yop, je m'incruste ici... j'ai commencé la resto d'un fourgon 508 de 1978.
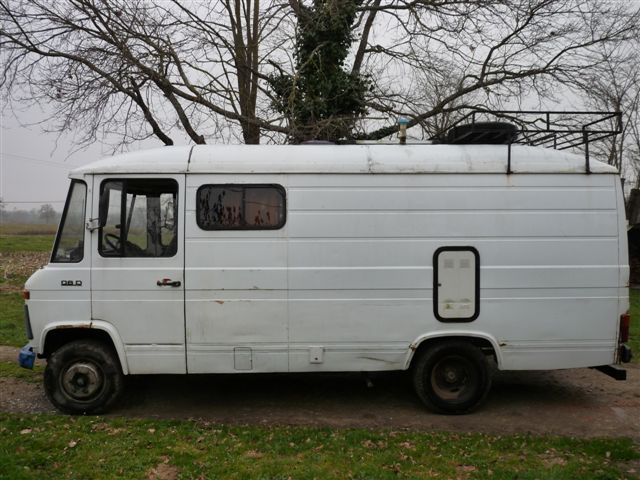
et comme ils commencent tous à prendre de l'age et à être perforé de partout, je partage une façon de faire parmi tant d'autres... excepté celle qui utilise du mastic, même fibré, pour restaurer une corrosion perforante.
c'est inéficace, même à moyen terme, et cela demande pas mal de temps aussi.
alors voila, je préfère me servir de cela
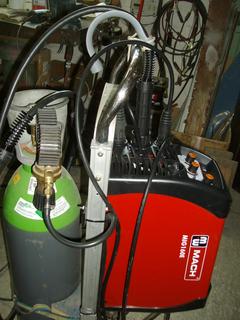
et puis ça aussi
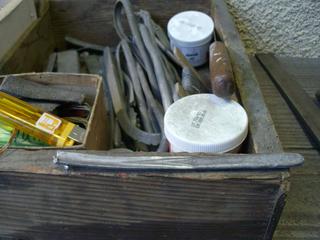
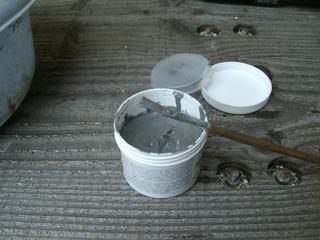
la technique de l'étain, avec un peu de pratique et surtout des barres à 33%, est pas si compliqué et surtout immédiate dans le résultat ! pas de temps de séchage.
par contre la préparation du support est longue et délicate quand on a des toles oxydées.
ça vas commencer avec ça
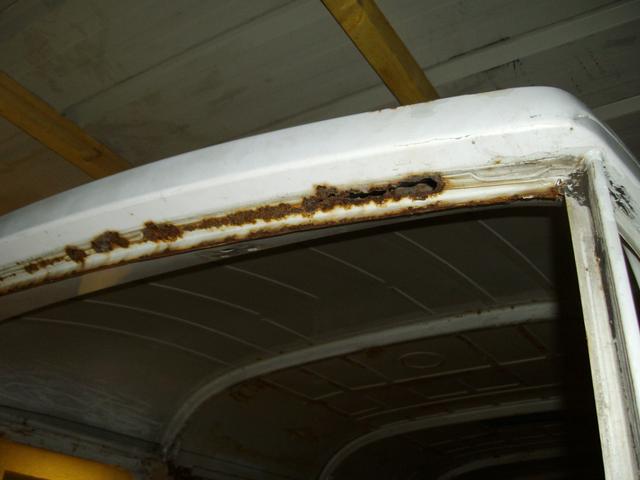
par précaution, sécuriser l' alignement de ce qui reçoit la courbure du par brise.
hostingpicson peut prépare la découpe
photo uploadhistoire d'avoir un belle ligne franche pour savoir ou l'on vas à travers les étincelles de la disqueuse
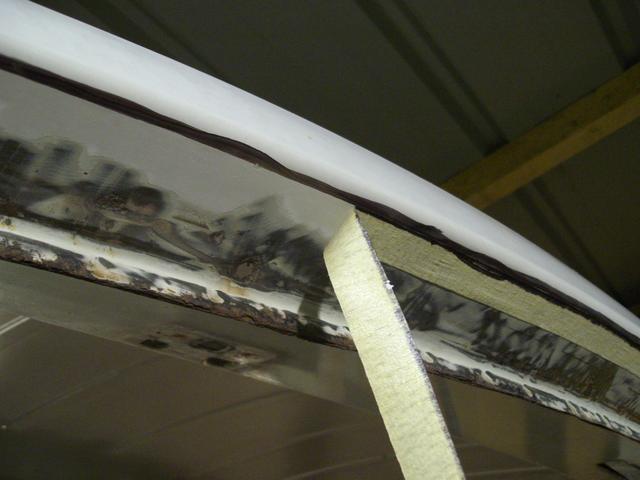
la disqueuse est passée
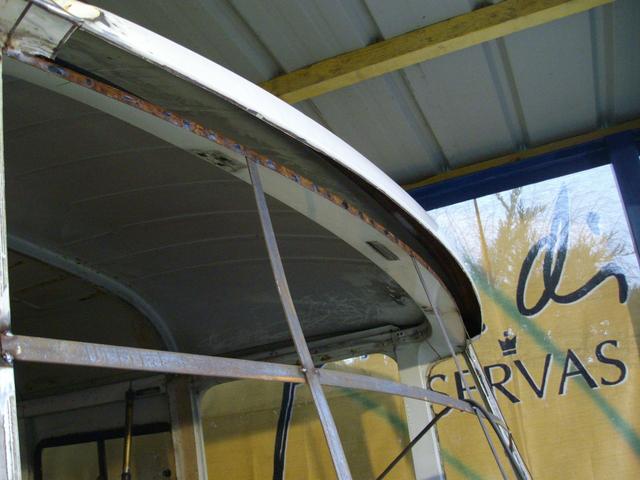
ce qui permet d'avoir accès à des parties cachées,
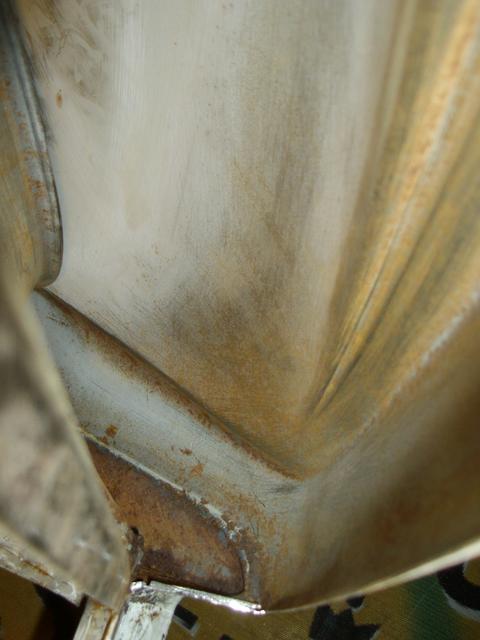
et faut en profiter !
un bon ponçage au papier gros grain 80 avec décapage jusqu'a la tole pour les parties oxydées. passage d'un dégraissant carrosserie et une couche impression phosphatant.
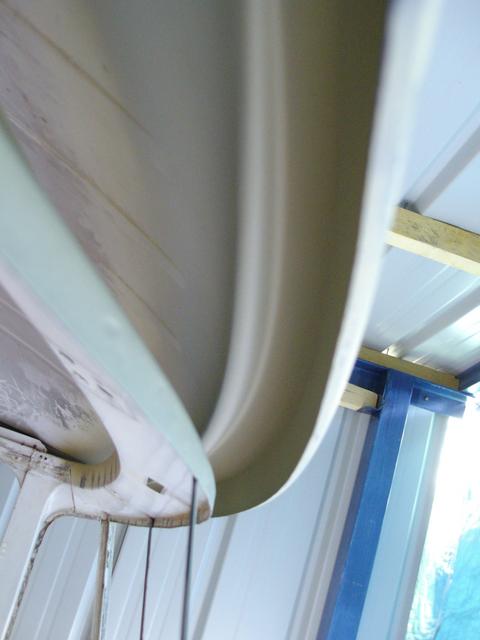
tout de suite, ça fait mieux.
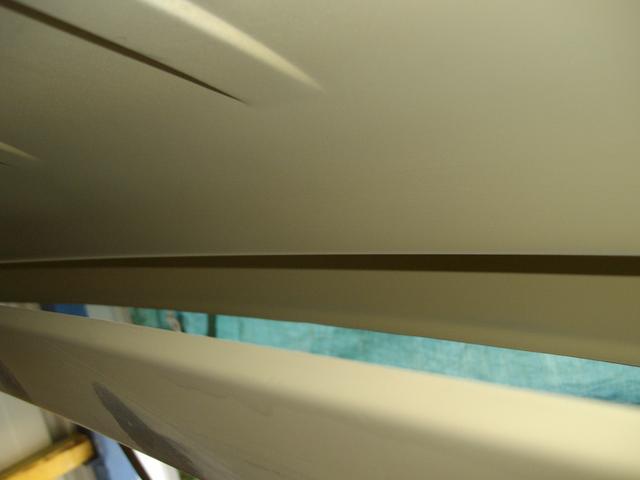
en parallèle et pour changer d'activité, la prise de la courbure sur carton, non alvéolée si possible, car ils sont pas assez rigide et cela complique une étape pas facile de précisions.
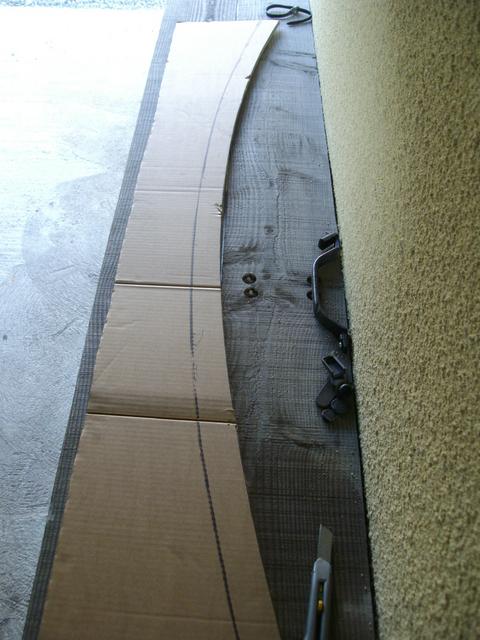
retour sur la préparation peinture,
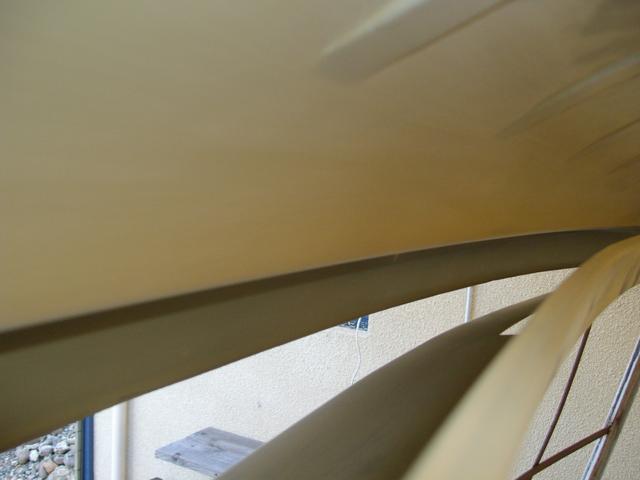
avec un dépolissage légé de la surface, à l'aide de scotch brite, un coup d'air comprimé et toujours un passage avec un chiffon imbibé de dégraissant carrosserie.
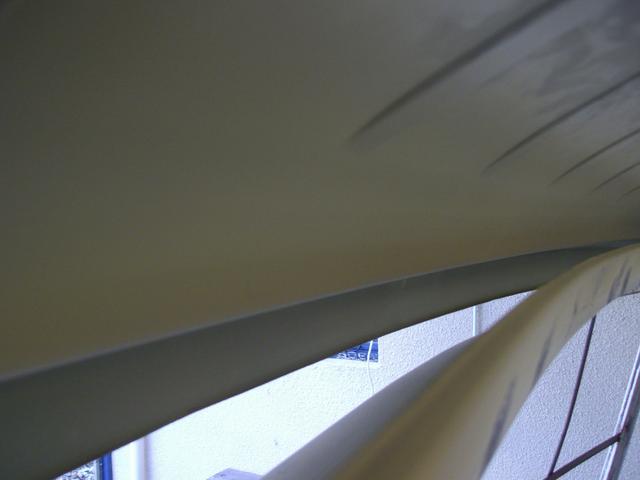
c'est pas flagrant la différence sur photo, mais indispensable avant la peinture, sinon, gros risque de non adhérence.
ce serait dommage pour une partie qui deviendra inaccessible après soudure.
on reviens sur la découpe de la pièce avec le patron en carton !
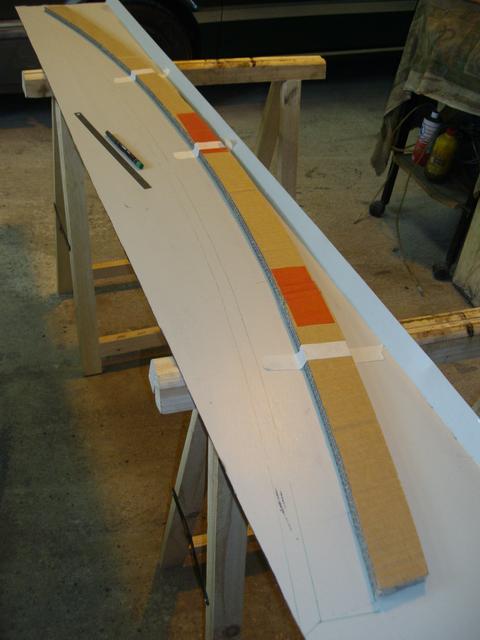
faut etre soigneux dans cette manip sinon on se prépare une prise de tete pour la suite.
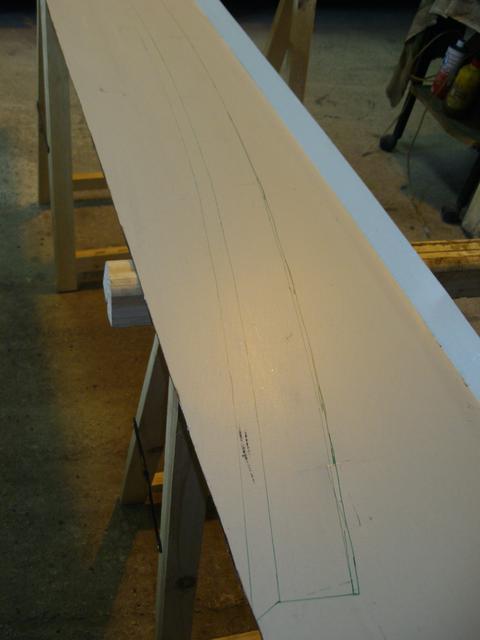
et la, précisément, avec le carton alvéolé qui se déforme à la moindre pression du stylo, j'ai préféré laisser plus de matière sur la courbure coté découpe disqueuse.
coté joint de par brise, il faut plier la tôle en suivant la courbure.
mais avant, la découpe
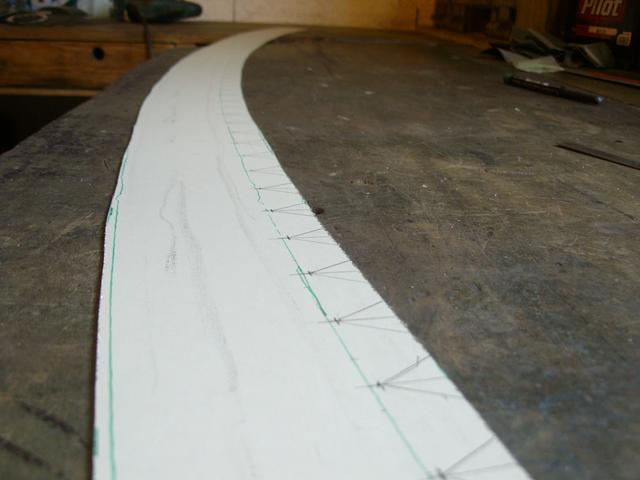
puis la préparation du pliage. laisser 2,3mm entre la ligne de marquage et la pointe de la découpe.
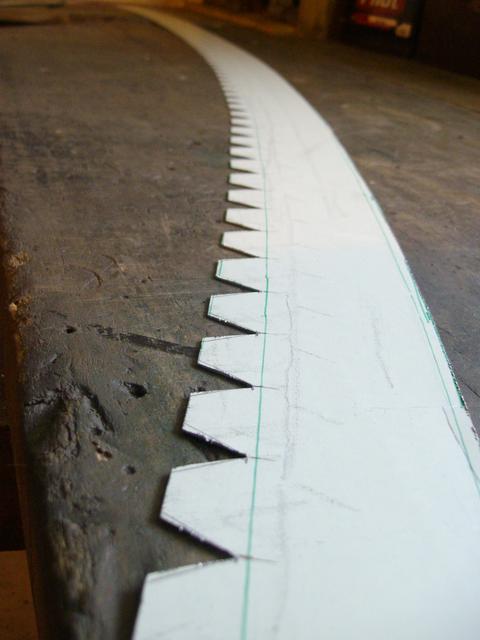
le serrage de la tôle se fait sous la ligne du stylo
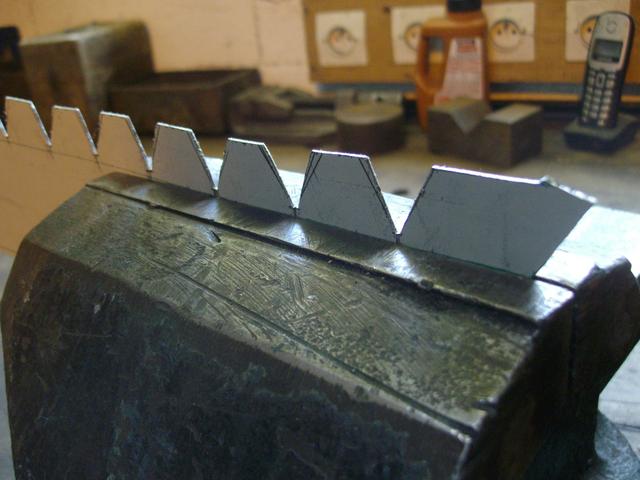
et le pliage en plusieurs étapes progressives. mettre un tas contre plusieurs dents de la partie a plier, et taper au marteau en pensant a plier avant tous l'embase de la dent.
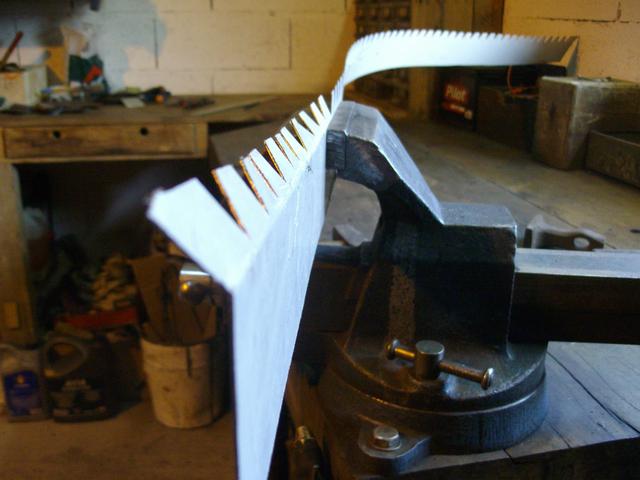
finir de plier... et c'est la que les 2-3mm montre leur importance. la pièce commence a prendre une courbure dans une rigidité toute relative, mais tellement agréable
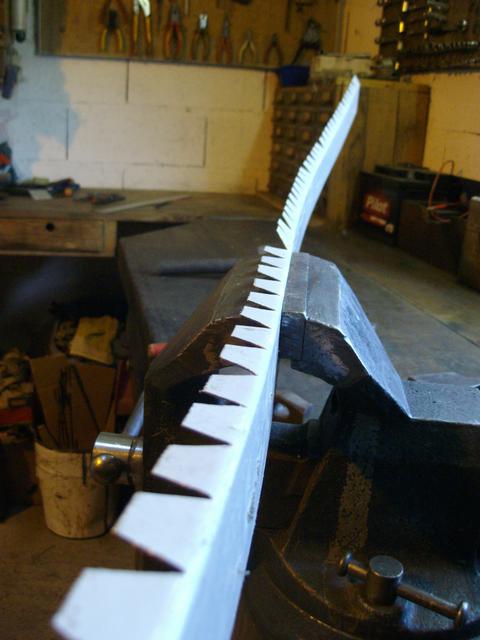
pofiner
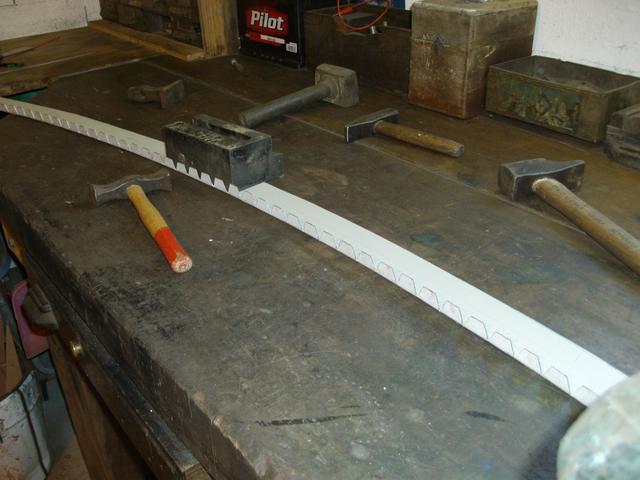
et la, grande interrogation... est ce que la courbure est respectée !
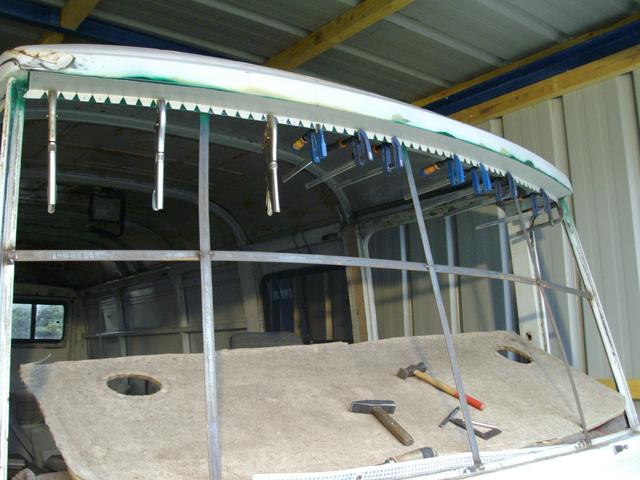
heureusement cette facon de plier peut s'adapter
on peut alors marquer, de l'intérieur de la cabine, la véritable courbure coté découpe.
etre précis une nouvelle fois, c'est ce qui vas déterminer la qualité "du bord à bord" de la soudure. Donc penser aussi a repérer la position de la pièce, par rapport à la caisse, avant de la déposer pour la découpe.
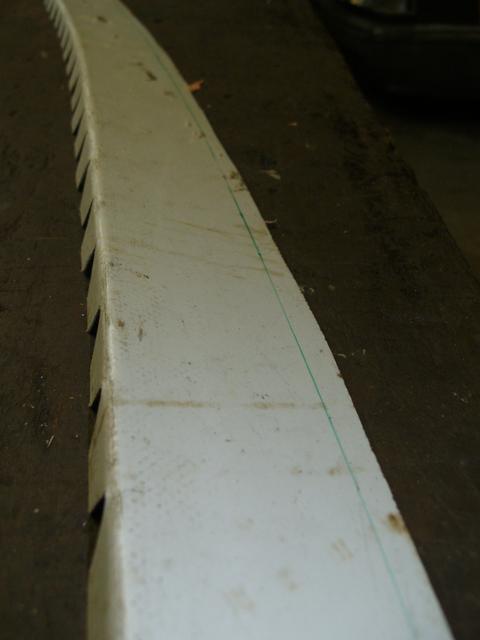
et faite pas comme moi

, penser aussi a poncer votre pièce avant de la plier.
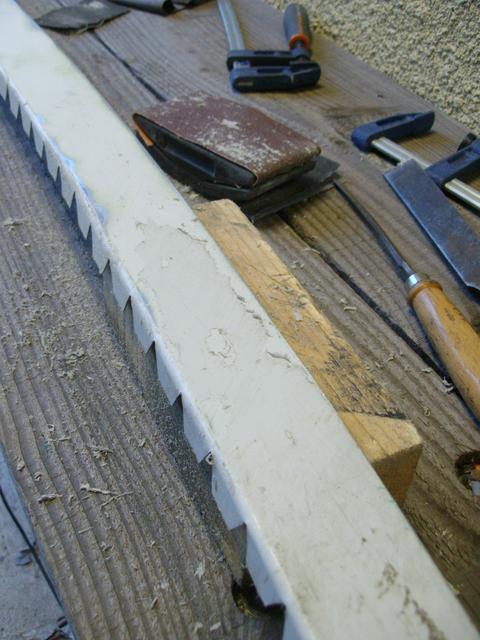
p'tite remarque, il faut essayer de respecter au plus pret l'épaisseur de la tole utilisée pour la pièce, avec celle de la caisse. plus facile de souder sans percer !
on repose la pièce découpée et poncée, en partant du centre et en reprenant le repère de positionnement ( marque au stylo vert ).
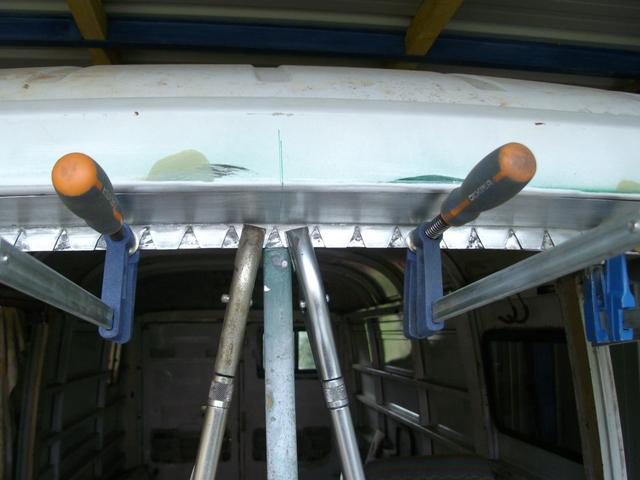
avec la partie d'origine de la caisse sur laquelle est soudée la pièce, bien poncée et propre ! ( la soudure déteste les vapeurs de peinture ou autre "brulés" par sa chaleur ).
comme en peinture, mieux c'est préparé,plus un résultat correct est facile. et pour le MIG et pour l'étamage du joint d'étain.
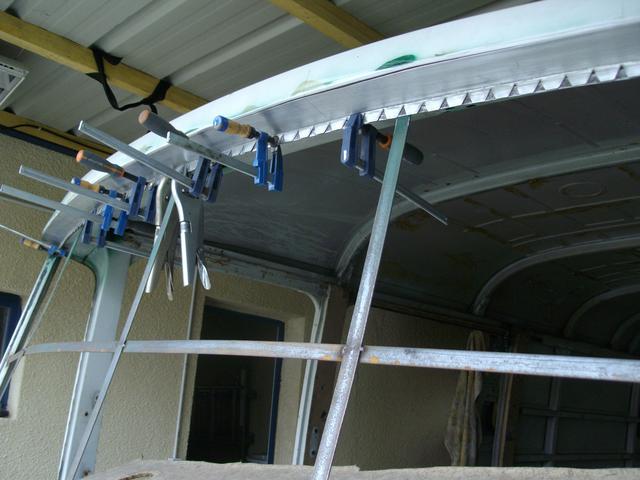
la pince du MIG proche de l'endroit a souder, et sur du métal non oxydé.
on peut commencer a souder les V des dents, après s' etre aligné soigneusement sur la partie d'origine, les uns à la suite des autres.
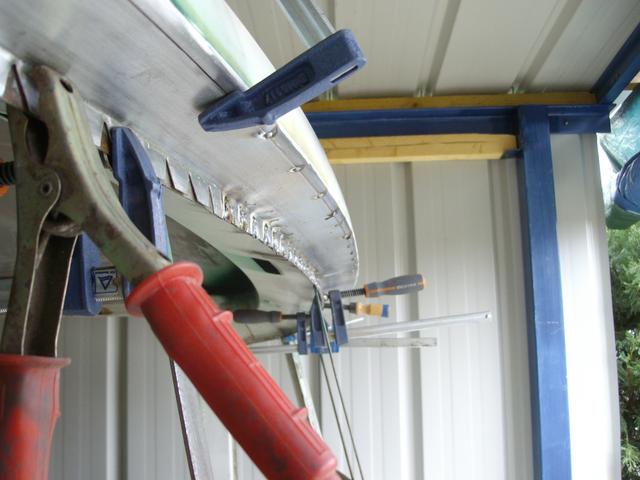
sur la photo, le coté gauche est fini. le coté droit commence, et en meme temps que l'on avance avec la soudure des V, on pointe le "bord à bord" coté découpe.
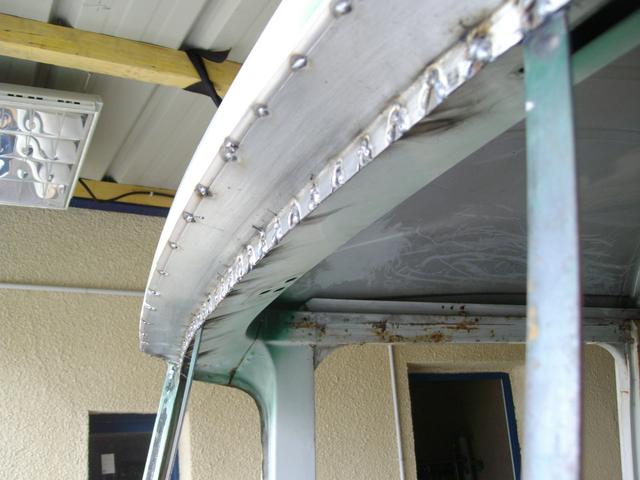
et on fini de souder entre les pointages.
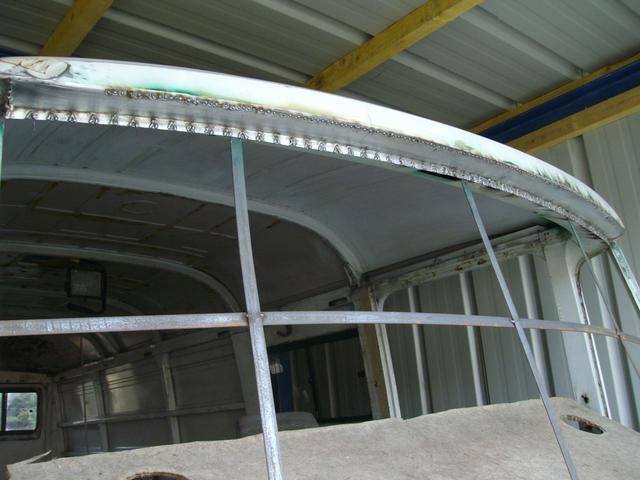
je soude par point, plutot que par petit cordons, car cela chauffe moins et la protection derrière brule moins. c'est plus facile aussi dans le cas de soudure par dessous, et moins de chance de percer !
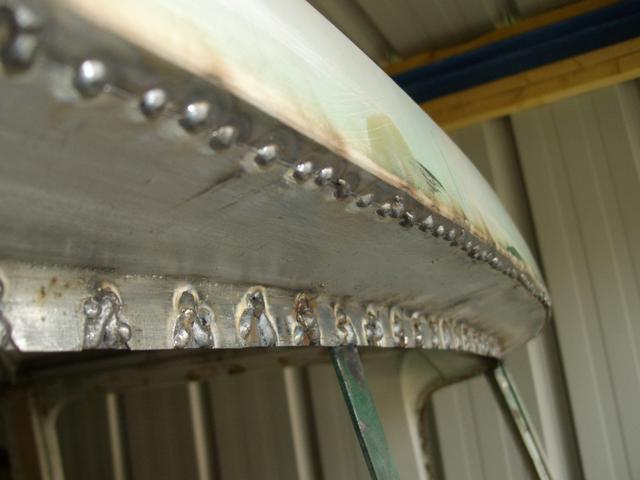
coté intérieur...
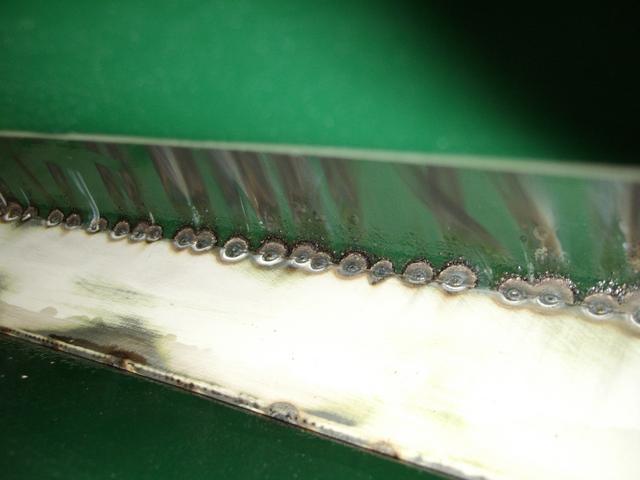
ya moyen de faire une soudure plus pénétrante en augmentant l'intensité du MIG, mais encore un fois, plus de chance de percer.
je préfère encore assurer et passer un peu plus de temps avec la disqueuse.
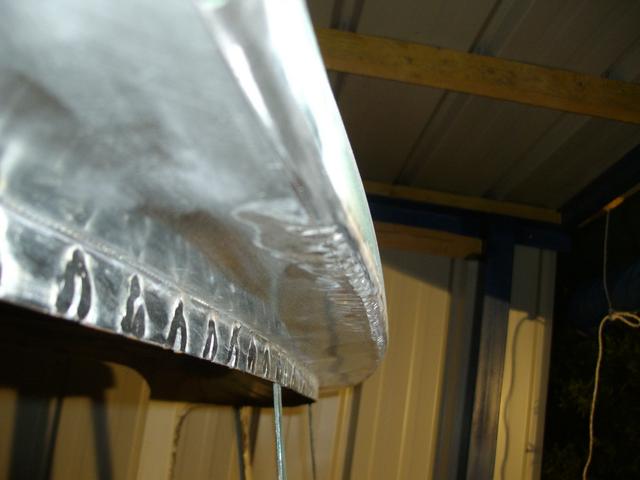
les minutes passent, à la grande joie des voisins !
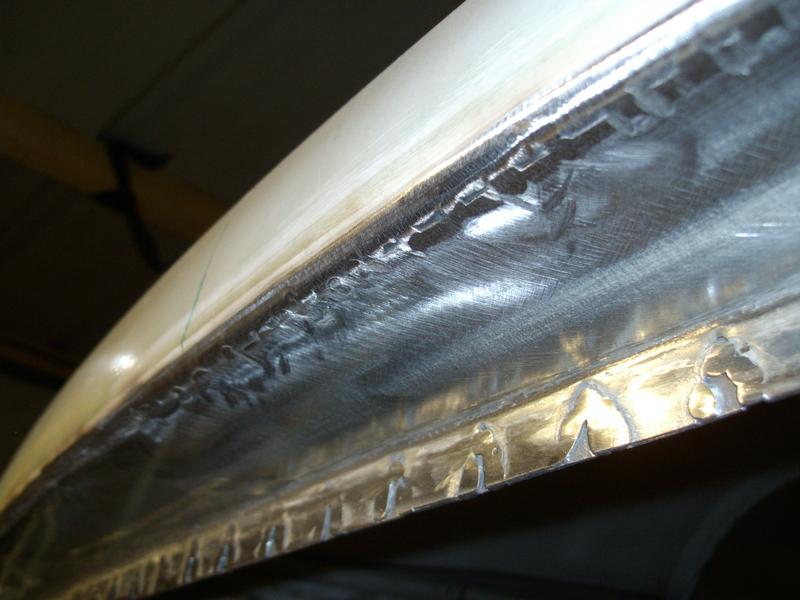
et pour les coins ou la disqueuse ne vas pas
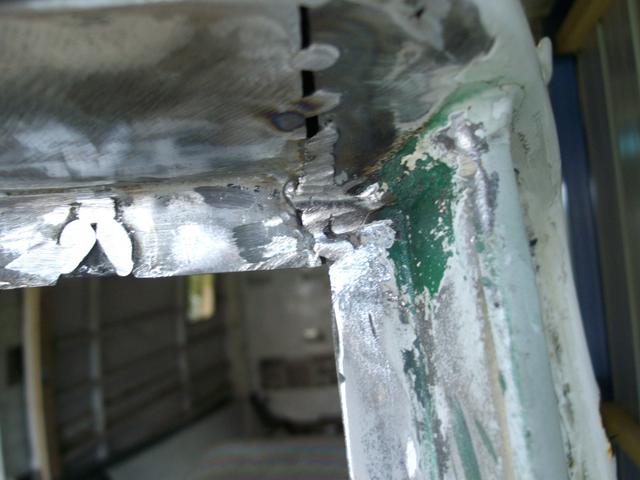
un petit outil bien pratique.
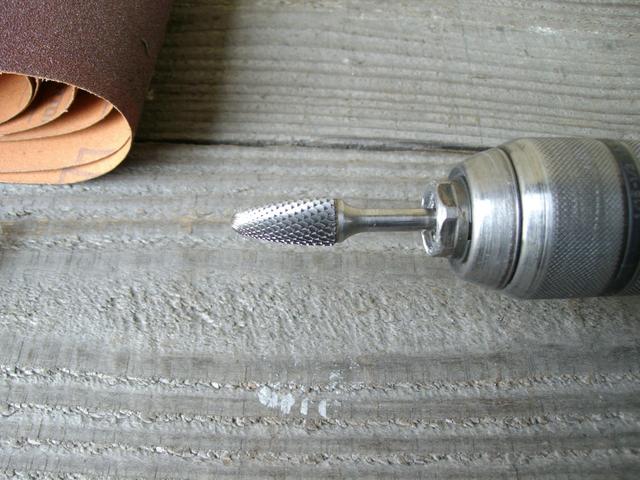
les soudures sont disquées en respectant l'épaisseur au niveau de la surface d'appui des joints.
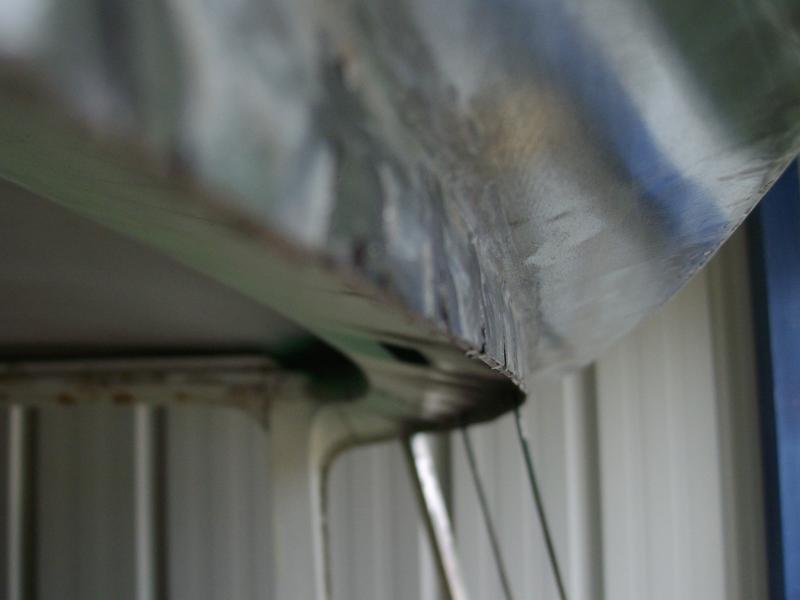
sinon, c'est un risque de fuite d'eau pour le par brise et un retour de la rouille.
après que le plan de joint soit fini, celui d'étain peut etre fait afin de rendre le tout bien étanche.

flèche rouge... encore un détail qui montre l'importance des 2-3mm.
flèche jaune, un autre détail pour montrer qu'il faut s'appliquer a tout décaper correctement les surfaces a étamer.
... à gauche, le grattoir n'est pas encore passé.
la patte a étamer a beau contenir de l'acide pour décaper l'acier, il faut enlever toutes traces d'oxydation jusqu'a retrouver du métal sain... sous peine de galérer, et au final, ne pas réussir à ce que l'étain pénètre dans ce genre d'endroit.
et meme si en surchargeant, on réussit à tout recouvrir, il restera de l'acide... fortement corrosif pour l'acier !
et c'est pas vraiment le but de la manip !

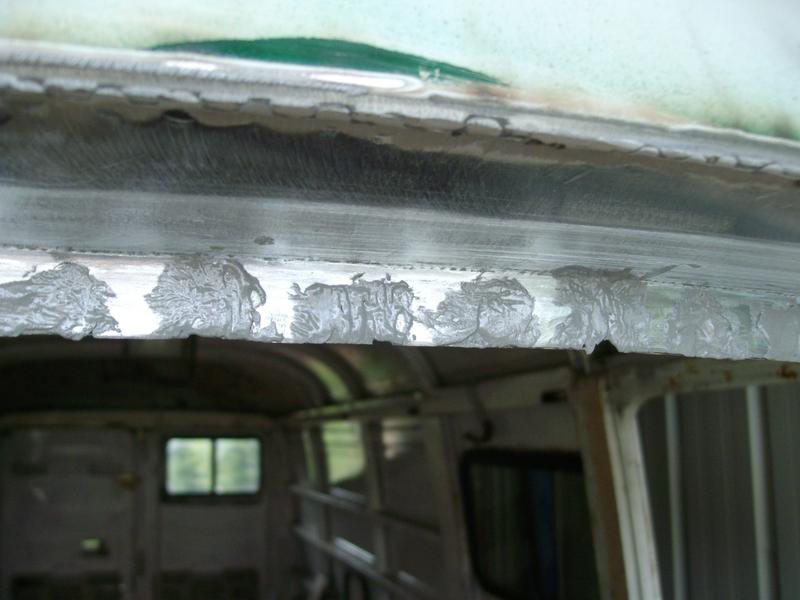
cela ne sert à rien d'en mettre beaucoup... la y'en a trop par exemple !
chauffer, avec un petit chalumeau à gaz, pas directement sur la patte a étamer, mais sur l'acier juste à coté.
ne pas mettre une grosse flamme et ne pas insister a rester longtemps sur un même endroit. il vaut mieux retirer la flamme avant que la réaction de l'étamage se fasse, quitte a répéter l' opération plusieurs fois, jusqu'a obtenir ça !
un grattage de la zone a étamer avec une spatule en acier, sur laquelle on vient mettre la flamme du chalumeau ( même principe que la pane d'un fer a souder) aide beaucoup la réaction a l'étamage.
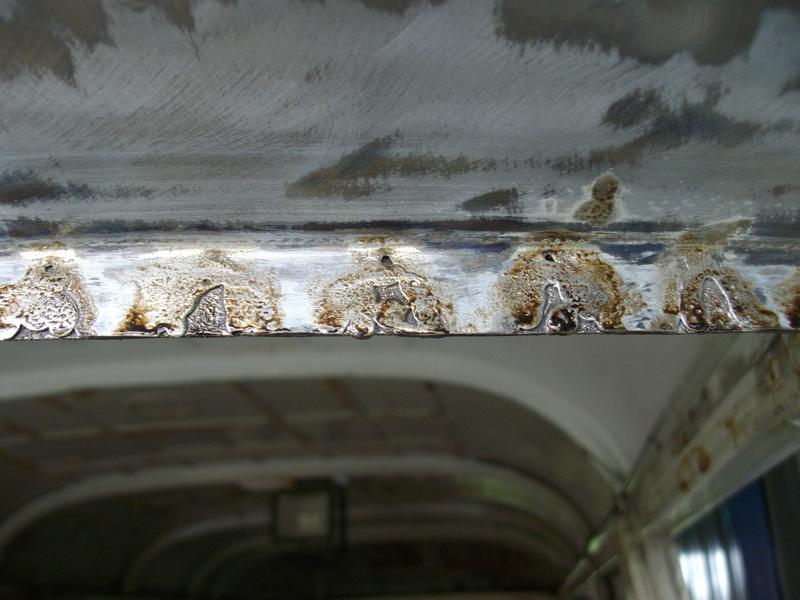
les traces brunes, c'est l'acide. en théorie, il faut l'essuyer avec une éponge mouillée alors que la tôle est encore tiède. mais dans certain cas ou l'oxydation est encore présente, ça aide de laisser l'acide lorsque l'on charge avec la barre d'étain. faut juste chauffer un peu plus la fusion de l'étain pour faire remonter l'acide a la surface.
chauffer doucement la barre d'étain sur son extrémité pour l'amener en température. et toujours par intermittence, chauffer la partie étamée pour la ramener en fusion. retirer la flamme, et appliquer l'extrémité de la barre sur cette partie. si au contact la barre d'étain de fond pas, il faut la frotter un peu sur la partie que l'on veut combler, mais sans trop appuyer sinon elle casse 2-3 cm au dessus.
il ne faut pas mettre la barre et la flamme en même temps sur la tôle, c'est ou l'un ou l'autre !
et on obtient un truc pas beau comme ça
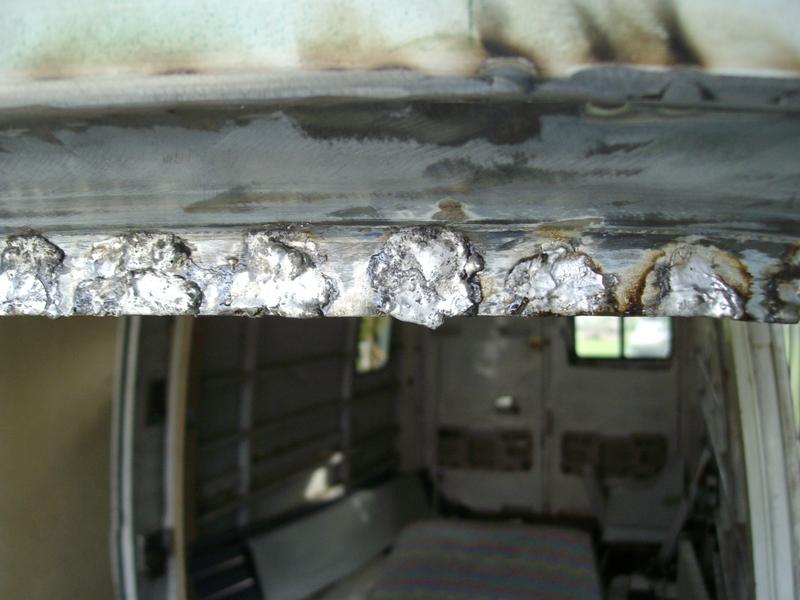
a ce stade, si l'acide n'a pas été essuyé apres étamage, il faut le faire encore tiède avec une éponge humide
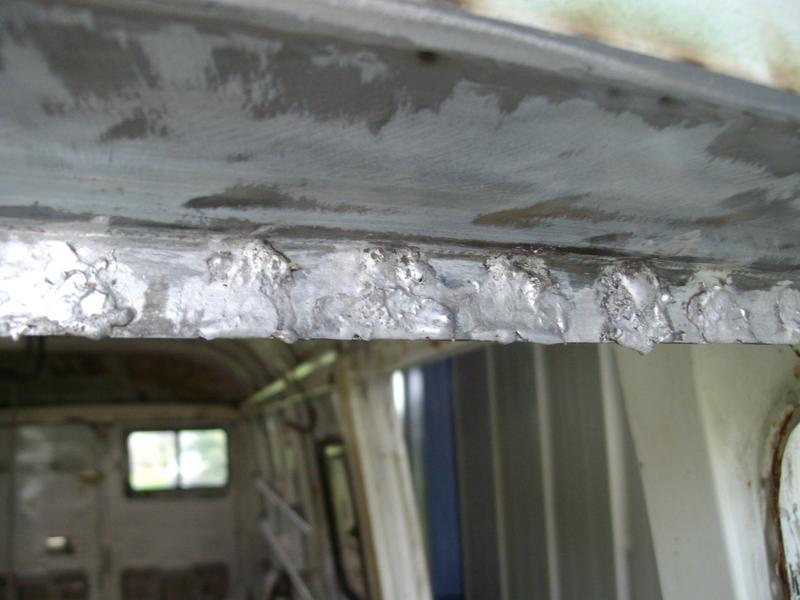
en rinçant régulièrement l'éponge. la peinture peut faire de sale réaction si c'est mal essuyé.
après, enlever le surplus avec un disque à lamelles en prenant la soudure du MIG comme repère pour conserver l'épaisseur
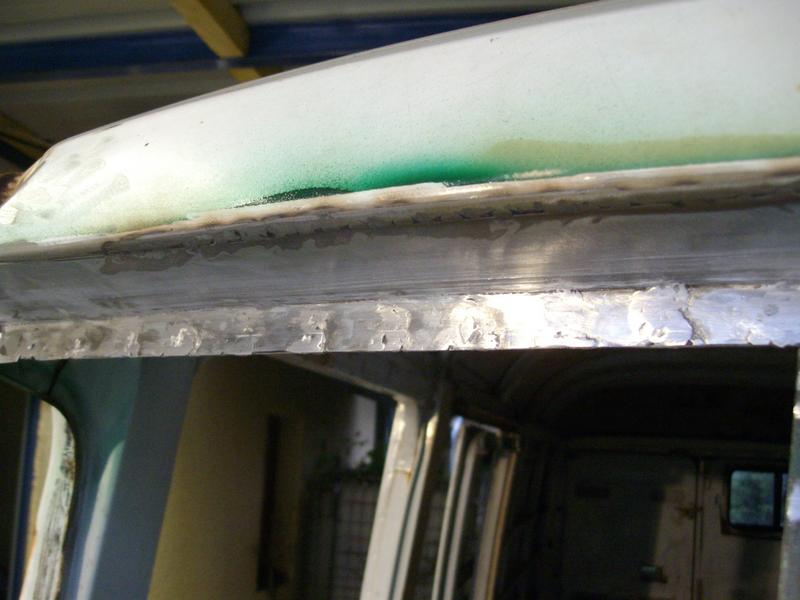
il restera toujours des petits trous dans l'étain, le mastic de carrossier fera tres bien la finition.
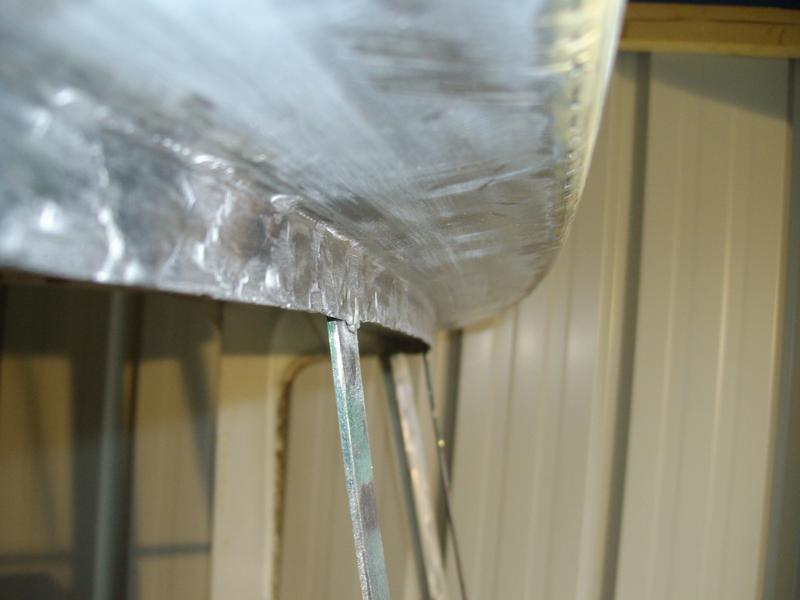
sauf que la, derrière un joint de par brise... j'ai bien mieux a faire
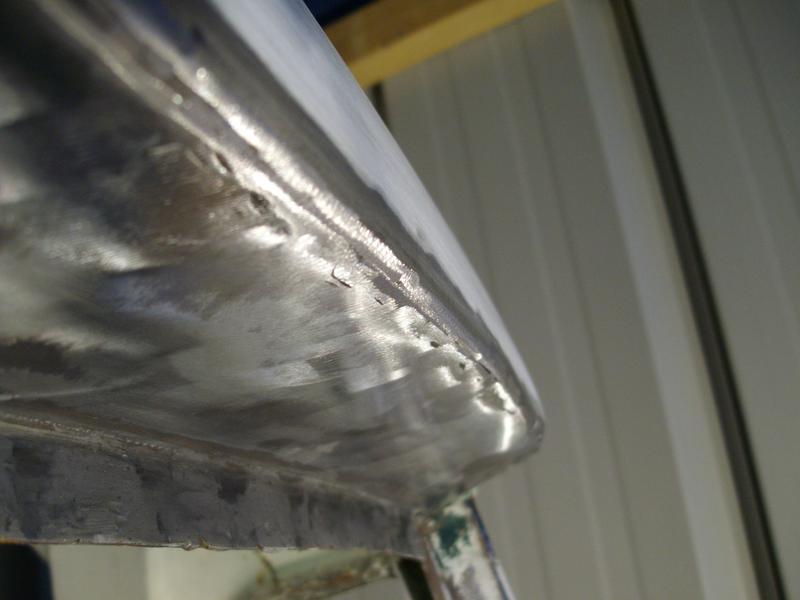
et ça recommence, patte à étamer
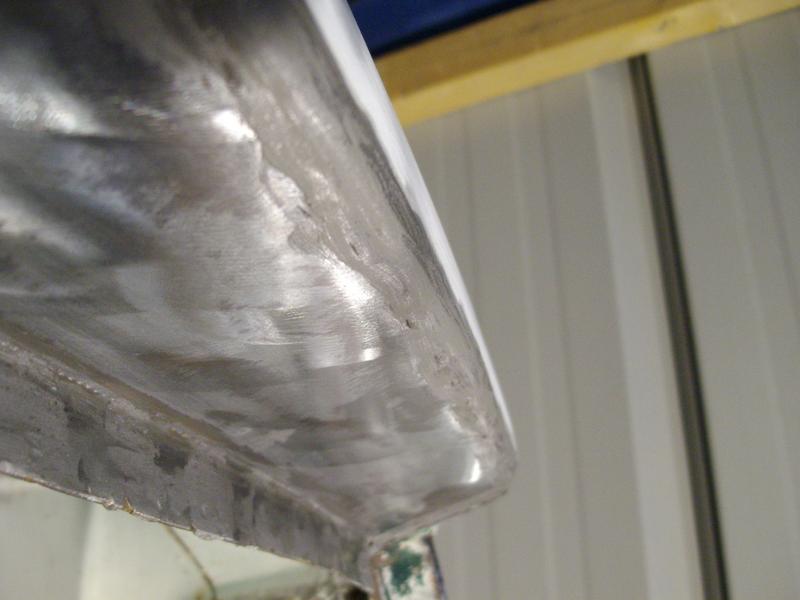
la tole est fine ici, alors tout doux la chauffe
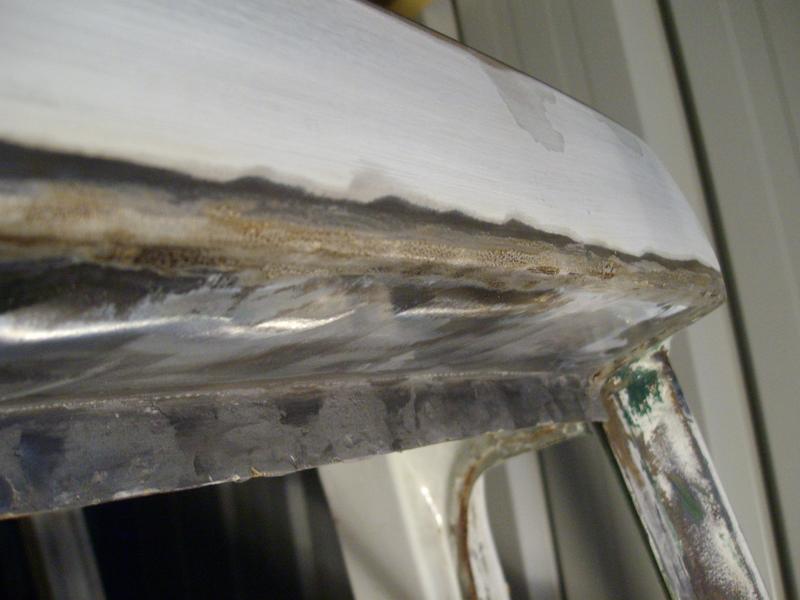
l'étain en surplus
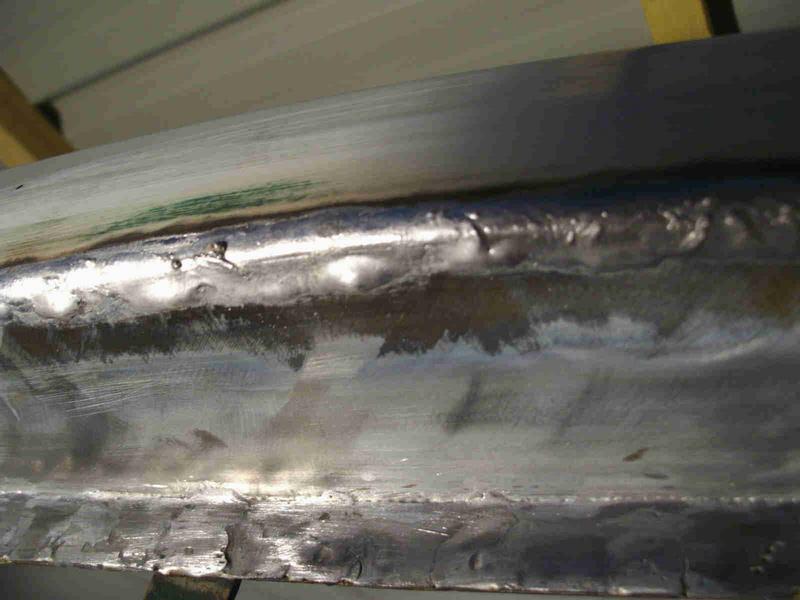
partout
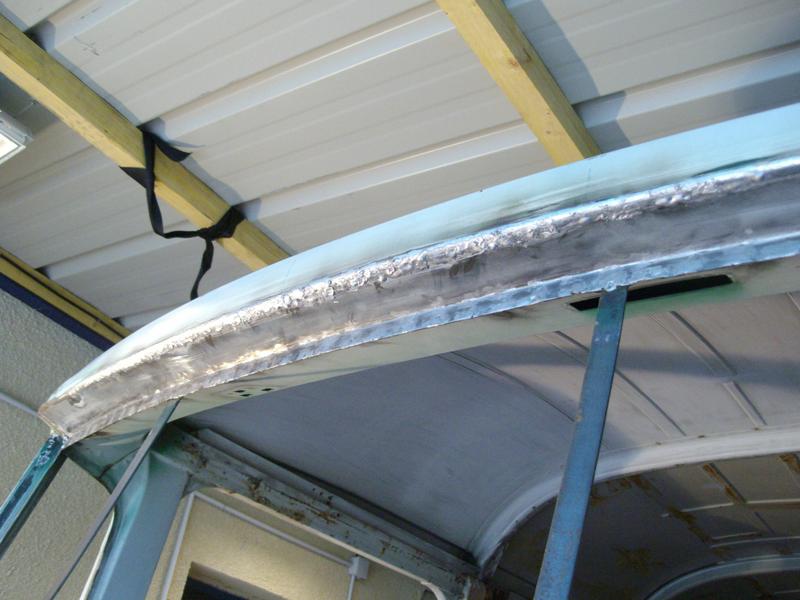
l' efficacité du disque à lamelles. pas trop de pression dessus, la tole ne doit pas devenir bleue !
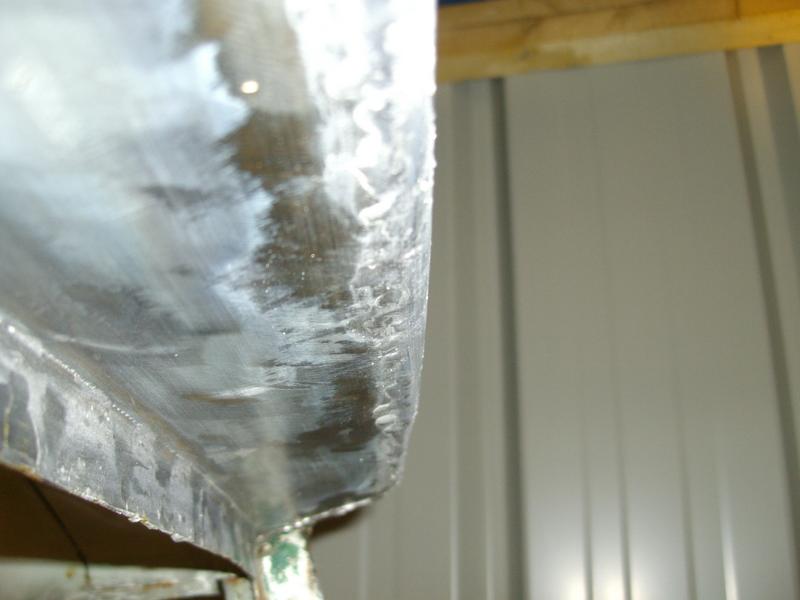
finition à la toile émeri de 80 et 120
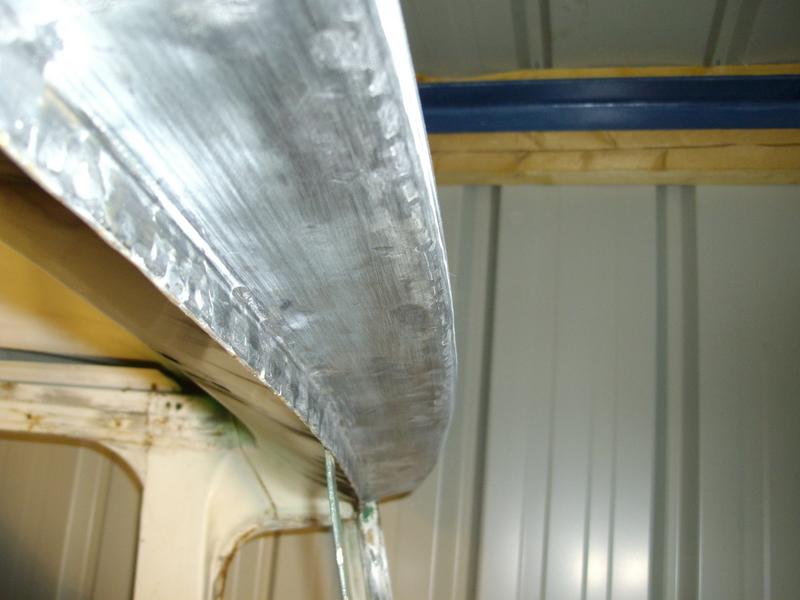
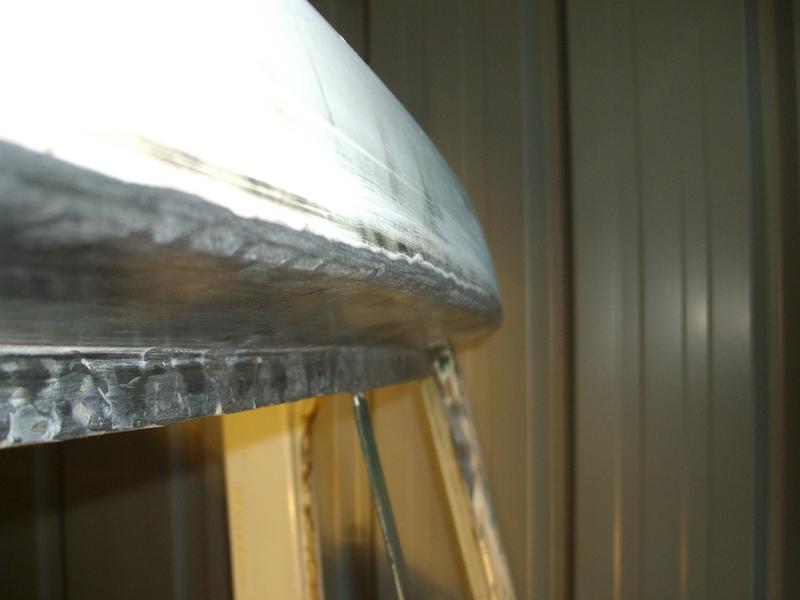
après vient la préparation à la peinture, sauf que pour ce fourgon, c'est la première pièce d'une longue série...
et ce superbe bigne sur le toit vas permettre d’essayer les greffons
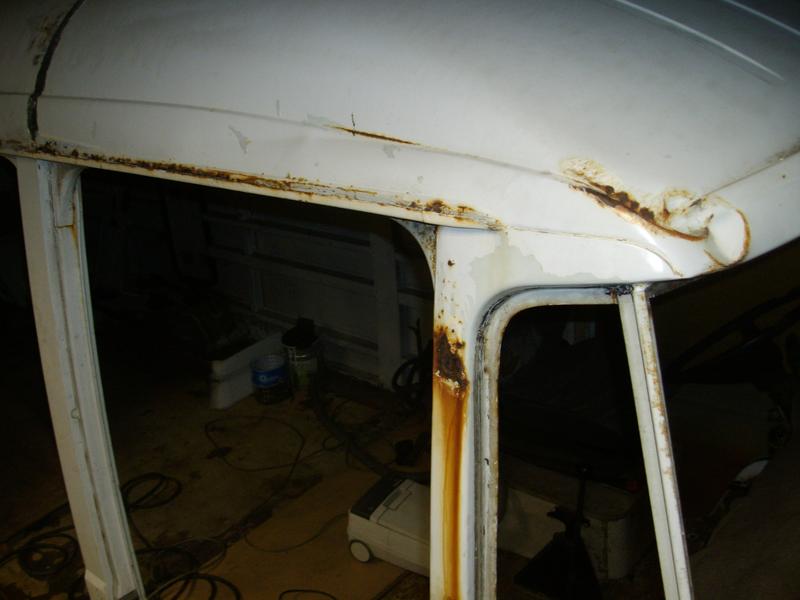
et d'un détail qui est pourtant une faille dans la conception de la cabine...
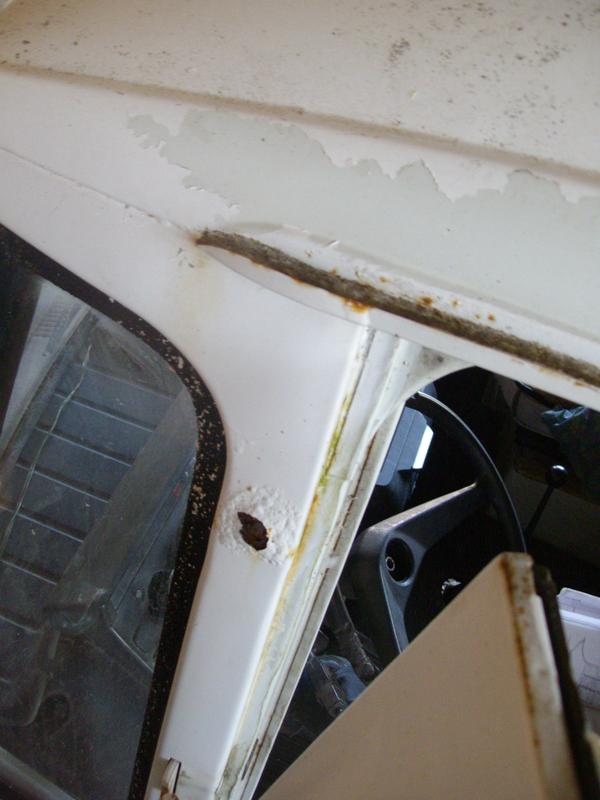
la gouttière n'a pas été épargnée non plus
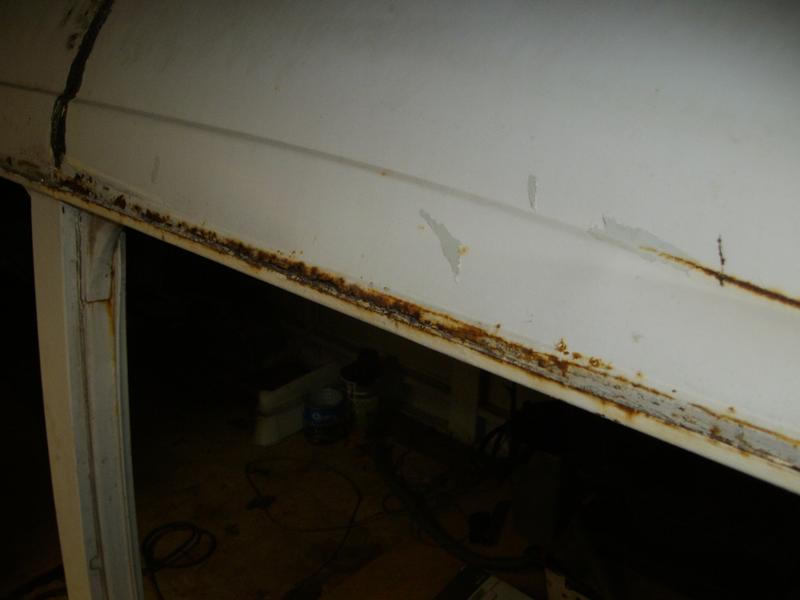
pour les reprendre, une découpe sur un 410 dans une casse
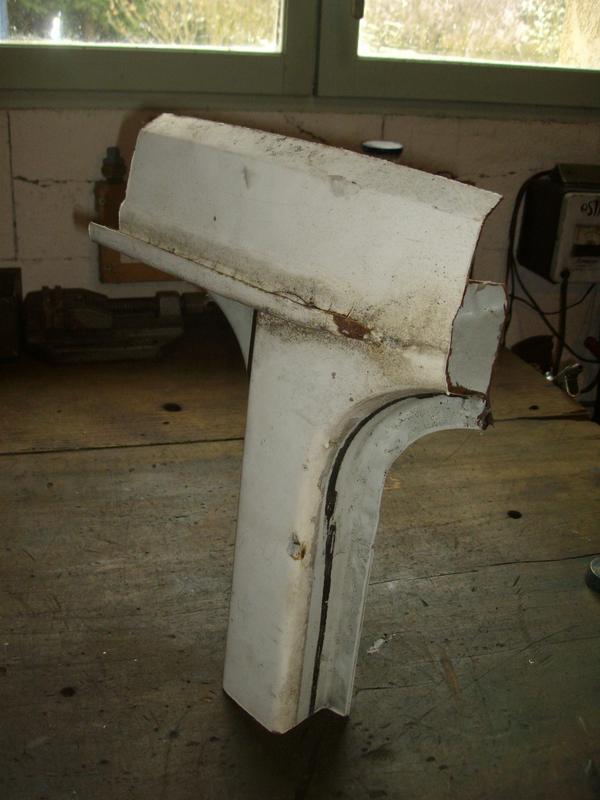
et sur un 508 fourgon plus récent ( direction assistée ) qui a brulé. avec une petite évolution de carrosserie qui se traduit par une fin de gouttière plus en avant.
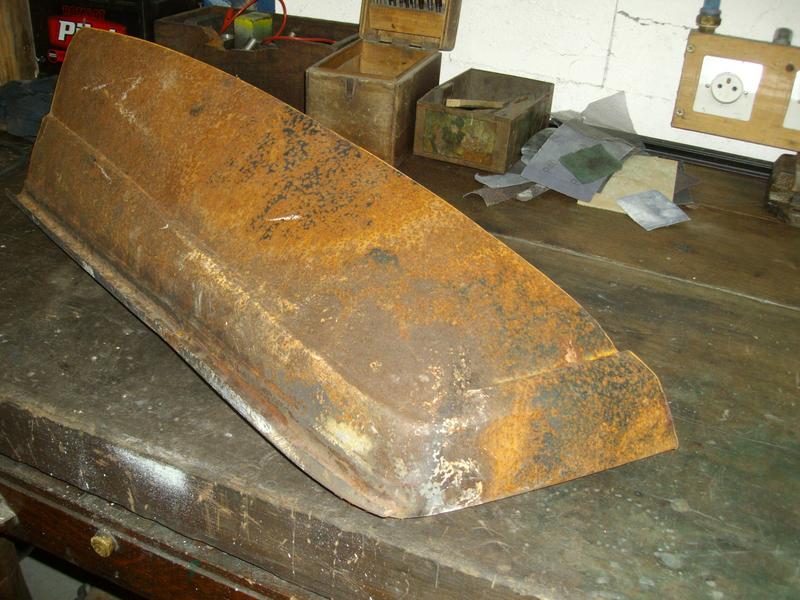
mais avant que le greffon soit prêt a être soudé, ya du taf ! parcequ'il faut lui dessouder tout les parties sur lesquelles il a été soudé, et qui sont venues avec la découpe.
découpe qui permet de voir que le procédé, employé en grande série, pour réaliser une gouttière n'est pas tres logique !
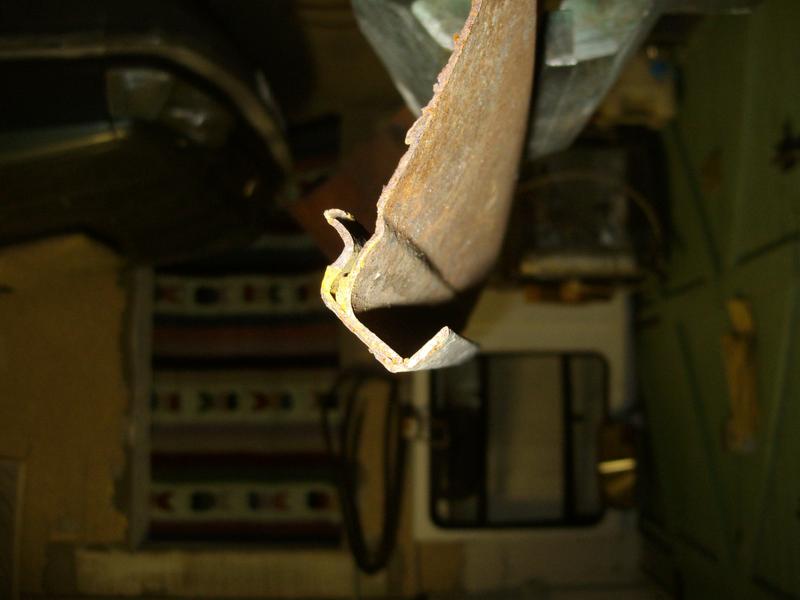
c'est l'explication au conseil de ne pas laisser des feuilles, terre ou autre qui retiendrait l'humidité a cet endroit.
surtout quand on sait que c'est par points que la soudure est faite, comme pratiquement partout sur une carrosserie.
et ces points, on les découvrent avec un coup de disque a lamelles.
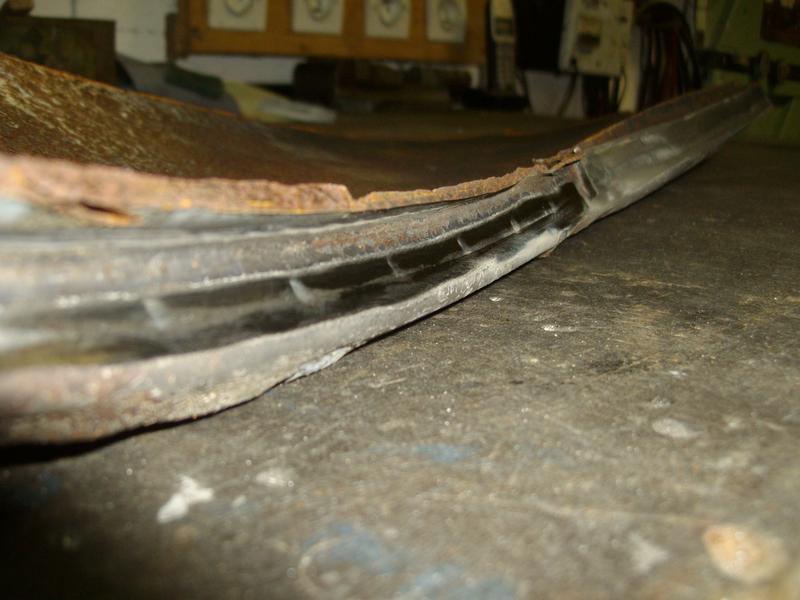
commence alors de longues heures de meulage avec la disqueuse tout en étant bien concentré a ne pas perdre de vue l'endroit du point, et a pister le moment ou la tole vas devenir bleue indiquant que la matière diminue.
le centre est alors de nouveau visible
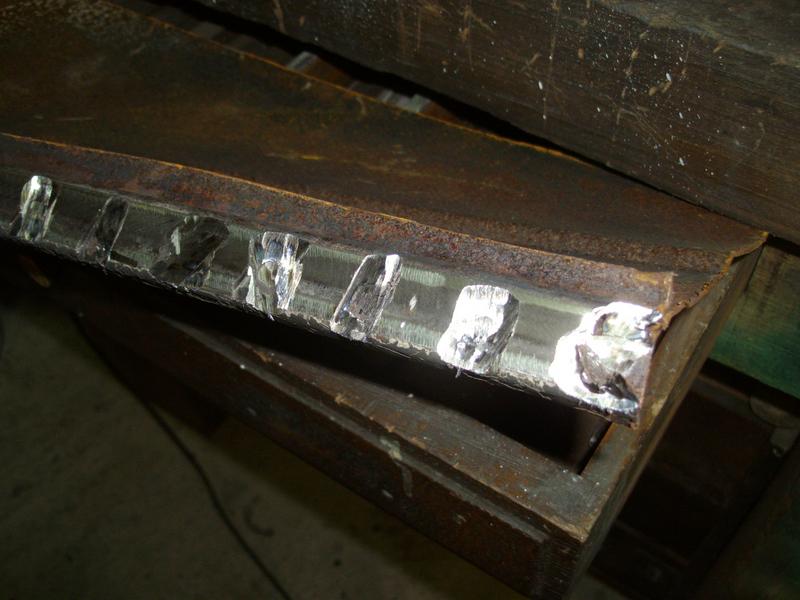
a ce stade, on peut essayer de glisser un ciseau a bois entre les deux parties ( coté droit contre la partie a conserver ) et de couper ce qu'il reste. ne pas insister si cela résiste.
il faut réaplanir la partie soulevée et reprendre la disqueuse.
ne surtout pas essayer d'arracher la soudure en pliant et dépliant plusieurs fois, sous peine de se retrouver avec ça comme résultat
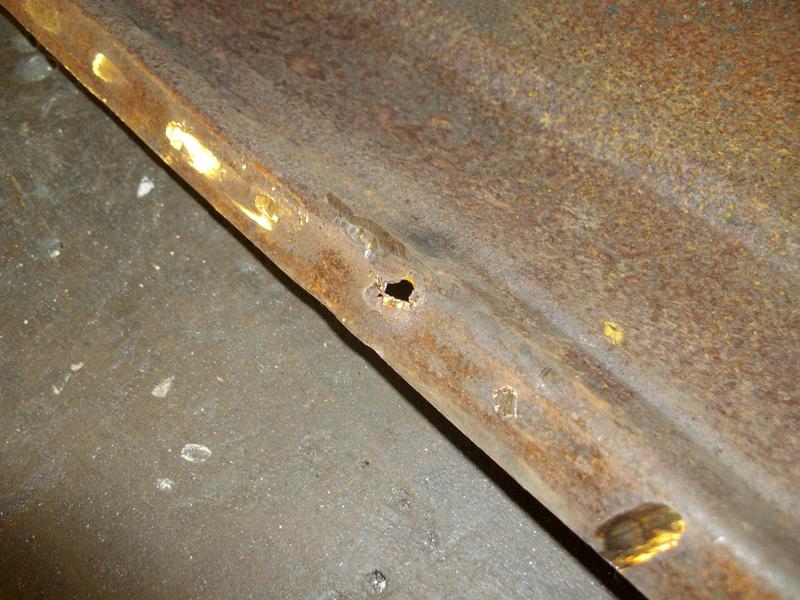
ce qui est logique car le greffon est souvent une feuillure extérieure fine, soudée sur une structure épaisse ! c'est donc lui qui cède en premier.
ça parait pas, mais le reboucher avec un MIG n'est pas facile, sauf si l'on peut glisser par derrière un bout de plaque en allu ou autre matière sur laquelle la soudure du mig n’accroche pas.
bref, point par point, ça se dessoude
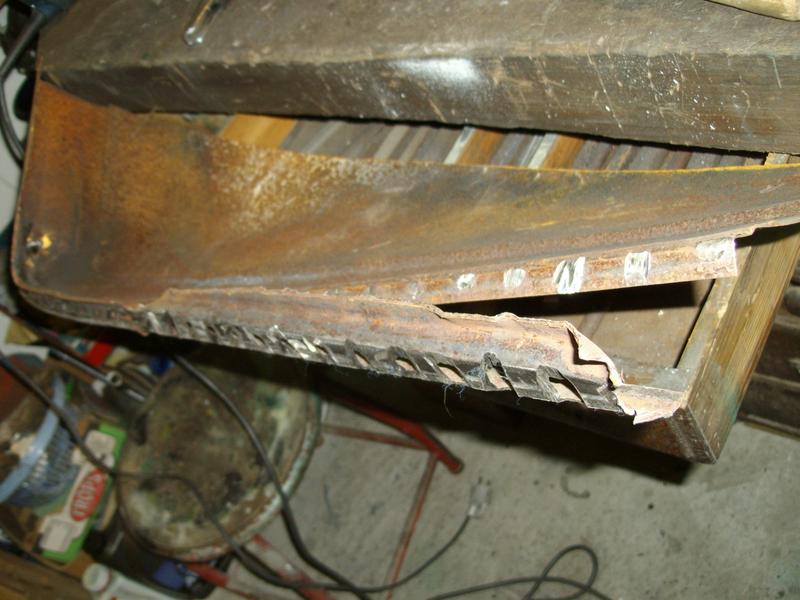
petite remarque, se servir de la tranche du disque pour meuler n'est pas bon car cela ne fait pas apparaitre de couleur bleue sur la taule, et c'est fréquent d' attaquer la partie que l'on veut garder sans s'en rendre compte. il ya un cas ou cela fonctionne bien, c'est lorsque l'assemblage des deux parties n'est pas pas parfaitement collé ou fortement oxydé. au lieu de pister une couleur bleue, c'est celle de la rouille qui dit quand s’arrêter. dans ce cas, il faut disquer autour du point,
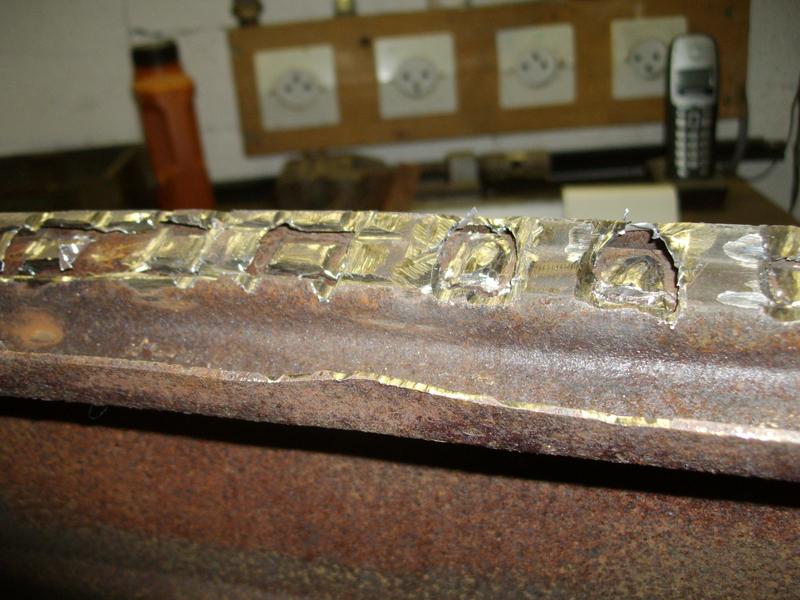
et une fois le point dégagé, finir de disquer la sur épaisseur. ça vas beaucoup plus vite et c'est plus facile !
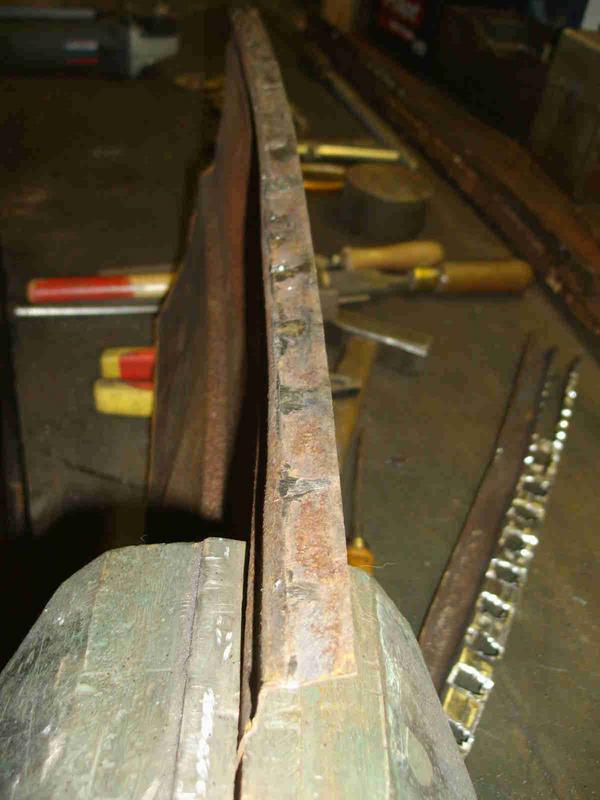
ce n'est pas tout, il ya aussi ce renfort de coin, bien épais et avec une tripotée de points inaccessibles.
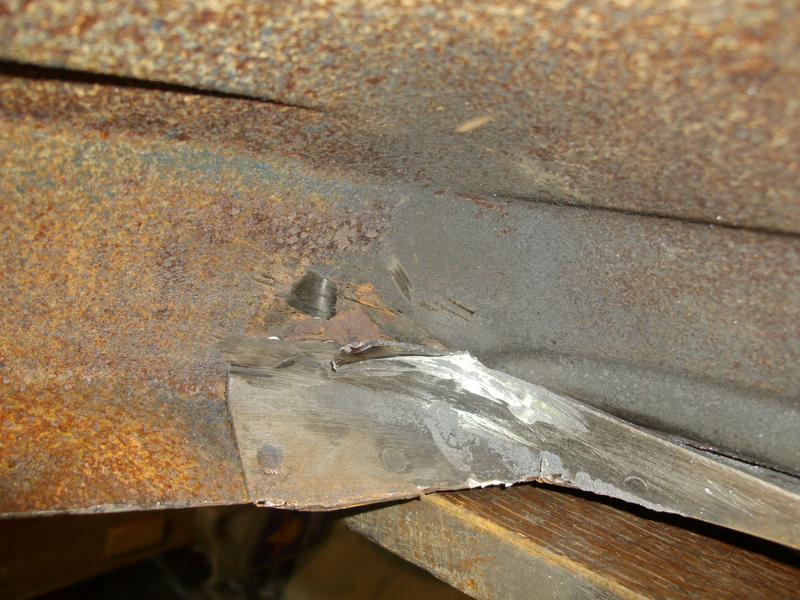
quand il faut meuler dans ce genre d'environnement, il vaut mieux avoir des disques de différents diamètres.
donc penser, sur des taf plus accessible, a stopper l'utilisation de différent disques avant l'usure complète, pour les stocker et les utiliser dans ce genre de cas.
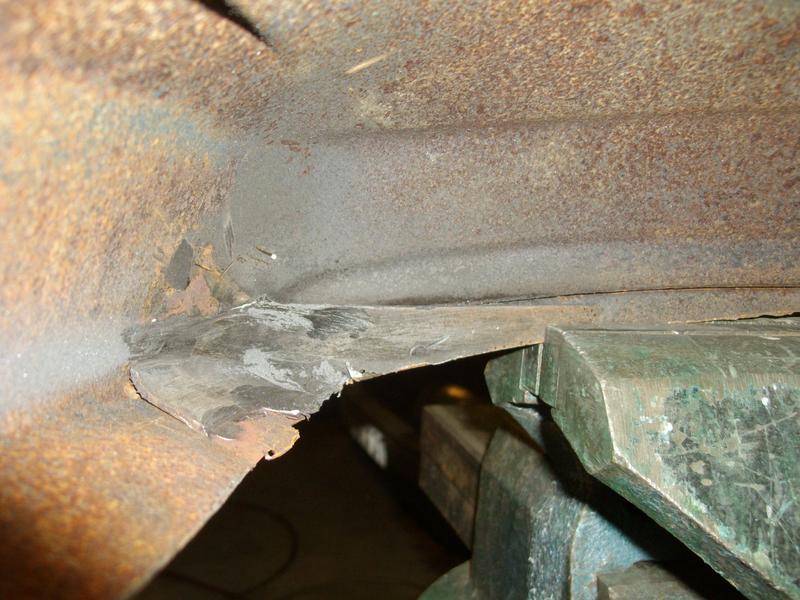
rester concentré sur la globalité du disque car on a vite fait de ce concentrer a l'endroit qui est concerné et d'oublier que ça peut toucher ailleurs, et en particulier sur la partie à conserver !
finalement le greffon est enfin prêt
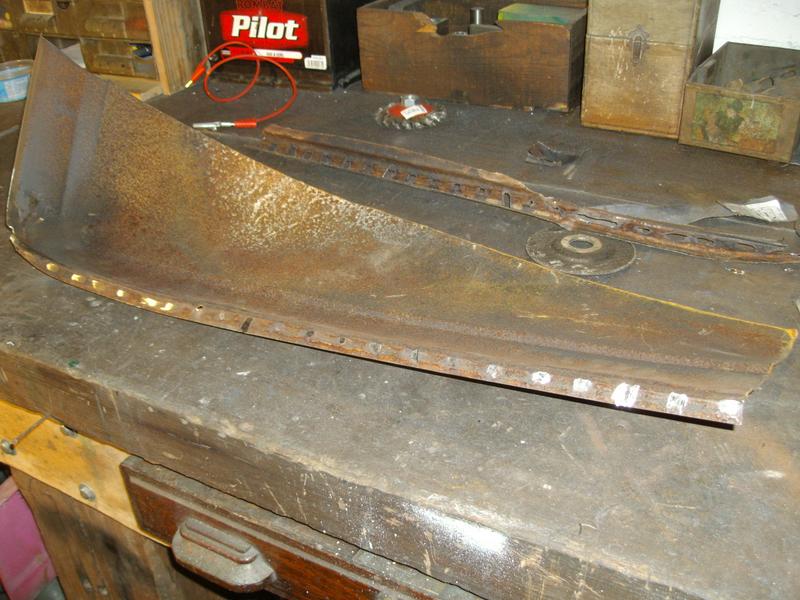
enfin presque... vaut mieux le préparer aussi pour la peinture pendant qu'il est sur l'établit . donc un bon ponçage a la toile émeri de 40 pour ce genre de cas
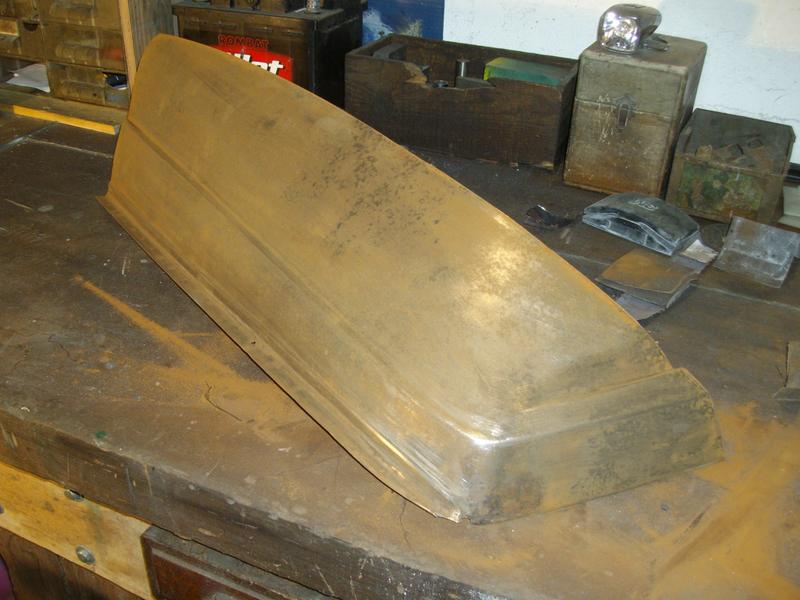
et une couche de protection...
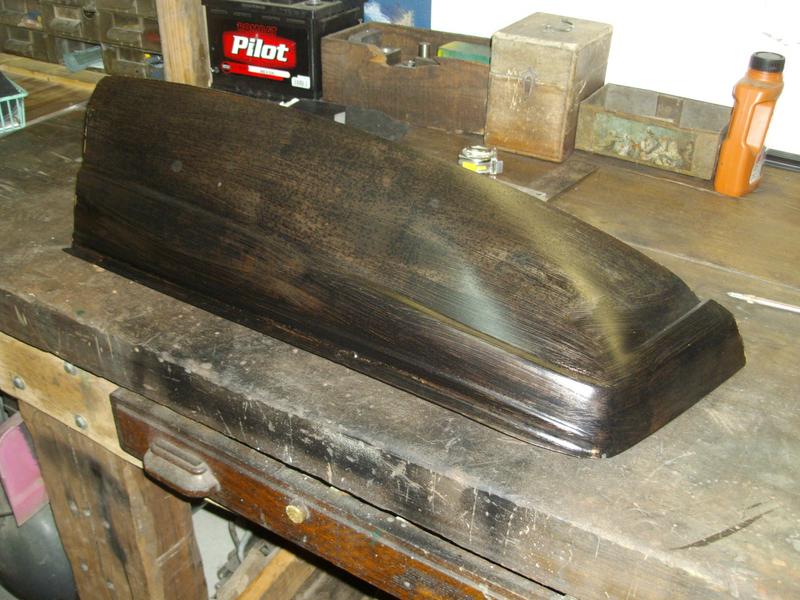
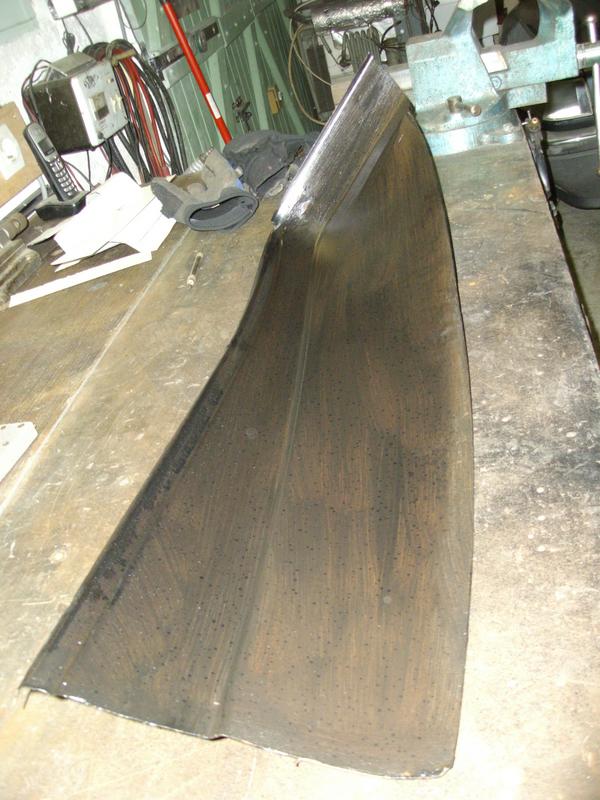
avant de le...
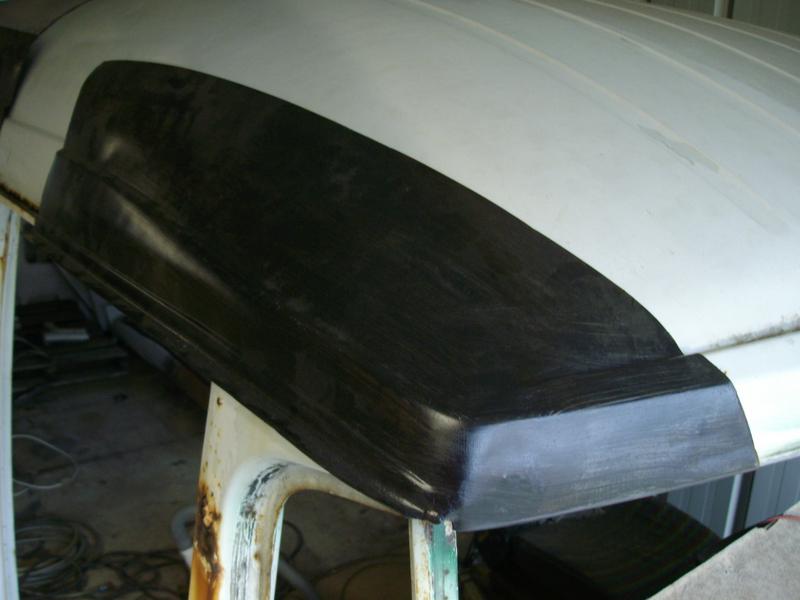
bin non parceque en fait, ce n'est pas le moment de le souder. comme pour la baie de par brise, la découpe de la carrosserie vas permettre l’accès a des endroits qu'il serait dommage de ne pas traiter.
et en particulier l’accès au montant de la portière... le fameux détail vu un peu plus haut !
donc on trace la partie a découper, plus petite que le greffon préparé... le bord a bord ne se fait pas maintenant car tan que la découpe n'est pas faite, le greffon ne peut être que superposé et donc peu de précision sur le positionnement .
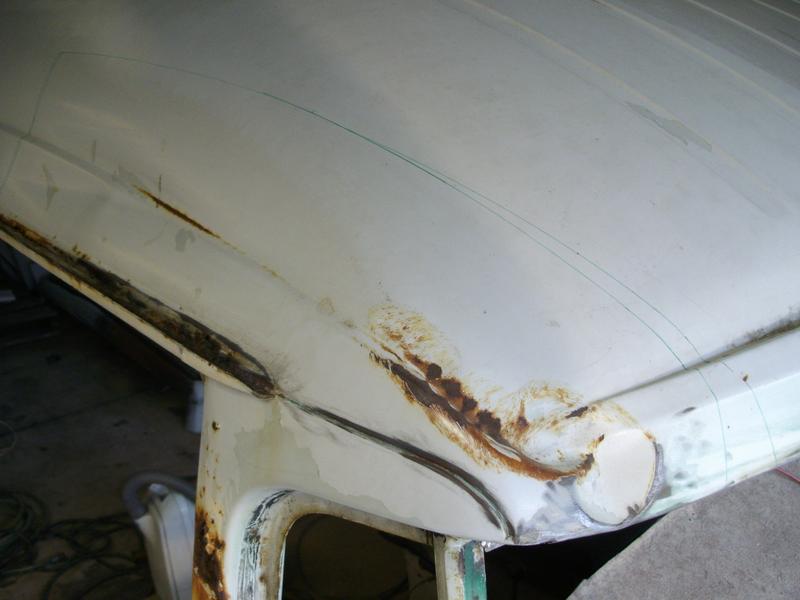
quelle vue !
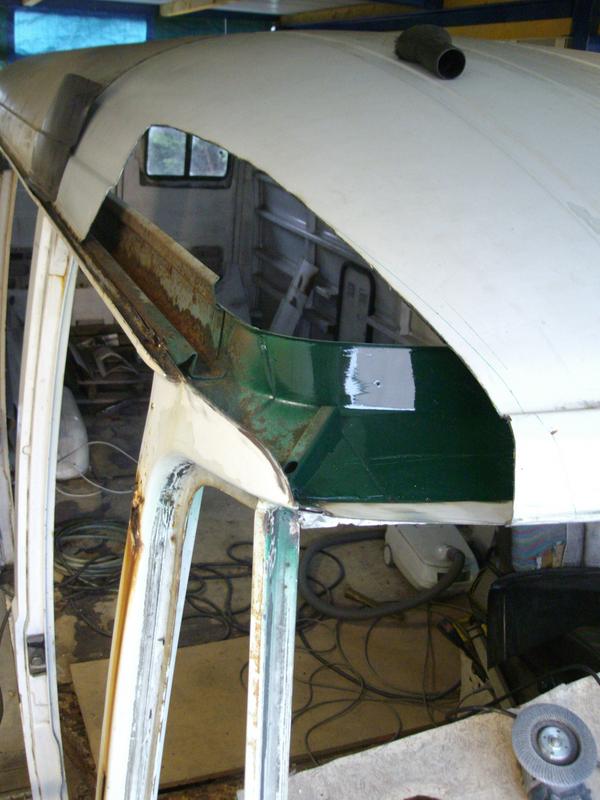
un peu plus près
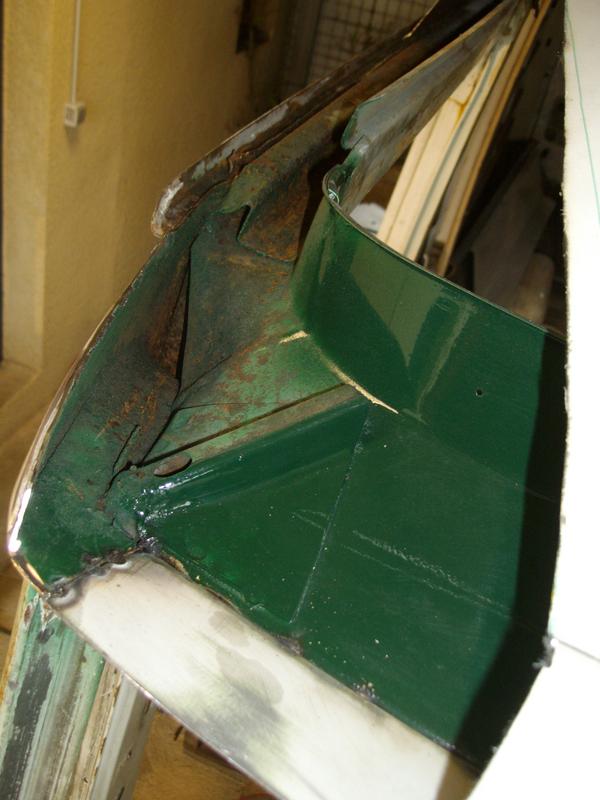
et la découverte de la faille ! une jolie cornière de renfort en doublon avec la feuillure extérieure
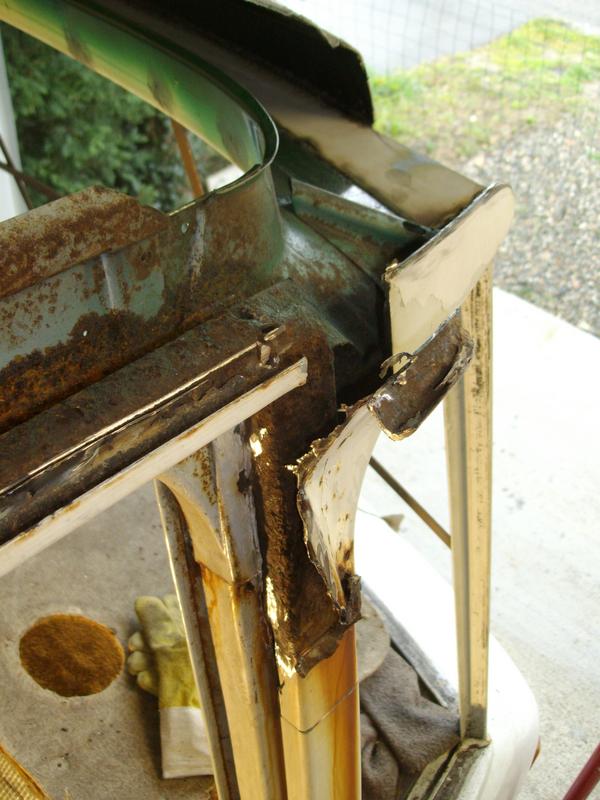
un peu dégagé, un peu gratté
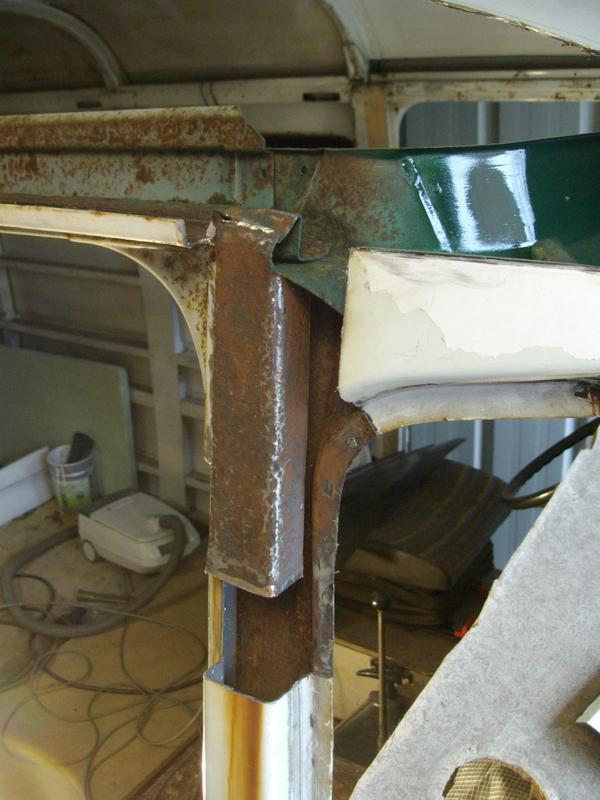
j'ai rien dit sur la découpe...
quelques conseils pourtant. elle doit se faire de préférence le long de pliure ( quand c'est possible ).
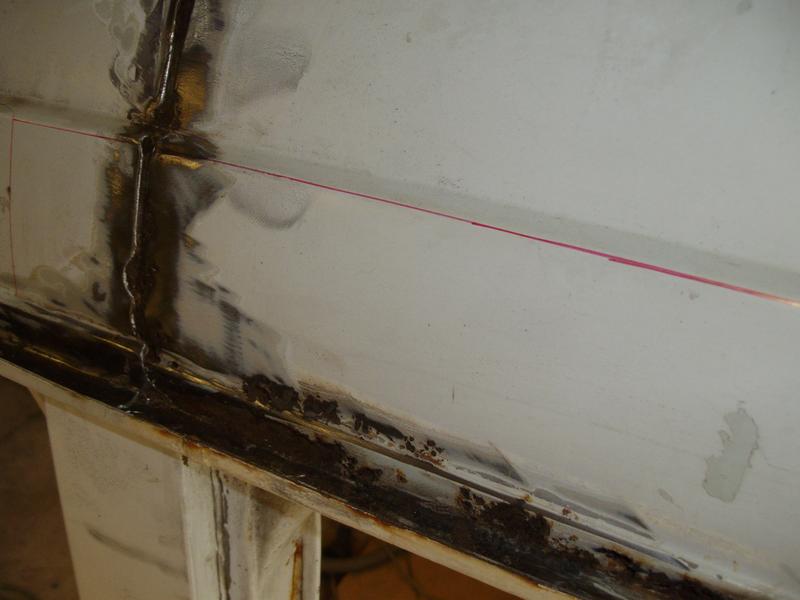
la tôle gardera plus sa rigidité, et pour réaliser le bord à bord, c'est plus facile.
il faut toujours garder à l'esprit qu'après la découpe, il faut souder donc avoir un champ de vision possible avec la tête + le masque à souder (qu'il faut pouvoir mettre et enlever)... pas toujours évident dans certain cas.
donc bien réfléchir sa découpe en fonction des parties rouillées et du reste !
coucou la rouille
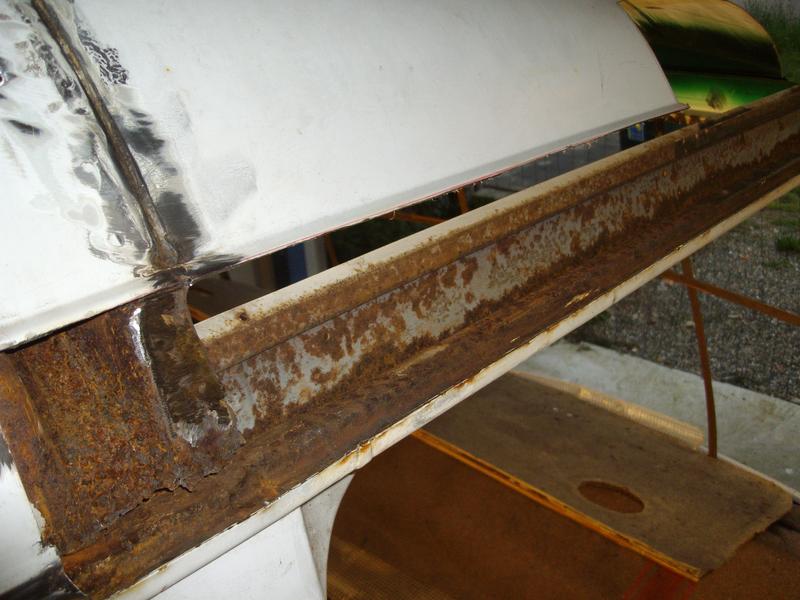
il faut penser a ébavurer de suite après la découpe...
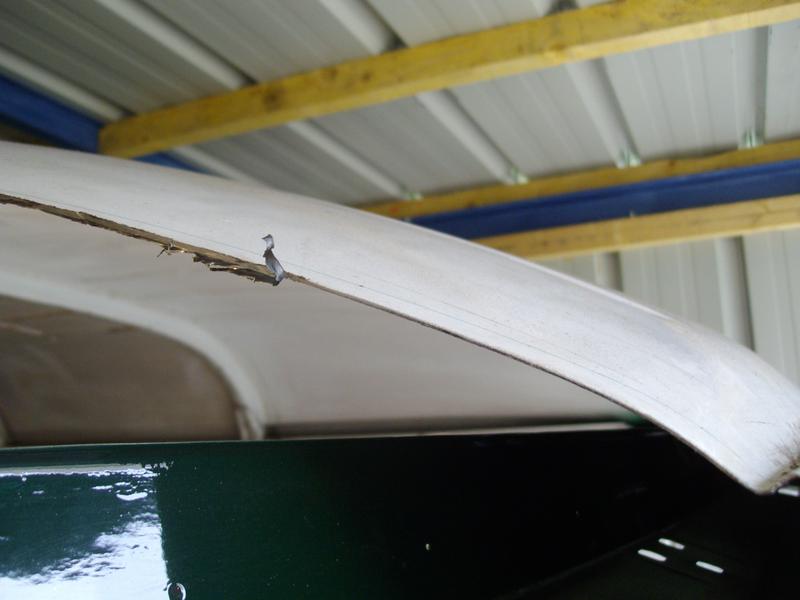
quand il faut gratter à coté avec le ciseau à bois, la coupure est la même qu'une lame de rasoir, sans douleur et sans effet sur le moment.
sauf qu'ici, la profondeur est relativement faible...avis au amateur (.trice) de suicide raté !
et gratter, il vas falloir... petite compensation quand même, reste pas grand chose des points de soudure de la gouttière
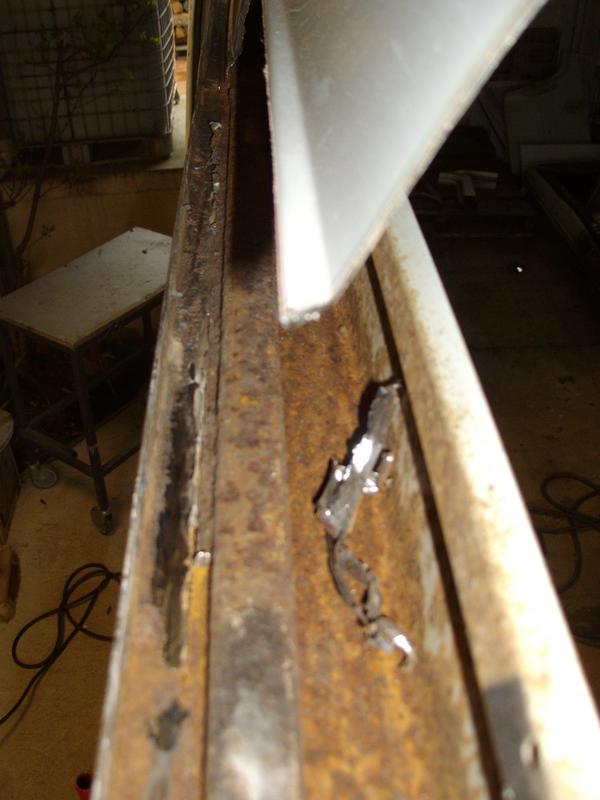
facile !

.
un peu moins sur le loupé lors de la découpe, qui laisse cette magnifique saignée dans la structure.
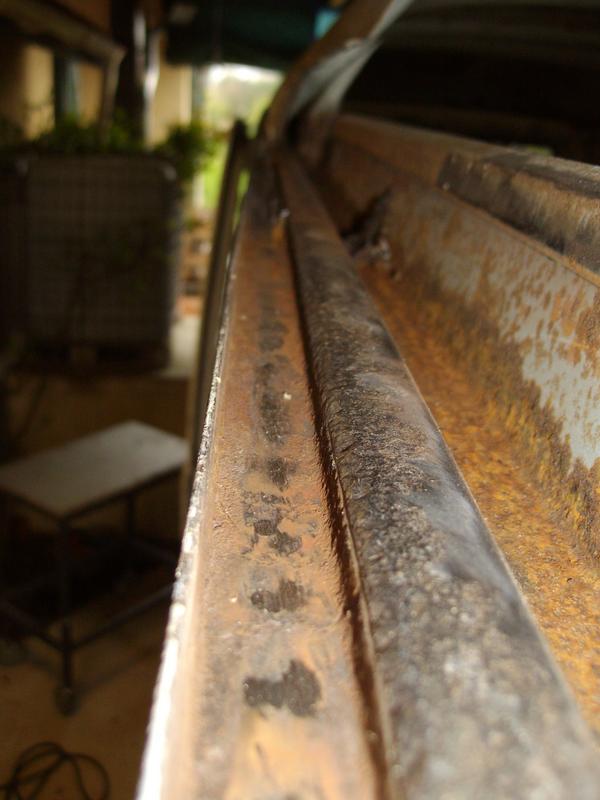
petit aperçu de l'embase du premier montant de toit...
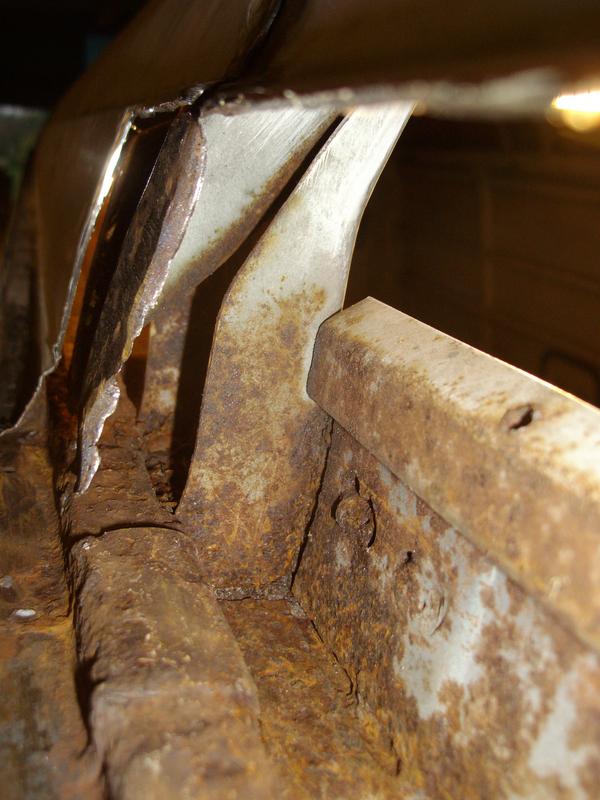
mais pas d’éparpillement, retour sur le montant de portière ou l'idée est de changer la feuillure extérieure. on découpe le morceau du montant découpé sur le 410
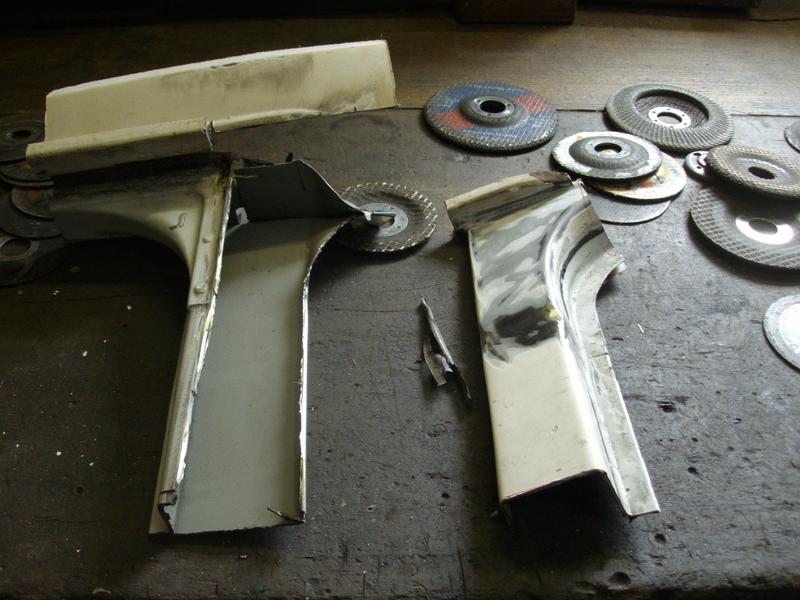
ce qui permet de confirmer la faille. le point sensible c'est la brasure entre la cornière et la feuillure.
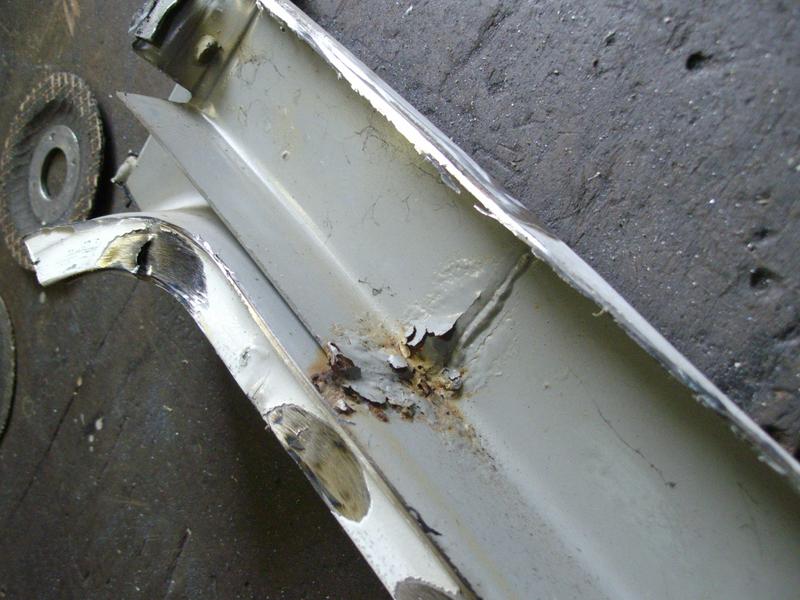
et ça commence a grignoter doucement mais sûrement entre les deux
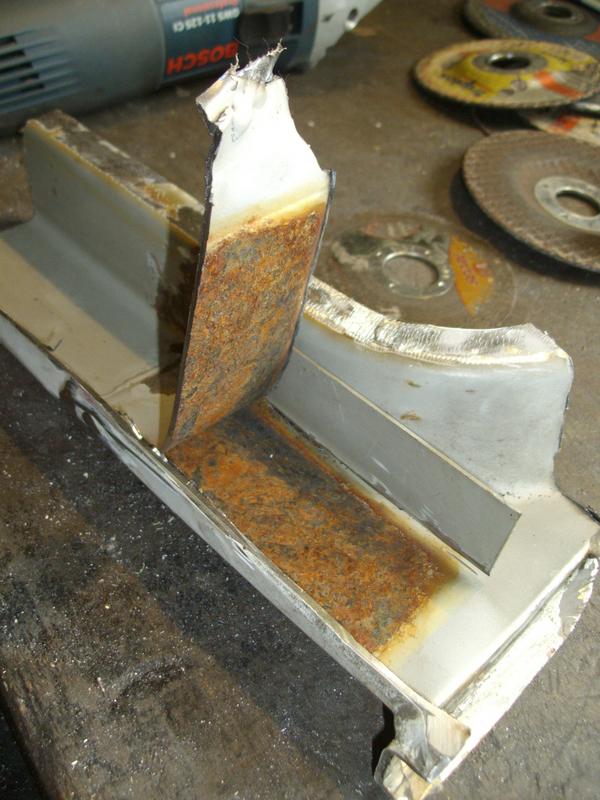
on reprend le principe de jeter ce qu'il faut garder sur le camion. ici c'est la cornière.
et on présente la pièce au camion pour repérer les traits de découpes à l'ajustement. et dans mon cas, je me suis bien chier !
la hauteur entre la courbure et la gouttière !
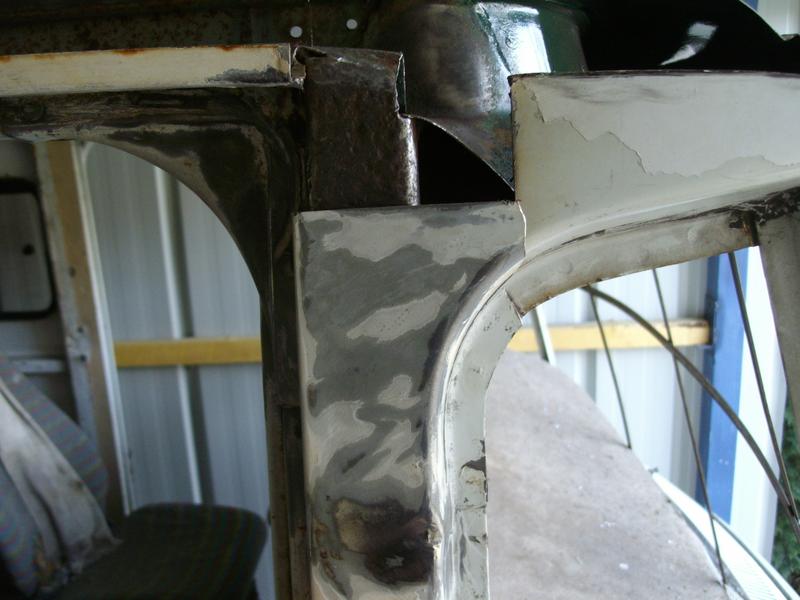
l'épaisseur du montant
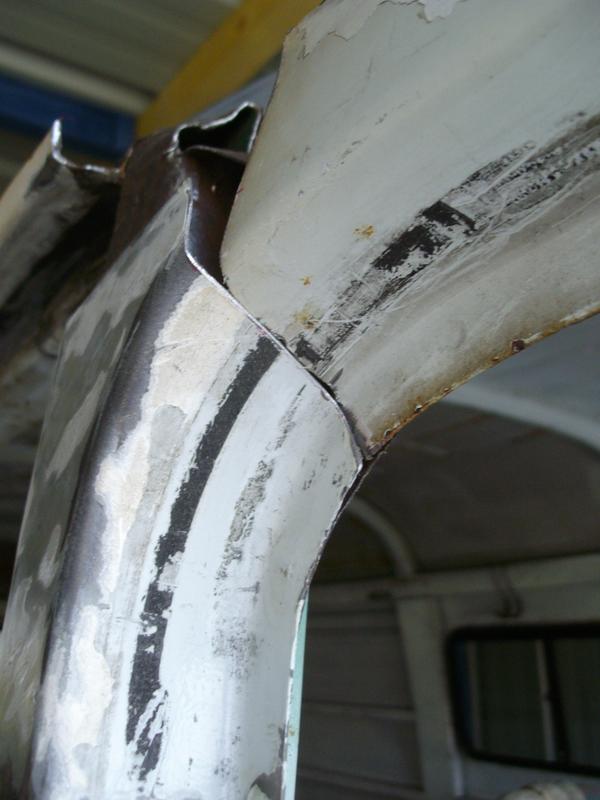
mais pas de panique, avec la soudure, ya pas de limites.
un petit régime pour le montant
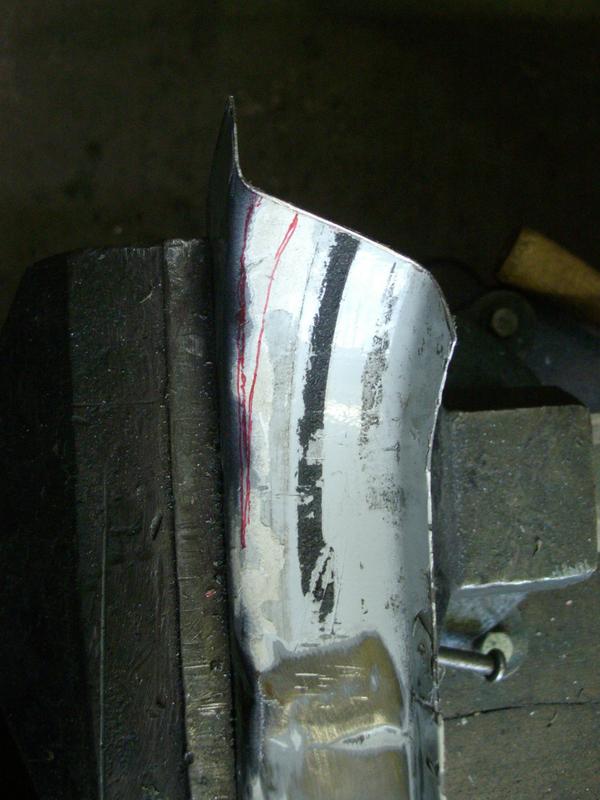
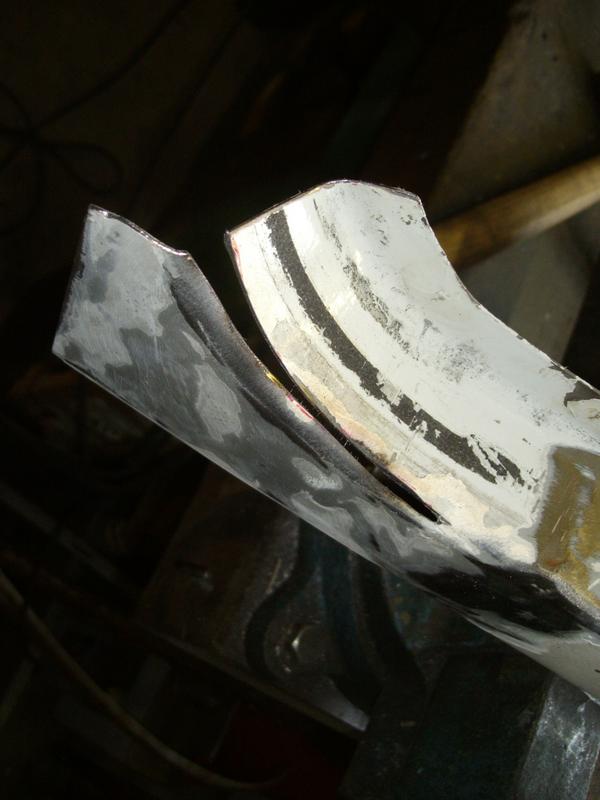
un premier pointage
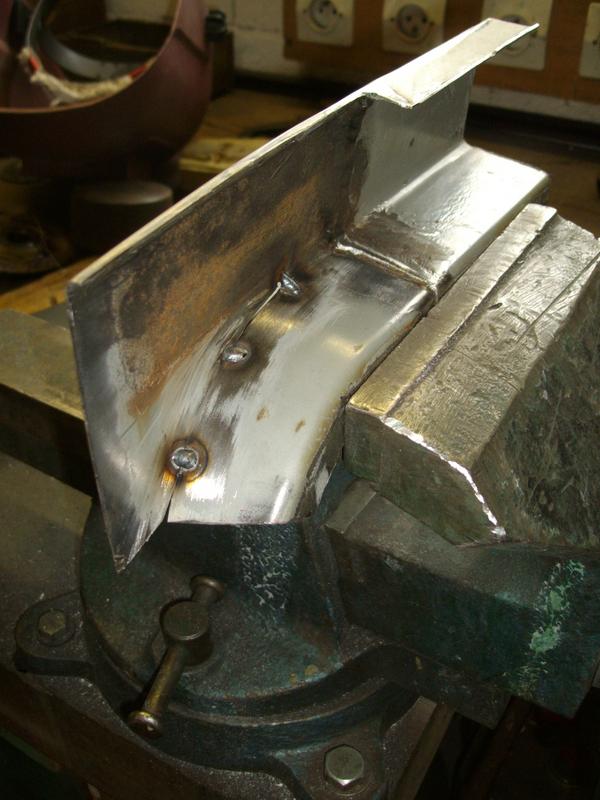
et au final, non, ça sent la galère d'insister dans cette direction, ça pue le rafistolage ! et en plus cela ne supprime en rien le défaut de conception chez merco ! ( lié a la production en grande série ).
cette cornière existe car c'est trop coûteux et compliqué d'emboutir l'arrondi du montant dans la même tôle que le montant lui même. l'épaisseur utilisé pour le montant est de 1mm, et passé la brasure, devient 7/10, plus facile a plier mais créé un point faible à un endroit déjà critique pour sa rigidité puisque c'est la jonction de différentes structures.
faut pas hésiter à sortir de cette logique.
donc changement de direction, fabrication de la pièce dans une taule de 1mm.
après un patron en carton
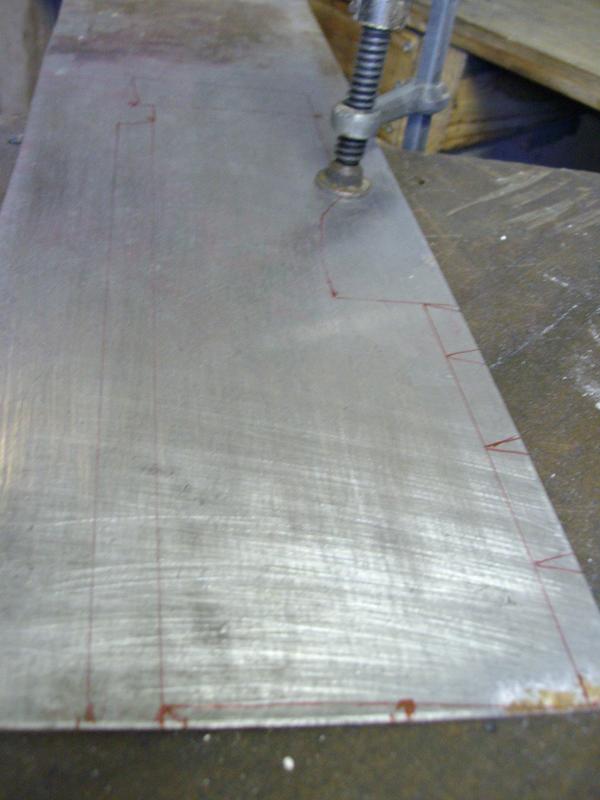
et comme je n'ai pas les compétences d'un chaudronnier, récupération de ce petit bout indispensable.
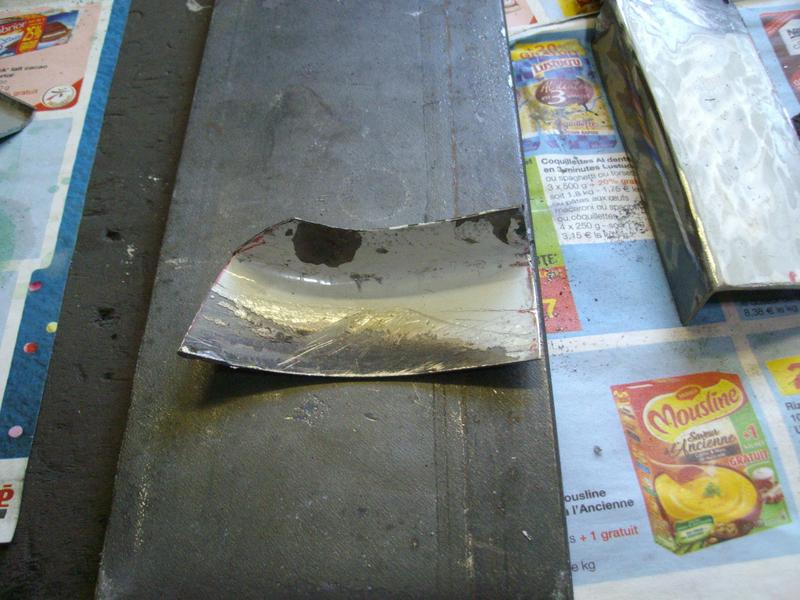
découpe de la cornière, sauf l'extrémité qui est soudée à la structure,
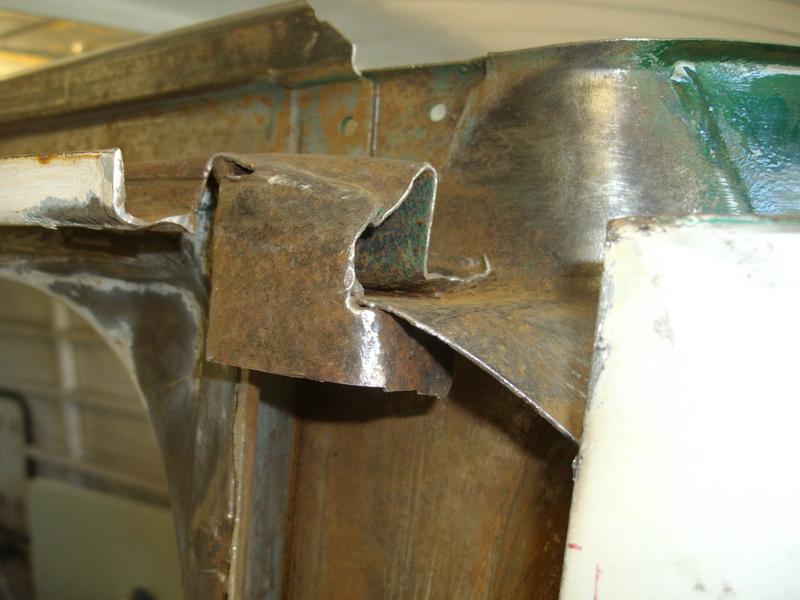
et on en profite pour découper plus bas que le niveau de la brasure pour faciliter le grattage du montant .
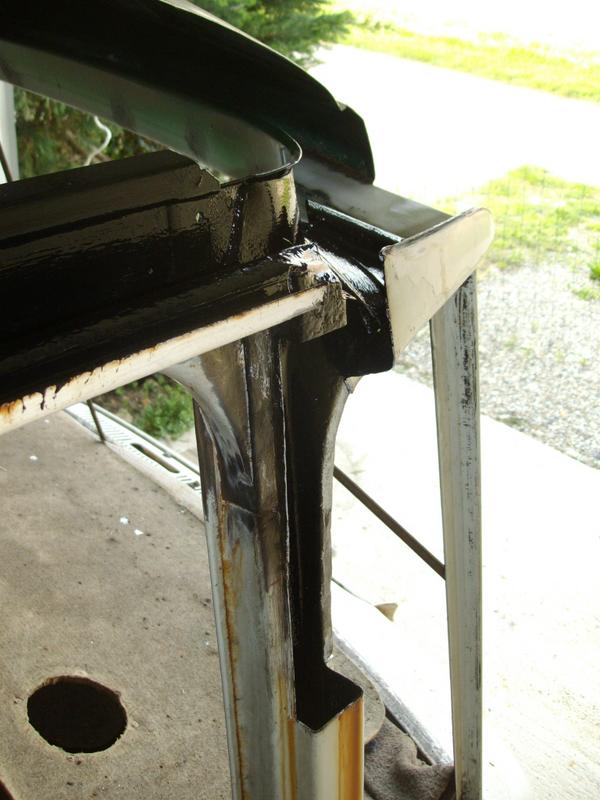
après un premier pliage, ajustement du petit bout
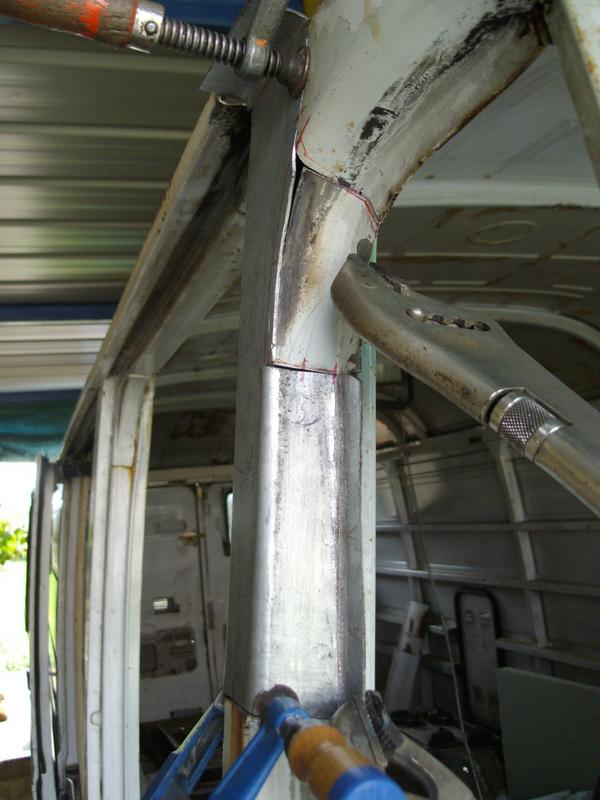
petit bout pointé
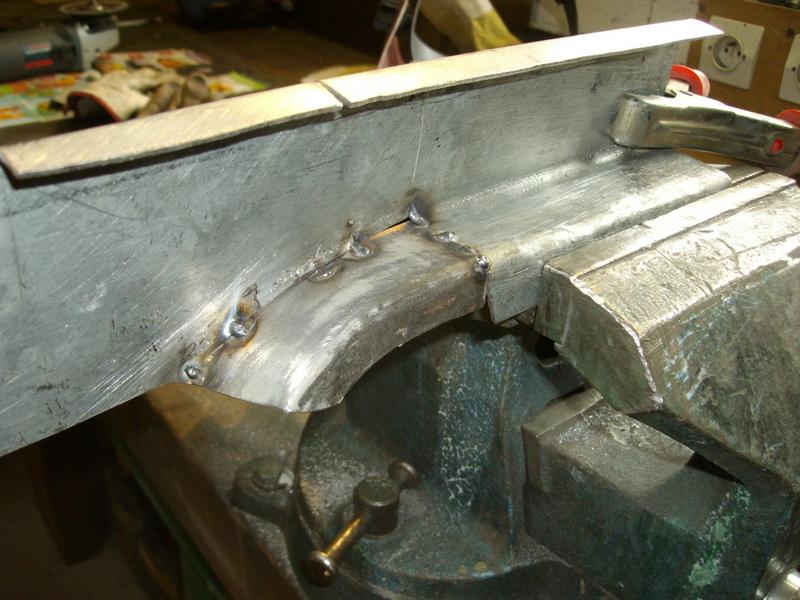
puis une soudure chargée
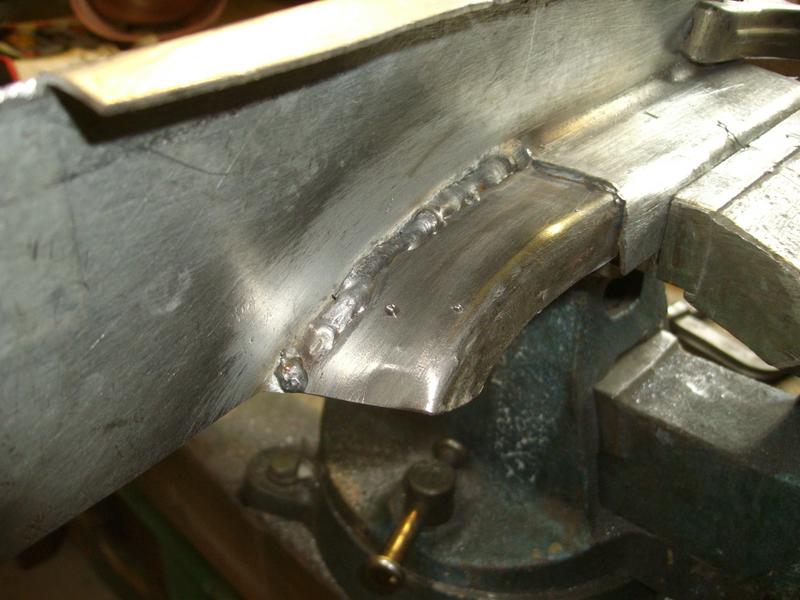
dans la perspective d'avoir un arrondi à faire.
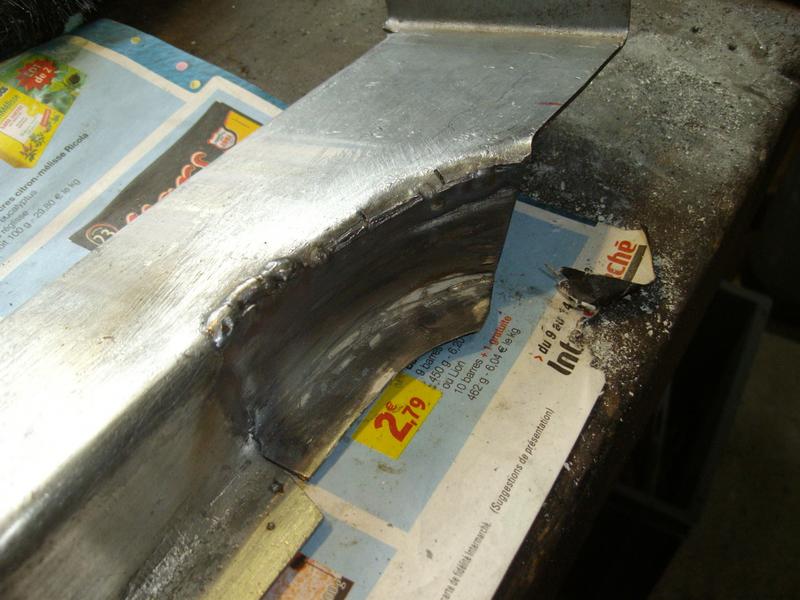
pour être positif, plus on en fait, plus ça devient facile. mais pour être sincère, ça reste bien prise de tête quand même ( ne pas tenter de faire la pièce sans commencer par le patron en carton ! ).
faut inventer des montage complexe à base de serre joints et de tas en métal.
style plier deux fois en sens contraire, comme pour la gouttière...
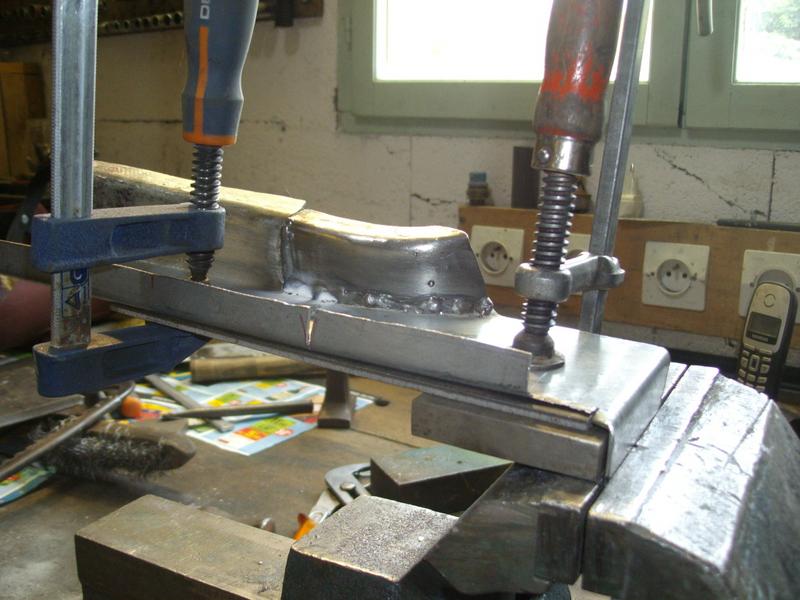
pffff, c'est galère !
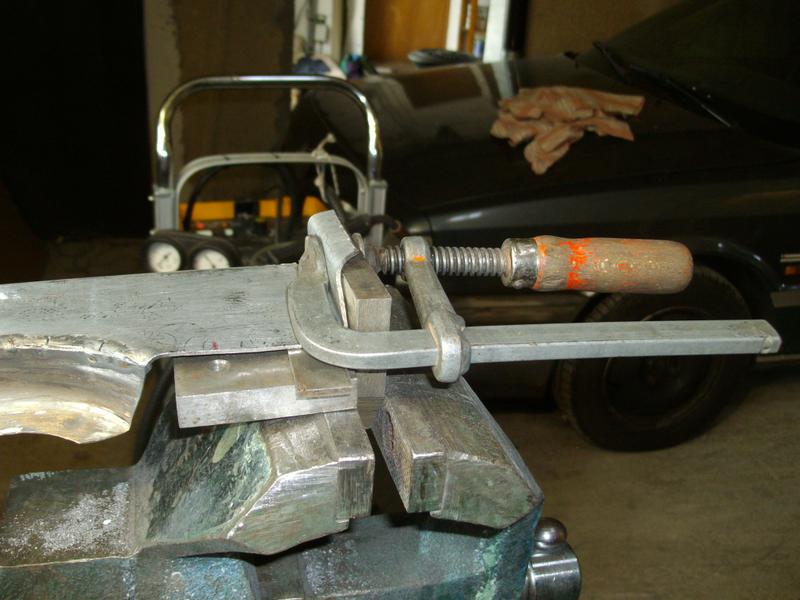
une petite entaille pour que la jonction soit plus facile
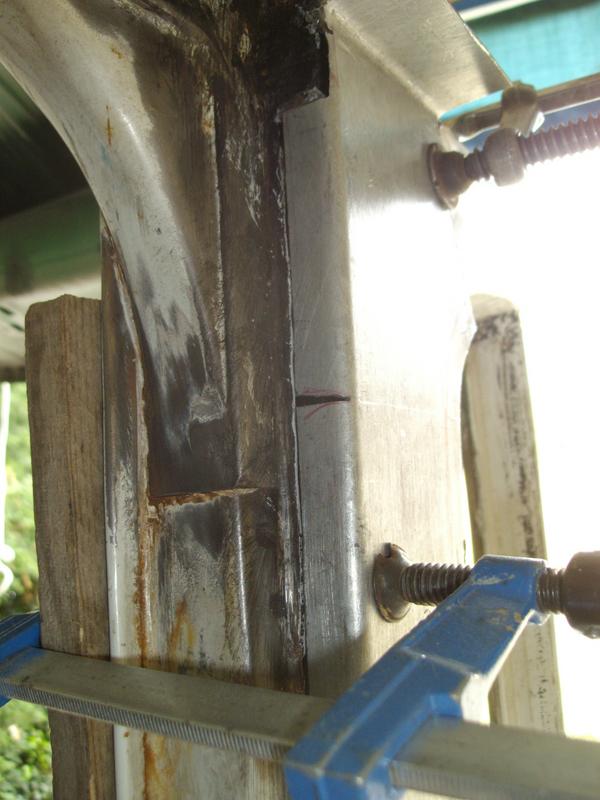
et enfin, quand on est sur que l'ajustement pour souder est bon, une protection impression phosphatant
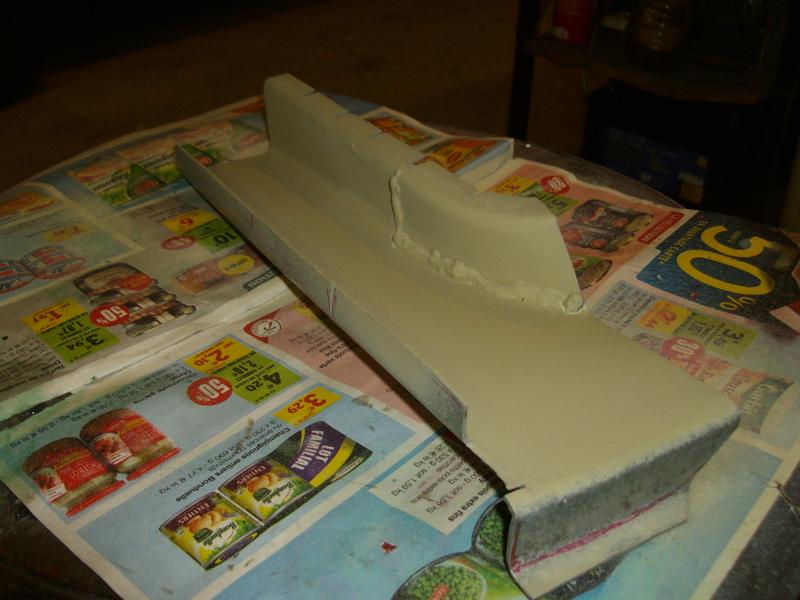
préparation du support. éliminer toutes traces de rouille qui présentent un "volume" ( paillette ).
finir en ponçant avec de la toile émeri de 40 ou 120. ne pas hésiter à soulever et gratter les parties sous lesquelles la rouille commence à gonfler.
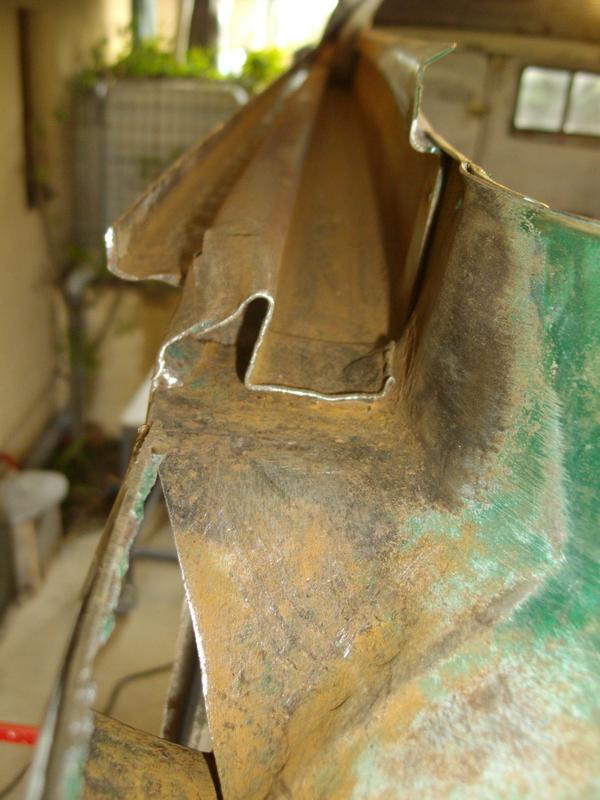
les outils qui ont servis pour faire tomber le rouille.. manque l'air comprimé et sa précieuse soufflette !
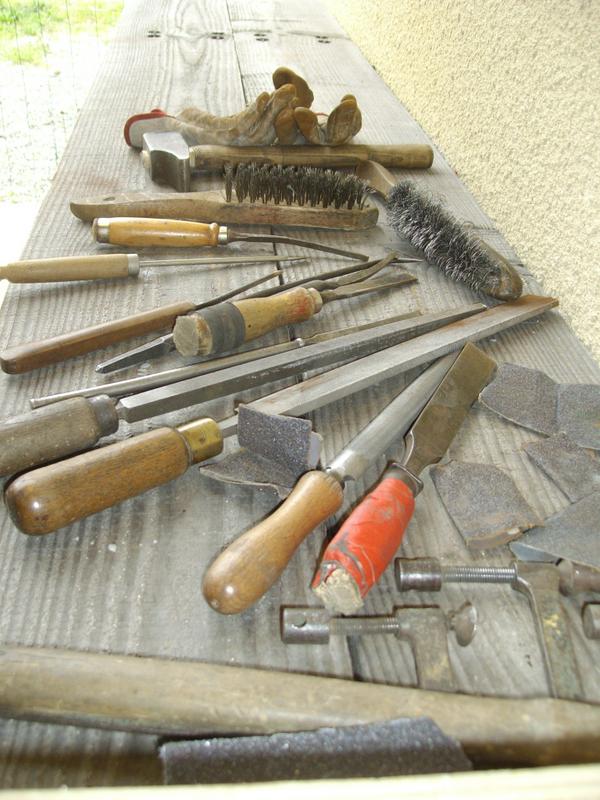
un passage au pinceau avec du frameto

idem pour l'intérieur du montant, enfin presque. jusqu'à la rencontre du support de la charnière supérieure.
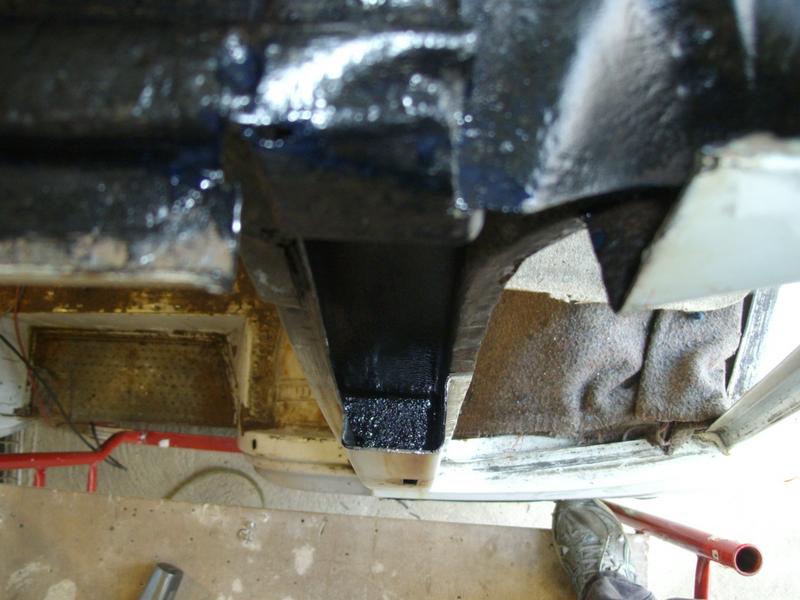
puis après respect du temps de séchage, tout dépolir avec du scotch brite
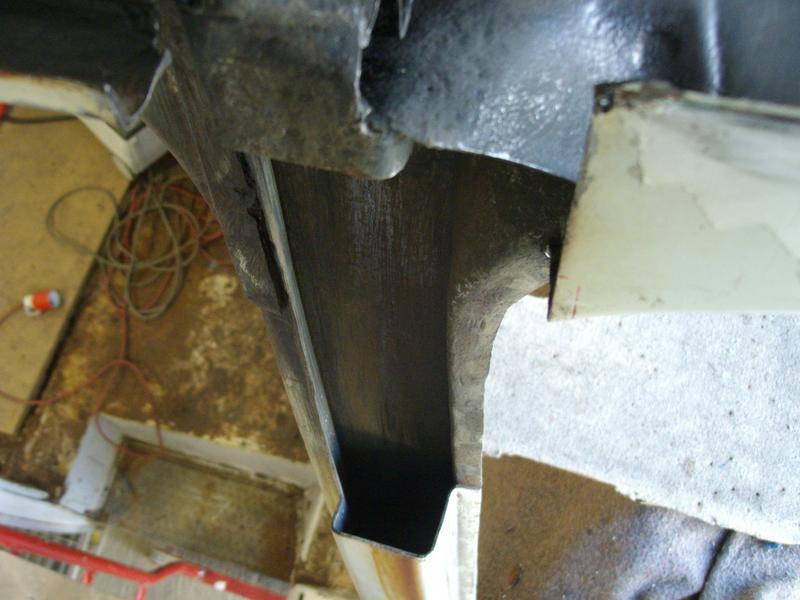
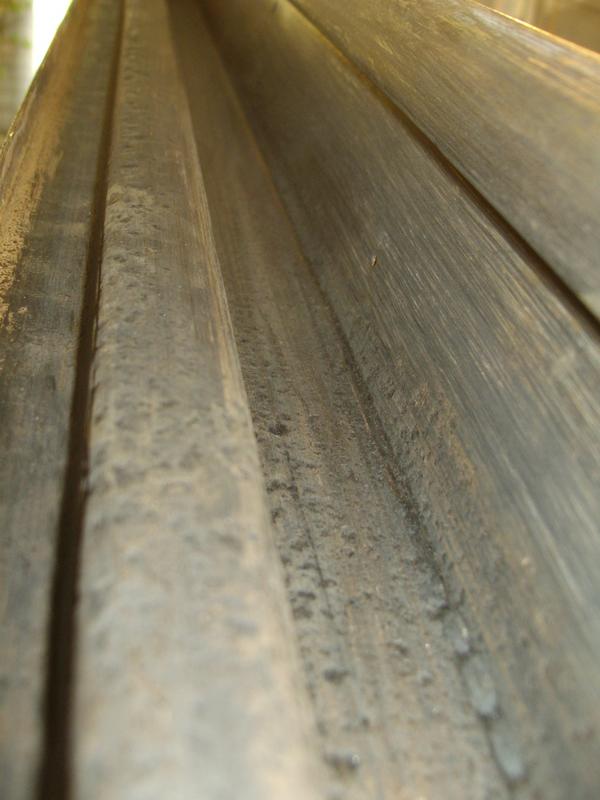
pour cette partie, j'utilise de l'anti rouille classique passé au pinceau.
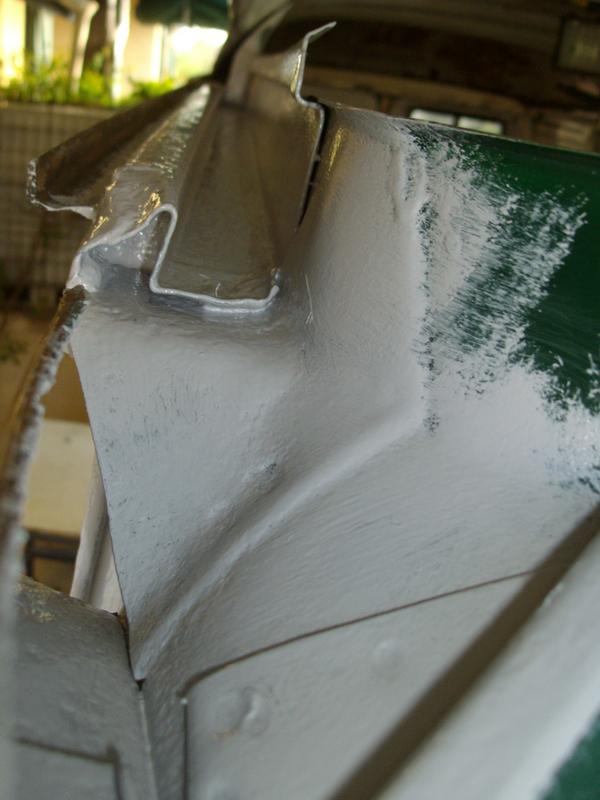
suivi d'une peinture de portail classique. pas très bon comme choix car elle résiste beaucoup moins à la chaleur du MIG que l'impression phosphatant, et le séchage est bien trop long !, mais le pinceau permet d'aller la ou le pistolet ne peut pas pulvériser...
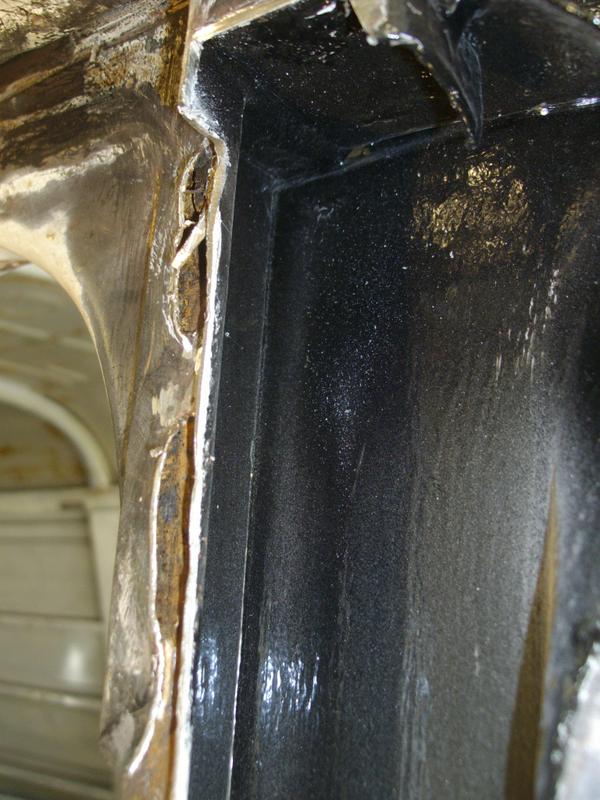
on profite toujours de l’accessibilité pour aller gratter sous les jonctions.
les surfaces a souder ont été poncé, on peut positionner la pièces
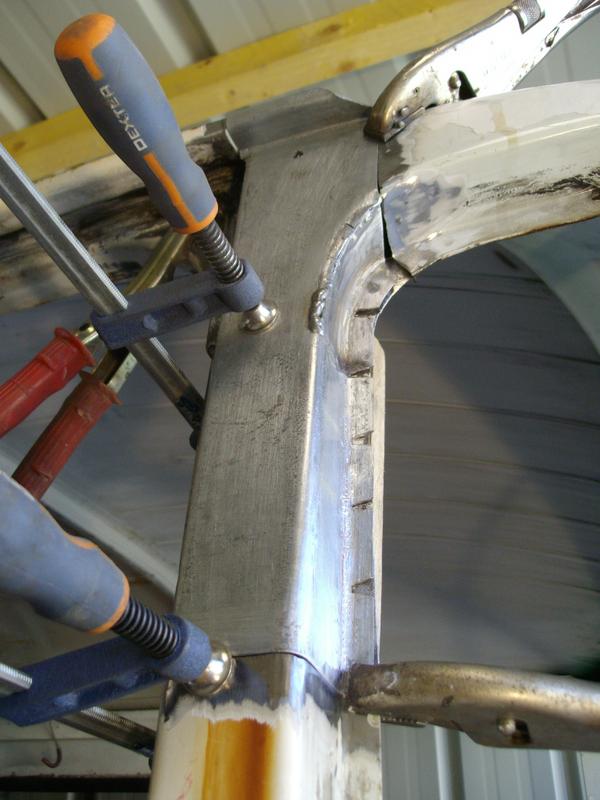
pour la pointer
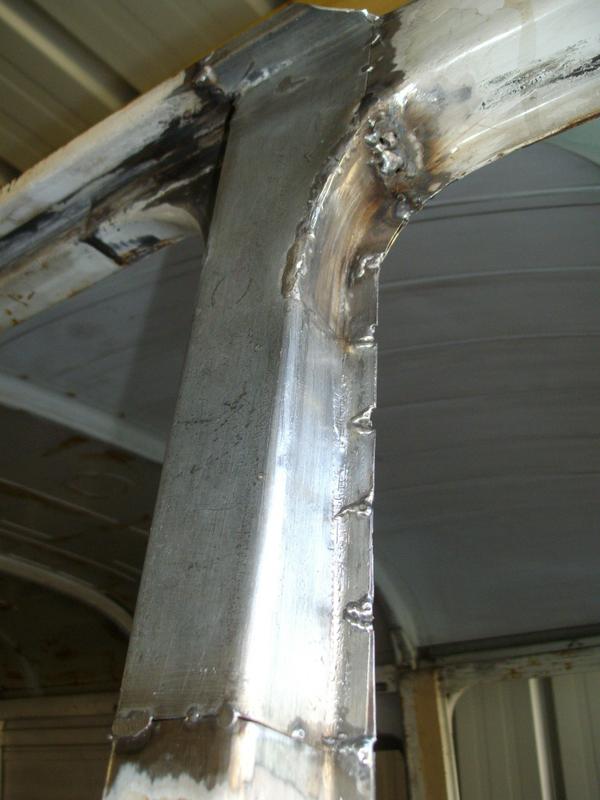
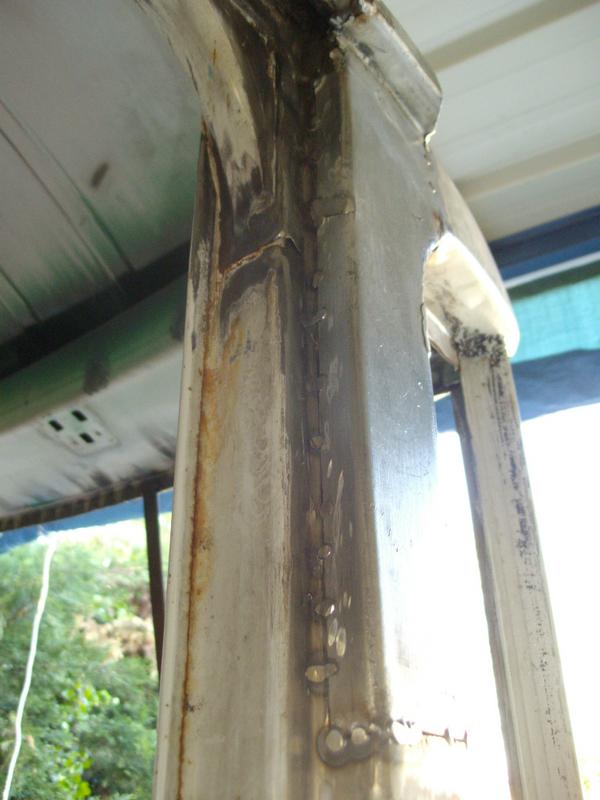
et la souder avec un cordon ( aie aie ! la peinture derrière ! ).
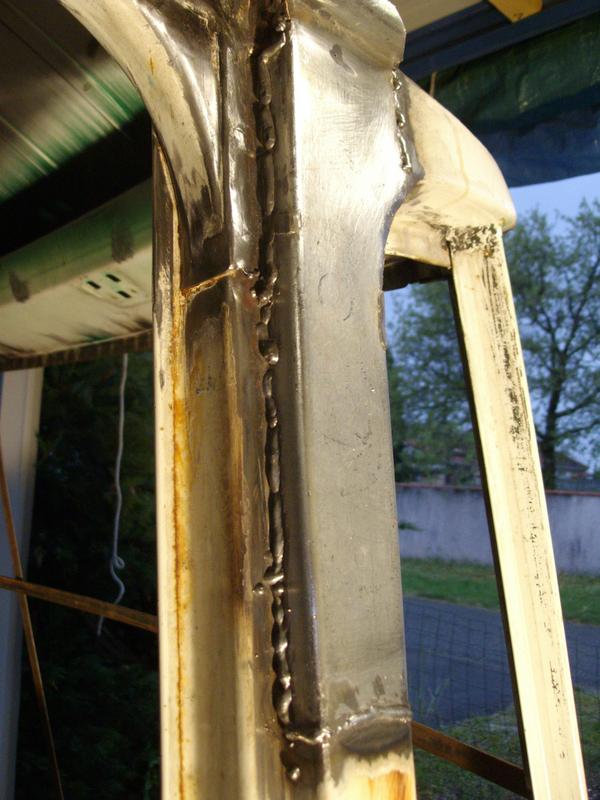
mais la zone doit être solide.
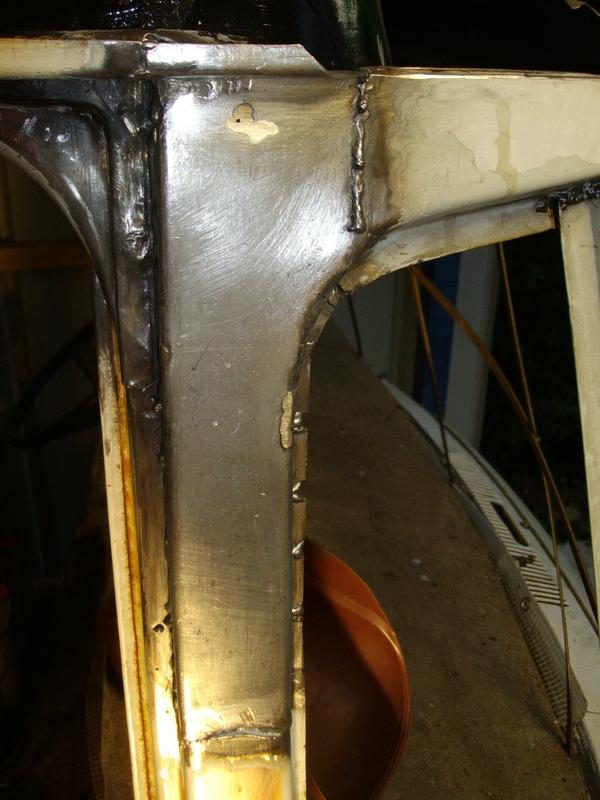
le passage de la disqueuse
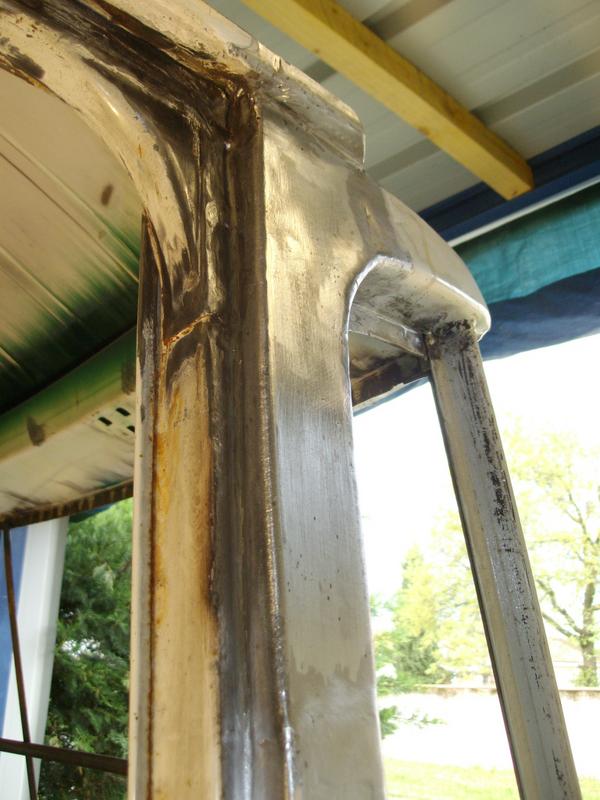
et celui de l'étain pour rattraper un alignement pas top... même à l'envers, en portant la chaleur avec des petits coups de flamme, l'étain peut se travailler comme une patte.
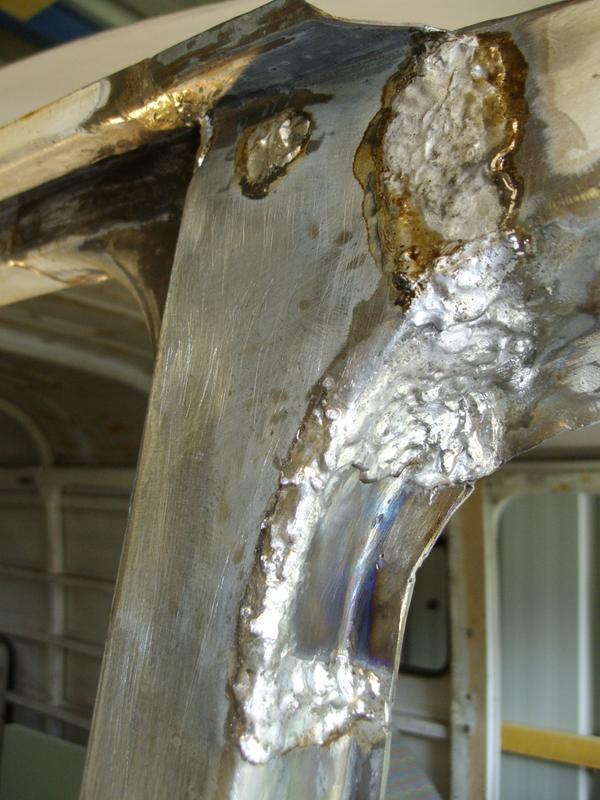
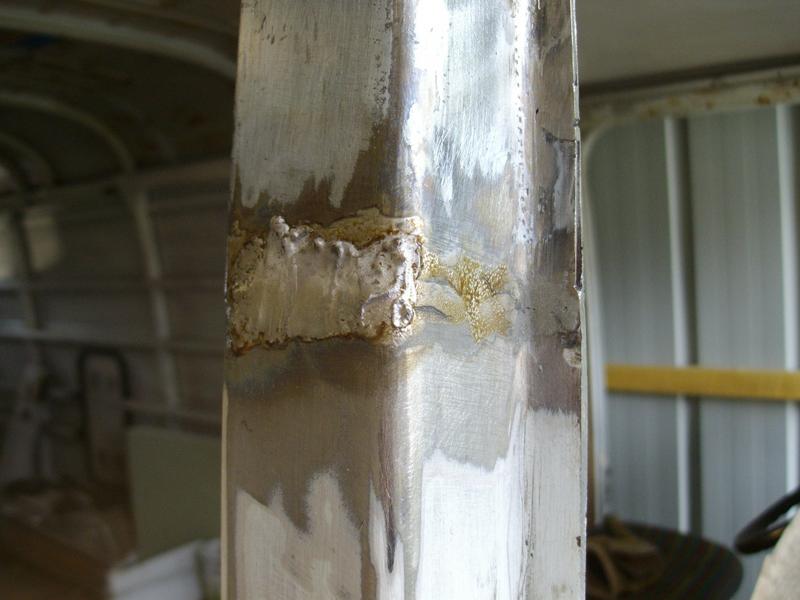
après avoir nettoyé l'acide, on dégrossit avec le disque à lamelles
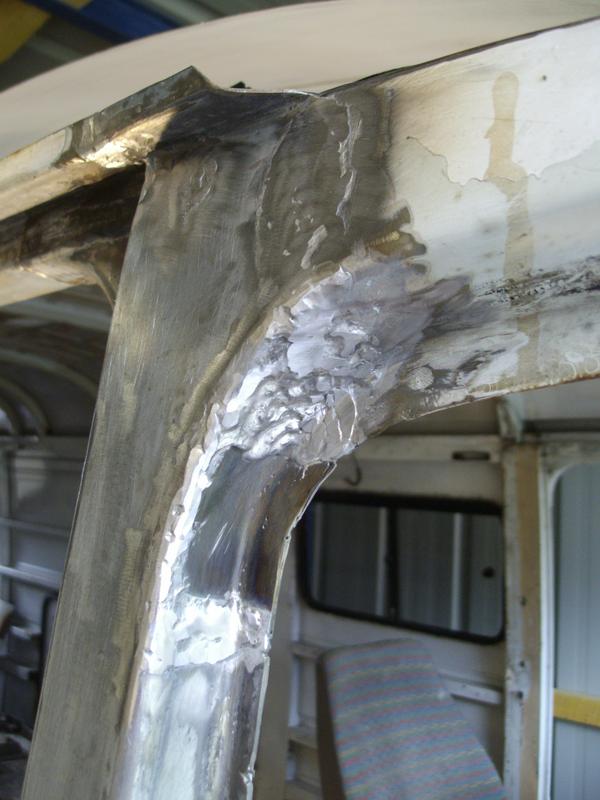
le final se fait avec un bout de toile émeri gros grain, monté sur cale et à la lime aussi.
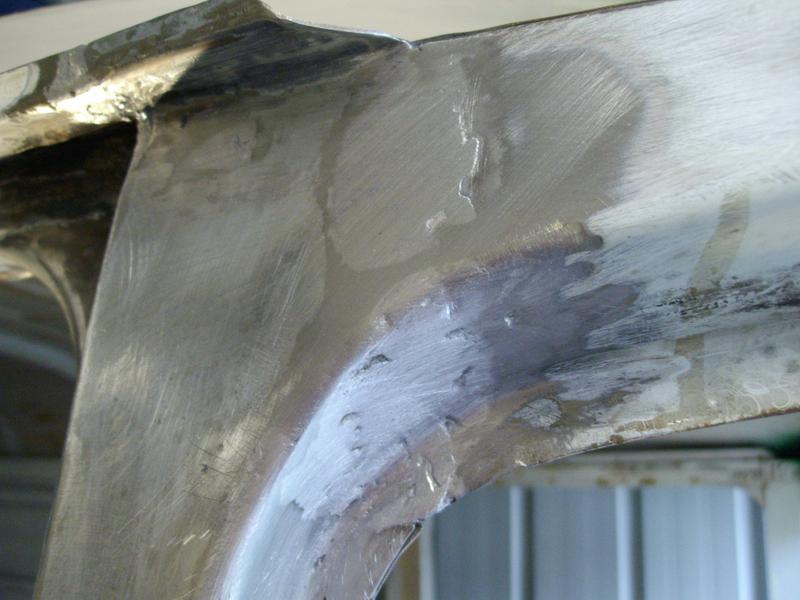
la cale a poncer fait apparaître les zones qui n'ont pas été touché par la toile émeri... ce sera une petite finition pour le mastic de carrossier.
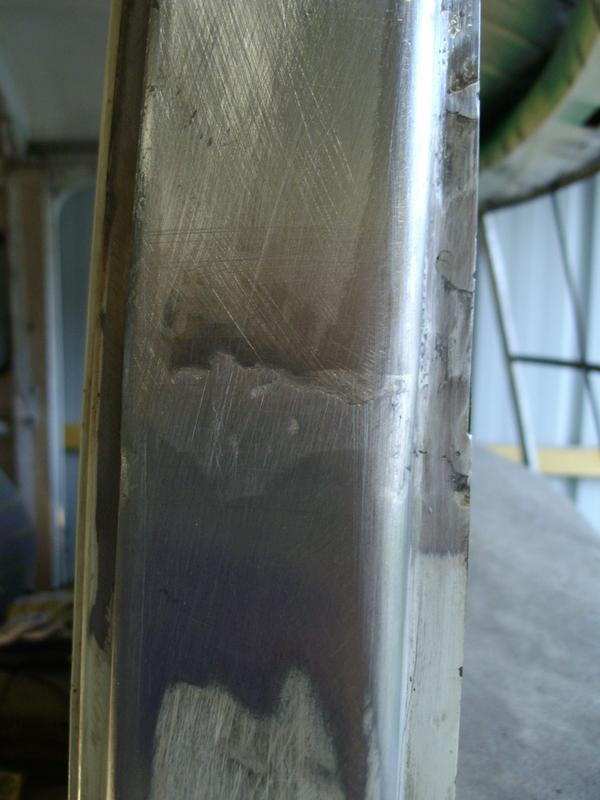
reste ensuite, par la seule ouverture restante, a pulvériser ( avec un flexible/buse multi directions ) sur les soudures et l' ensemble de l'intérieur du montant, une cire corps creux.
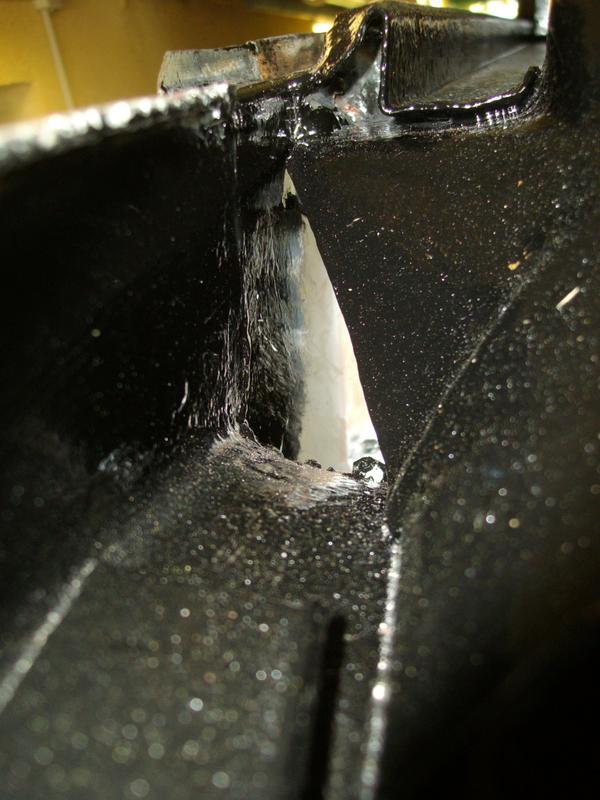
un embout de bombe dégrippant sur une bombe cire corps creux est bien pratique aussi.
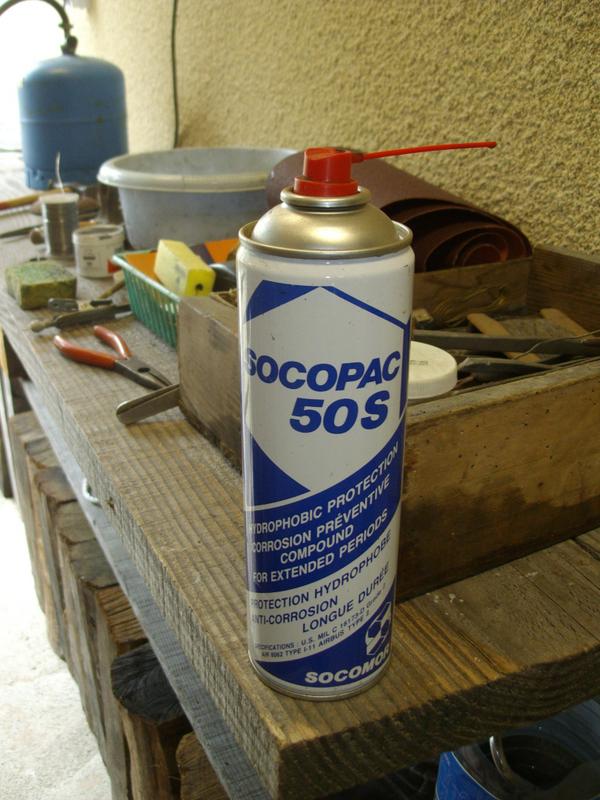
quand tout cela est fait, on peut fermer l'ouverture du toit.
marquer la découpe sur l'avant
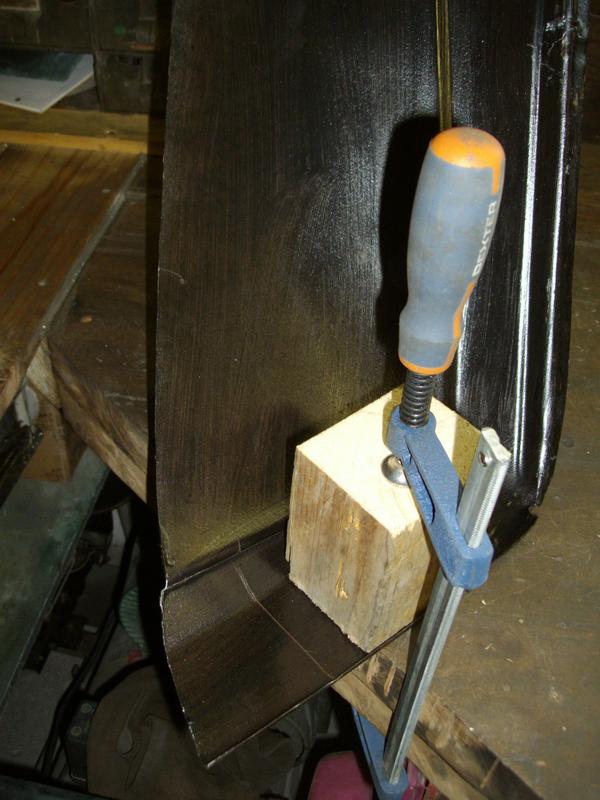
et couper pour pouvoir l' ajuster au toit .
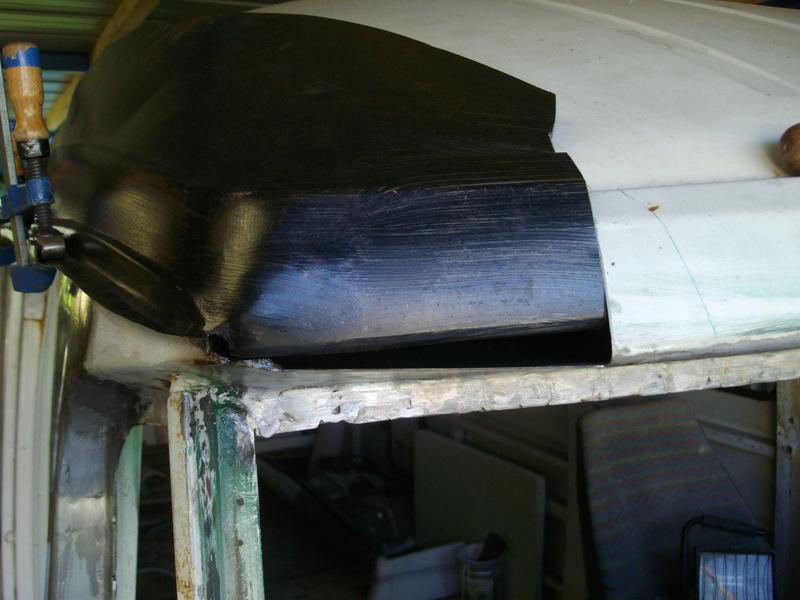
ensuite marquer la découpe et couper l'arrière.
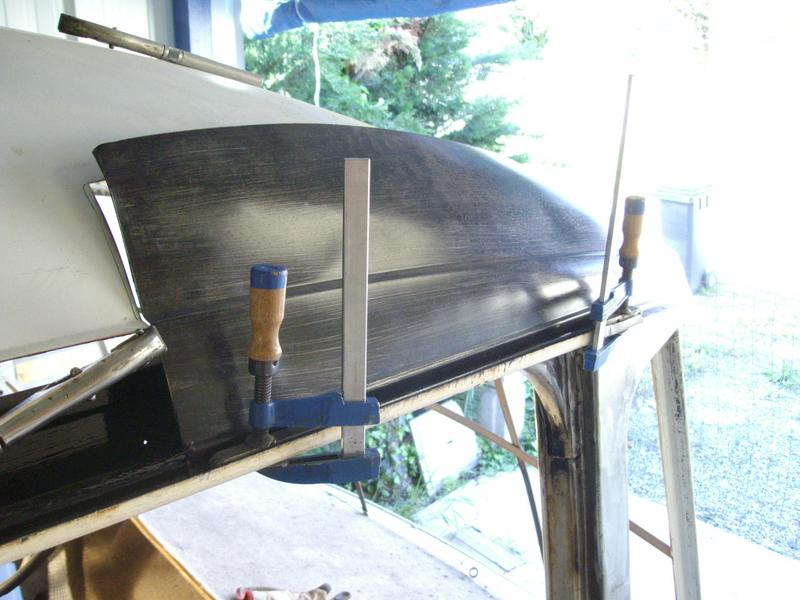
c'est alors possible de marquer précisément la découpe qui fera l'arrondi du toit.
il faut que la gouttière soit positionnée par des serre joint et que l'alignement de l'arrière et l'avant soit respecté.
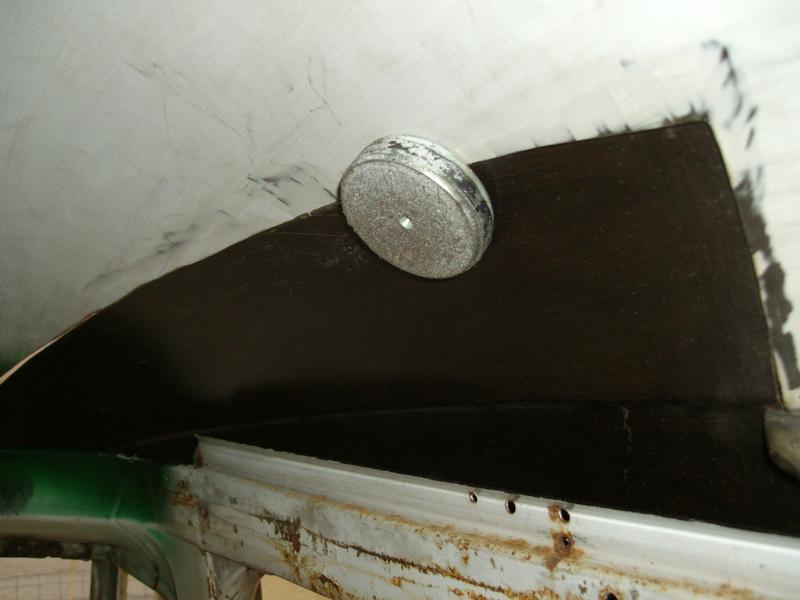
quand c'est bien ajusté, repérer la position de la pièce avant de la déposer pour préparer les surfaces à souder, et disquer les V pour souder la goutière.
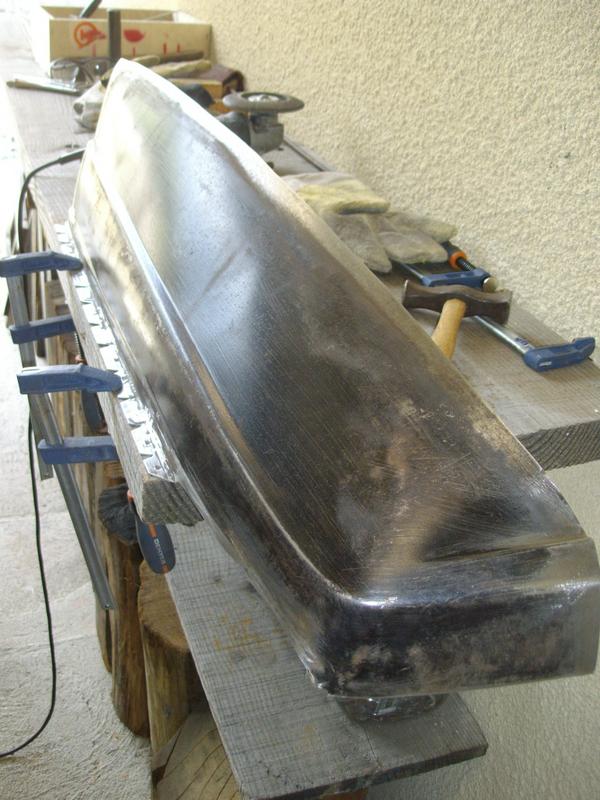
mettre à blanc coté toit aussi
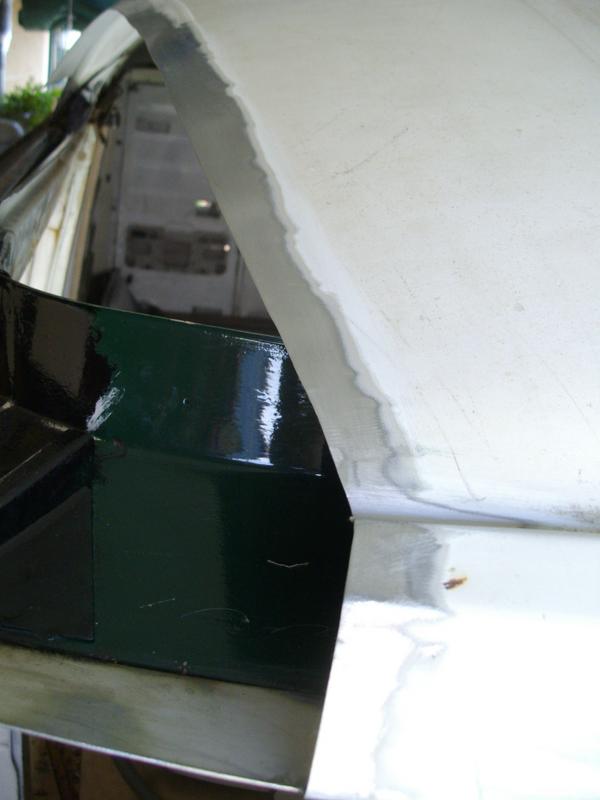
moment du résultat de tout cela...
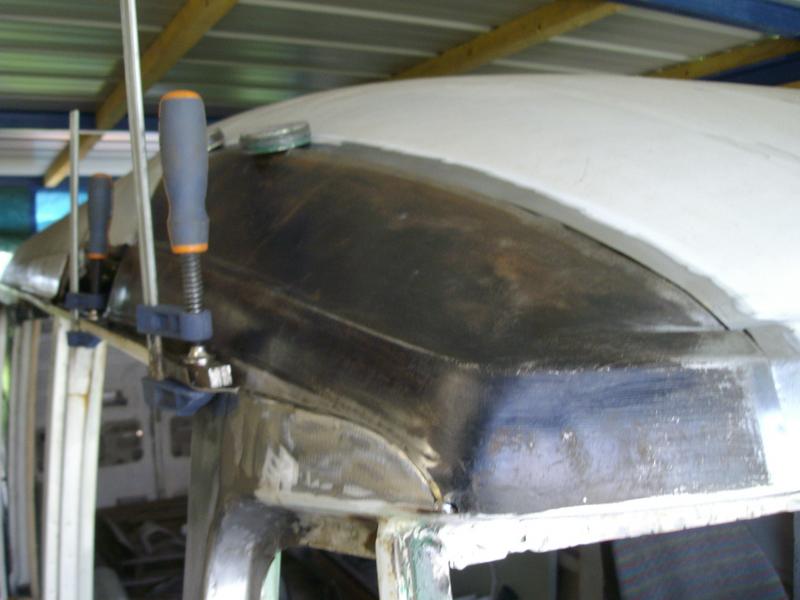
... bin entre le bigne qui a tout fait plonger le coin avant, et l'incendie qui a fait gonfler la pièce, le pointage vas demander de la patience !
les serres joints sont enlevés pour faciliter le positionnement du haut
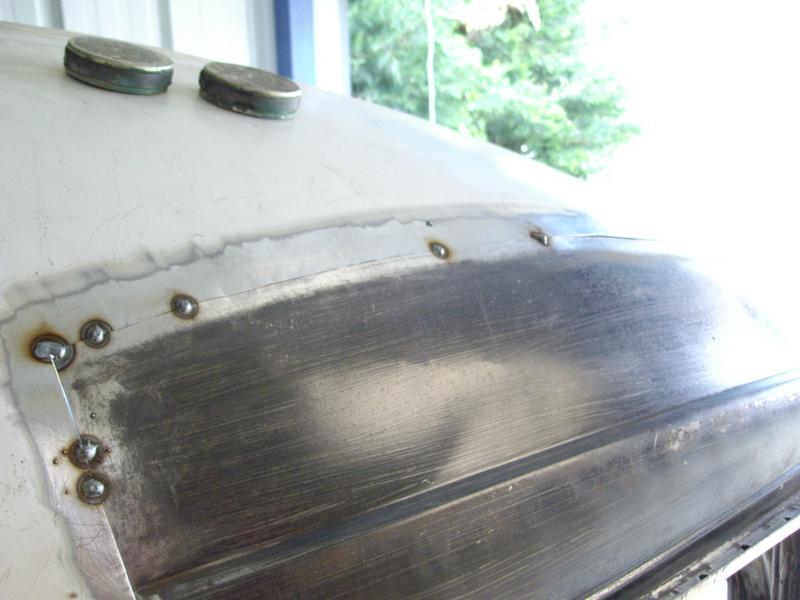
en prenant son temps, le résultat fini par se voir
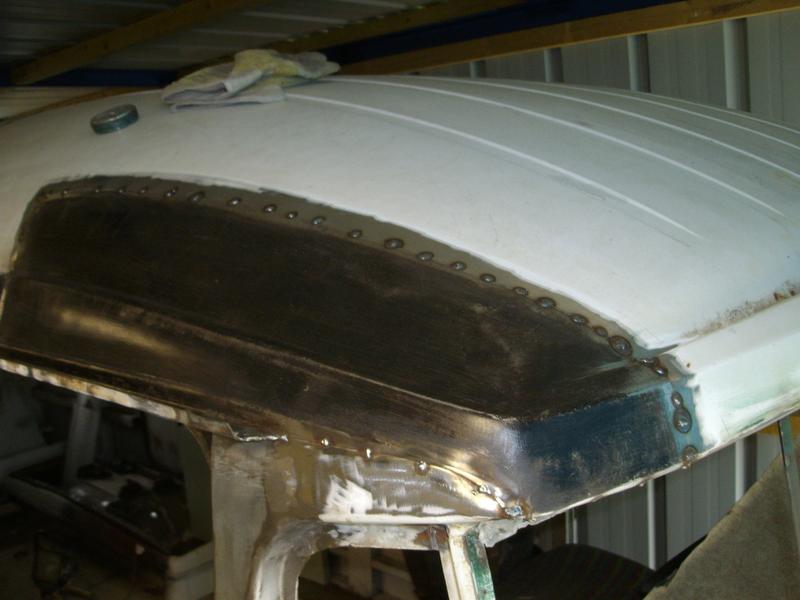
souder les V sur la gouttière et les disquer.
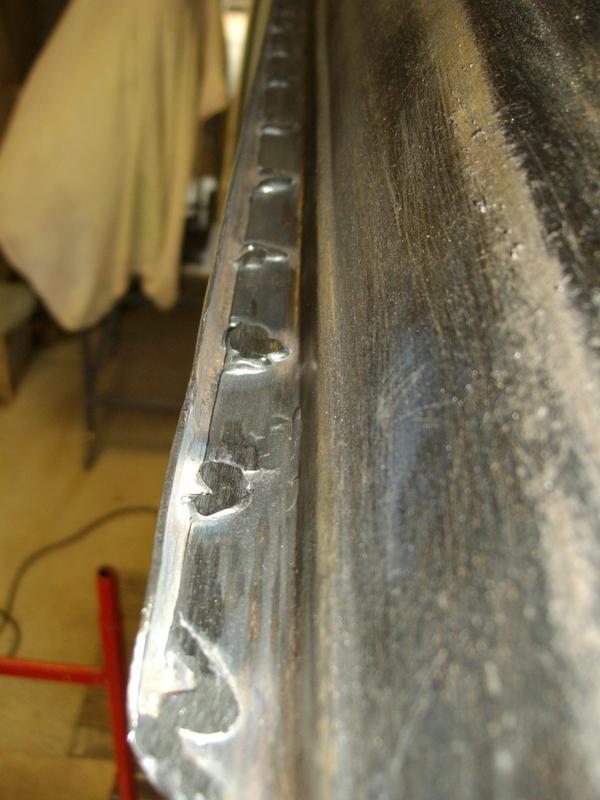
pour info, il existe des disques à meuler (a droite ) pour dégrossir, la finition se fait avec celui à tronçonner (a gauche ), avec un grain plus fin.
le changement de disque sur la disqueuse ne fait pas perdre du temps... mais bien le contraire !
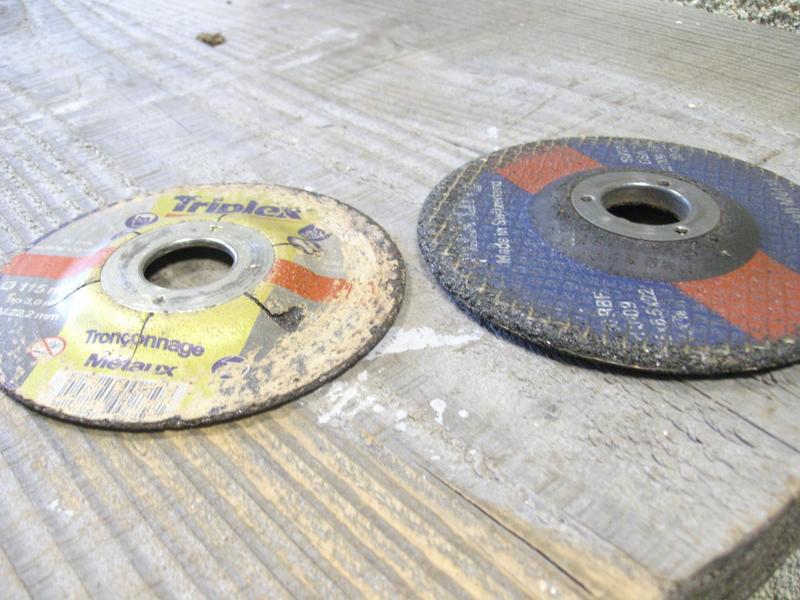
j'ai un peu oublié de le mettre à coté, mais le disque pour couper la carrosserie est moins épais que celui de gauche (1mm).
m' fin, j'étais content à l'idée de pouvoir faire un joli joint d'étain dans cet endroit si facile !
donc préparation des surfaces a étamer, avec entre autre le joli affleurement de la disqueuse sur la gouttière, tout le long de l’arrête de la pièce.
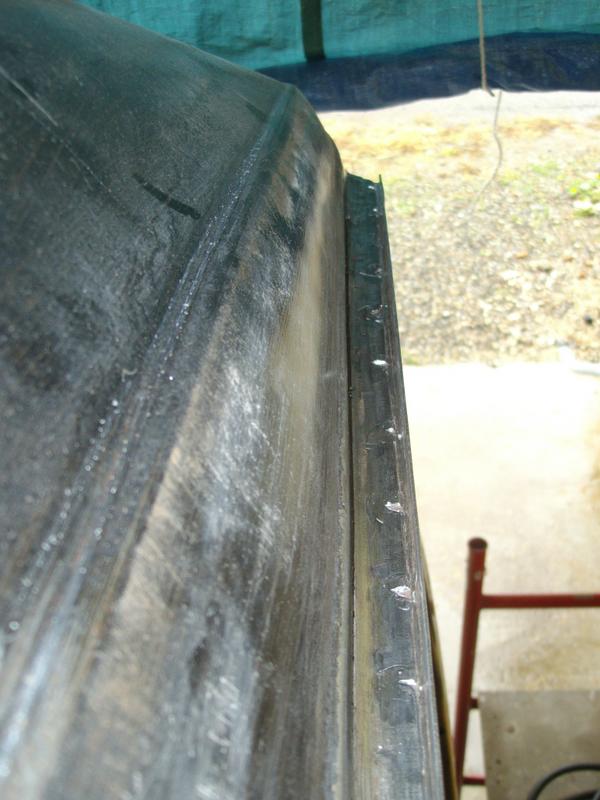
patte a étamer
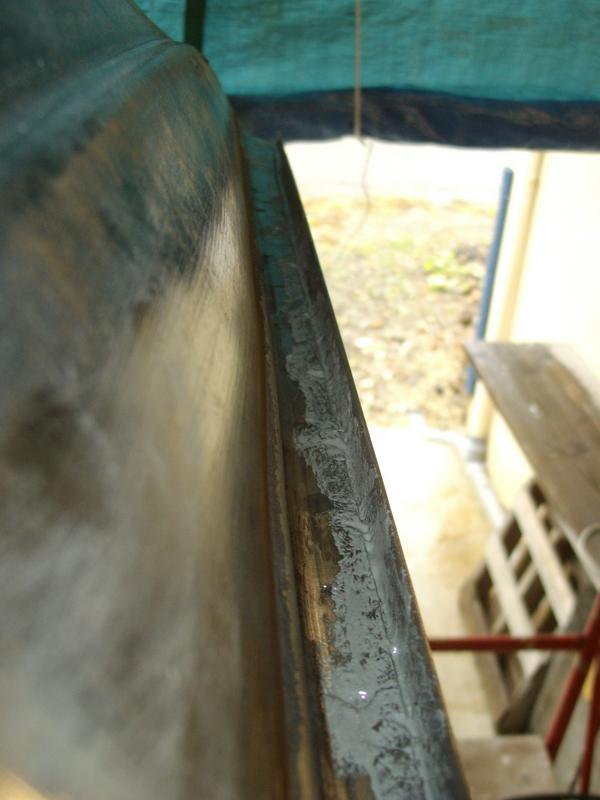
chauffer par le dessous de la gouttière après avoir décapé la peinture.
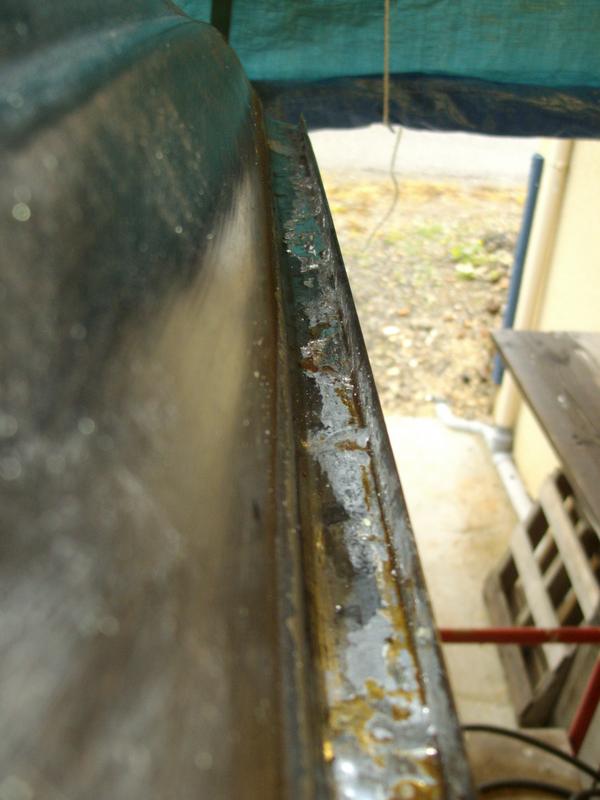
et la, facile de faire un joli cordon qui viendrait faire la jonction entre l’arrête de la pièce et le bord de la gouttière !
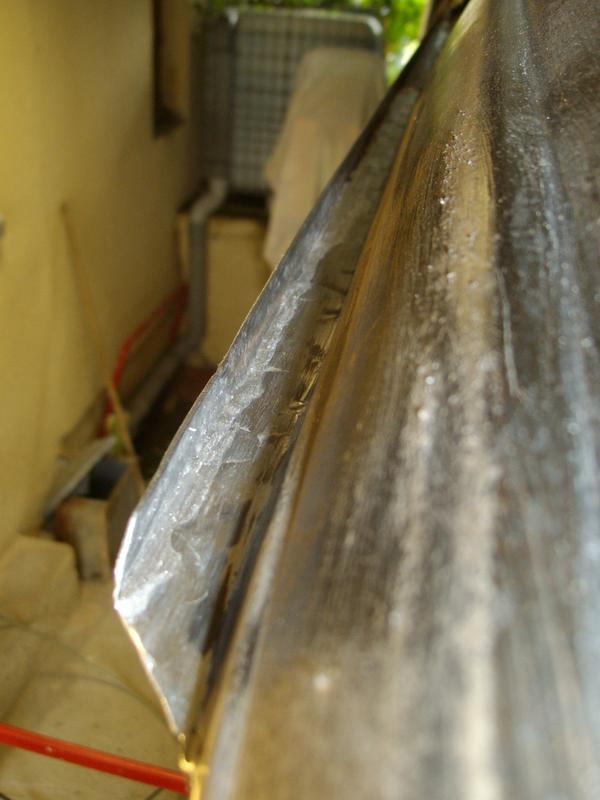
moais, trop oxydé, pas assez décapé. le compromis n' a pas été le bon partout !
et l'étain n'a pas accroché à tous les endroits du bord, mais c'est quand même étanche.
un coup de cire corps creux coté intérieur avant que la chaleur tiède ne parte, et la cire se répand mieux.
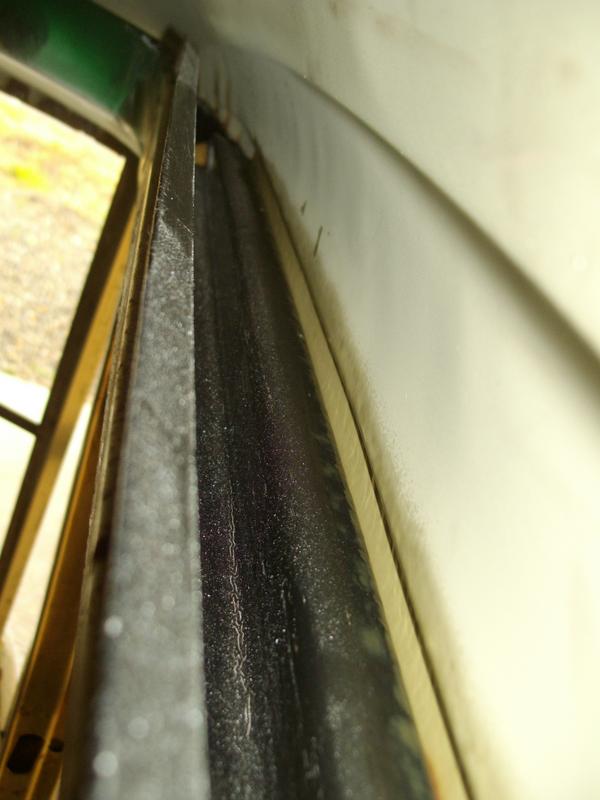
finir de souder
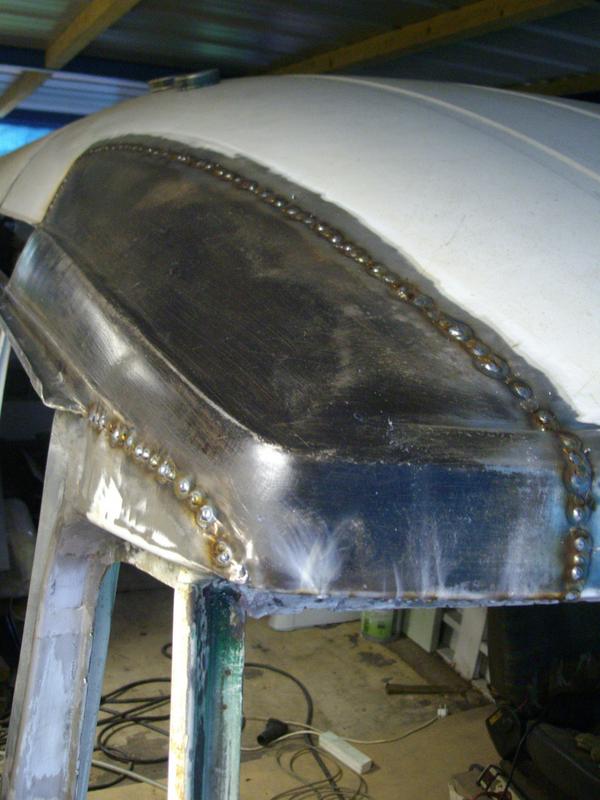
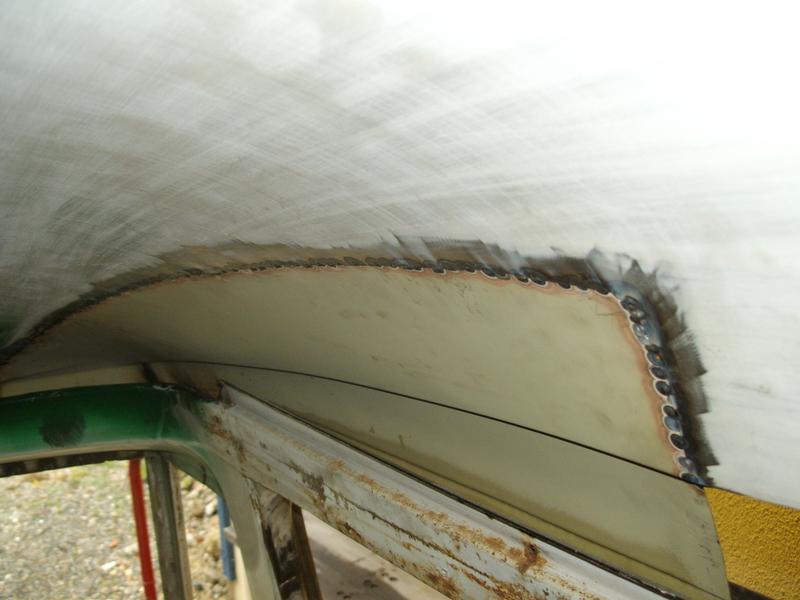
disquer
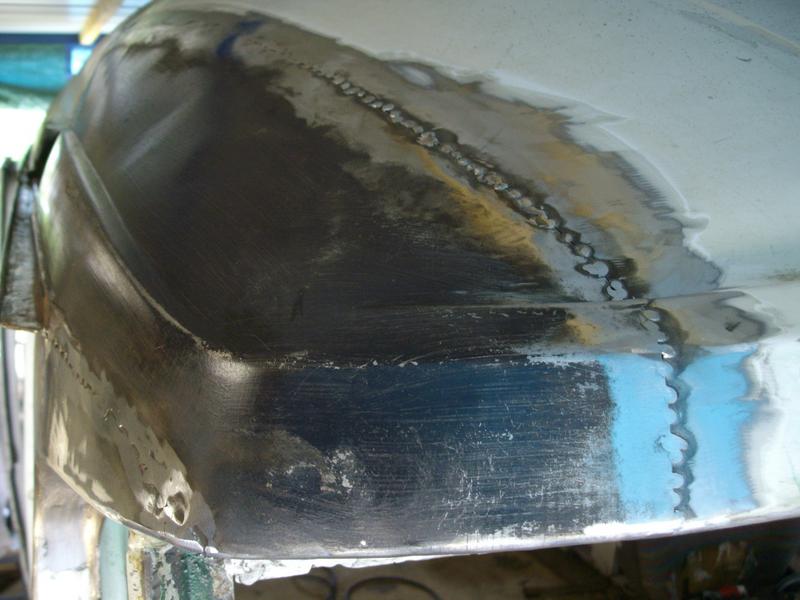
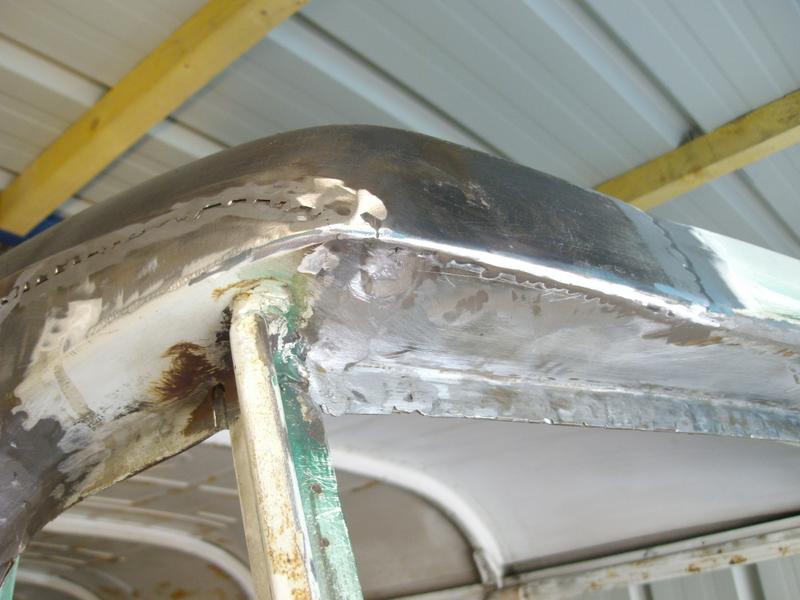
le taf de l'étain entre en jeux, et à cet endroit il vas falloir prévoir large !
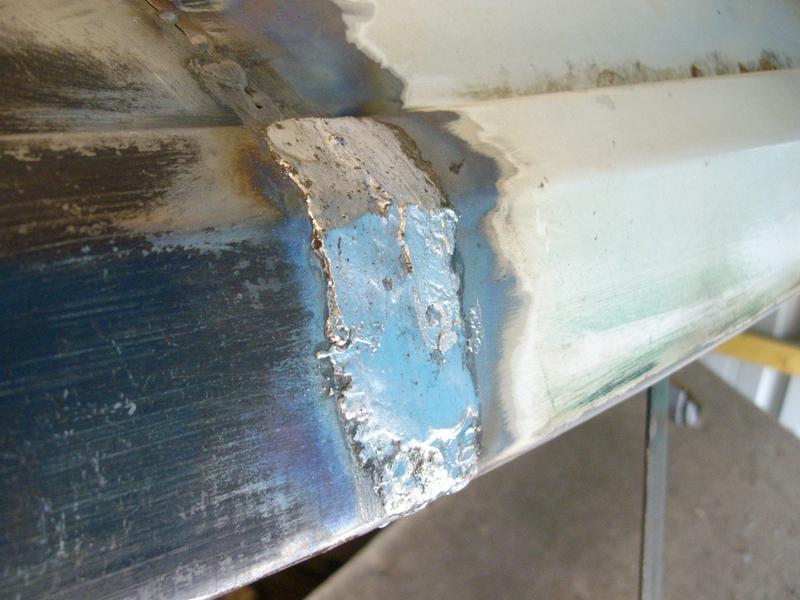
avec un peu de pratique au niveau de la recherche de température, on arrive a l'aplanir avec une lame chauffée ( comme une pane de fer à souder ), ou une spatule en bois très dense.
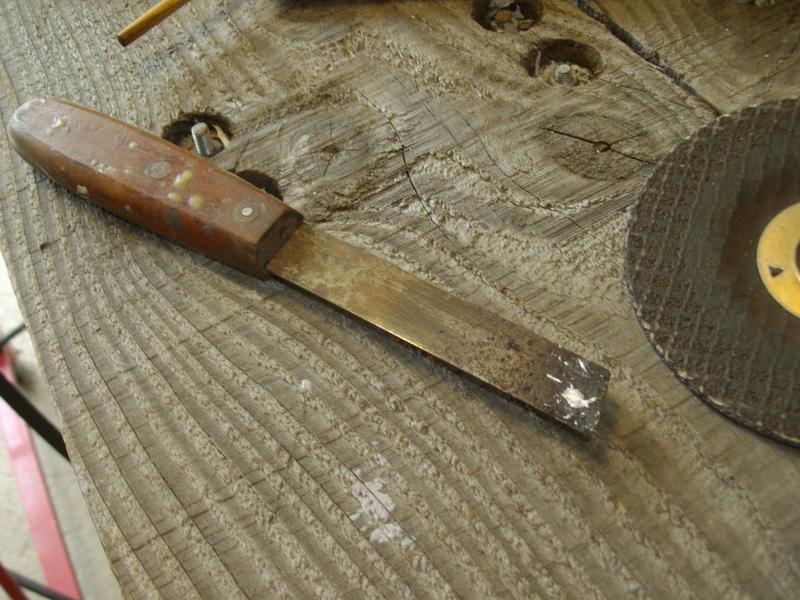
après en avoir déposé grossièrement avec la barre d'étain.
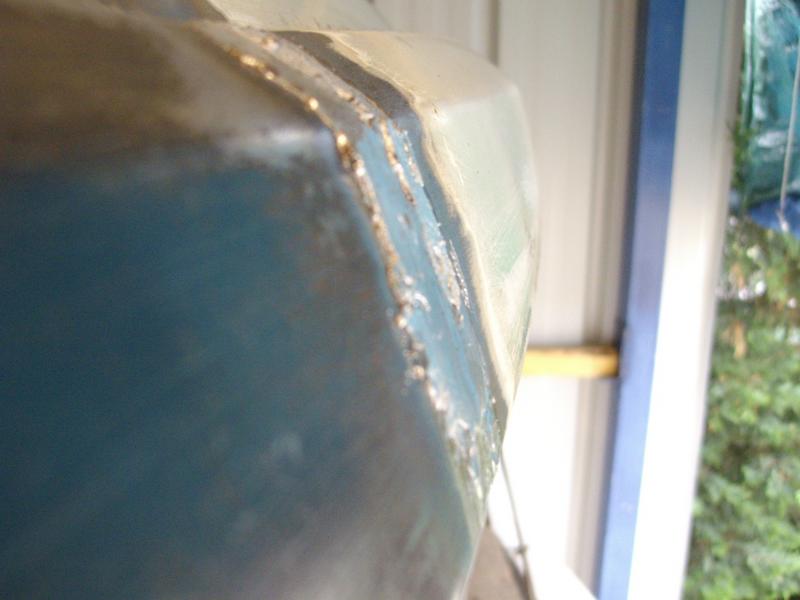
la, il ya une belle cuvette.
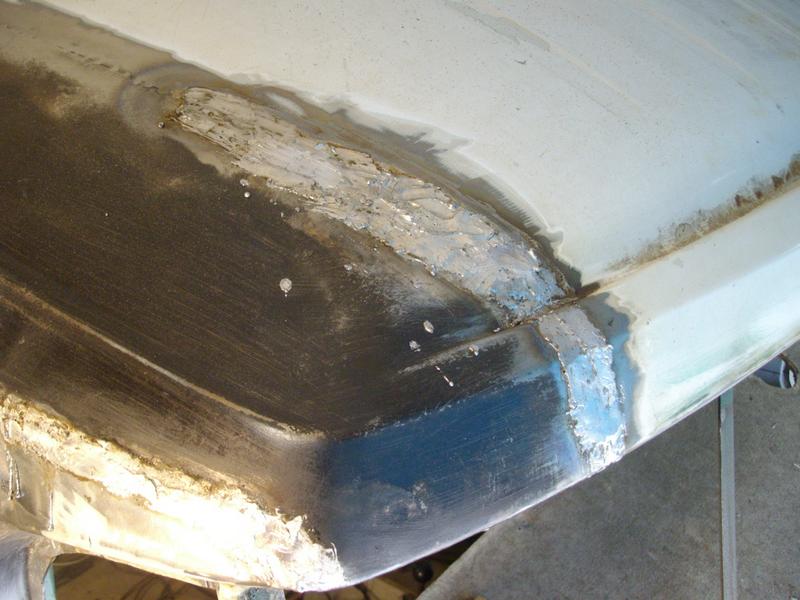
bien étanche le final de la gouttière...
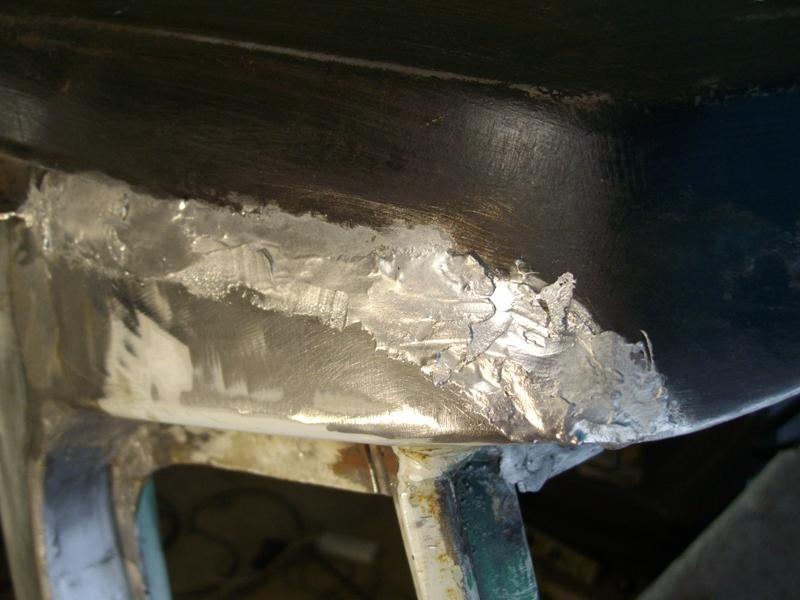
fin de la jonction avec la baie de par brise
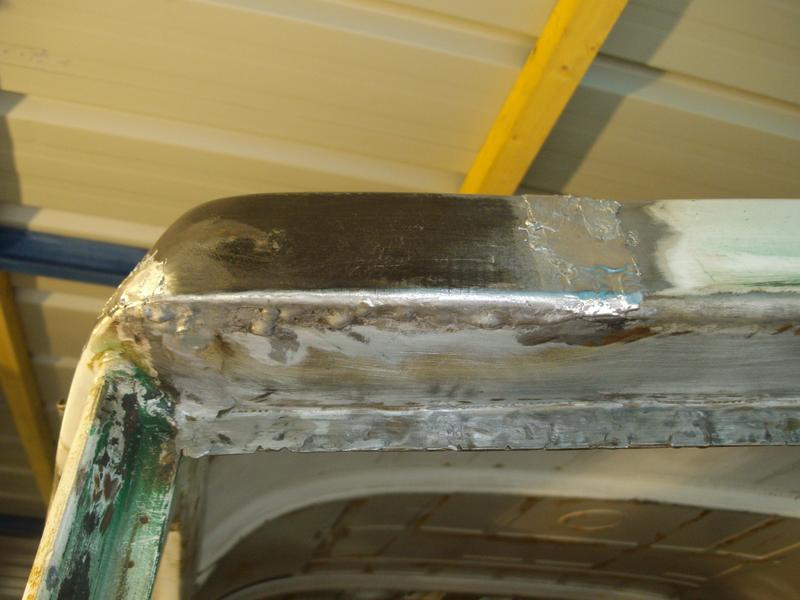
et la dernière ligne courbe !
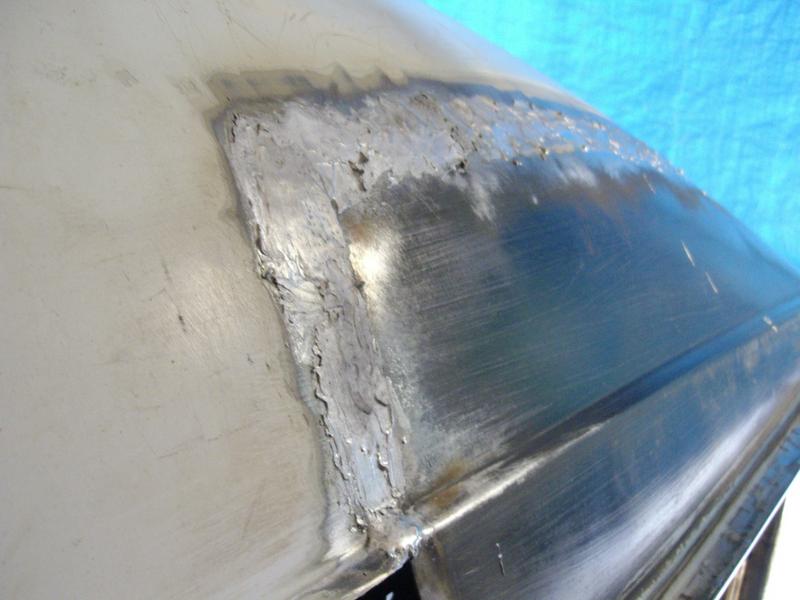
je suis tombé sur des barres, dont le pourcentage était inférieur à 33%, et impossible a travailler comme cela, on a beau chercher le point de fusion, ça coule direct !
et on suit toujours le meme principe, dégrossir avec le disque à lamelles et un grosse lime métal .
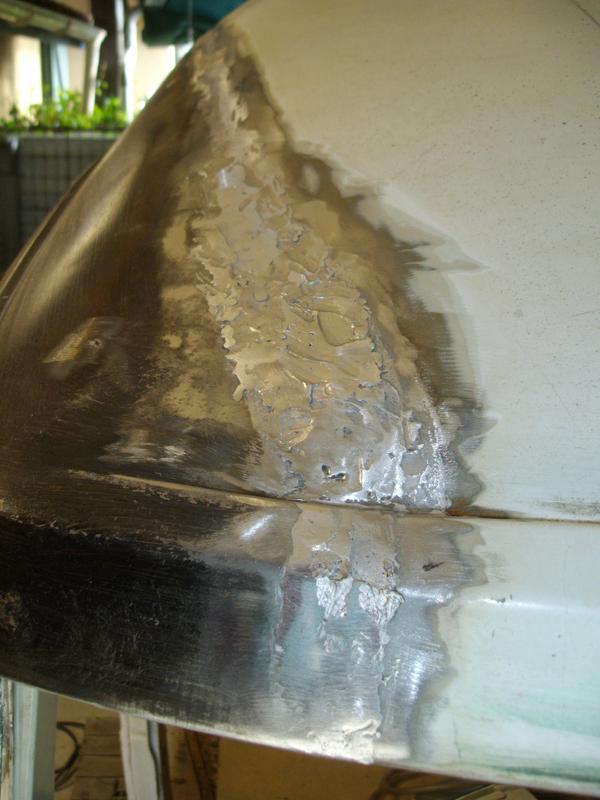
et finir avec une cale à poncer et de la toile émeri de différent grain.
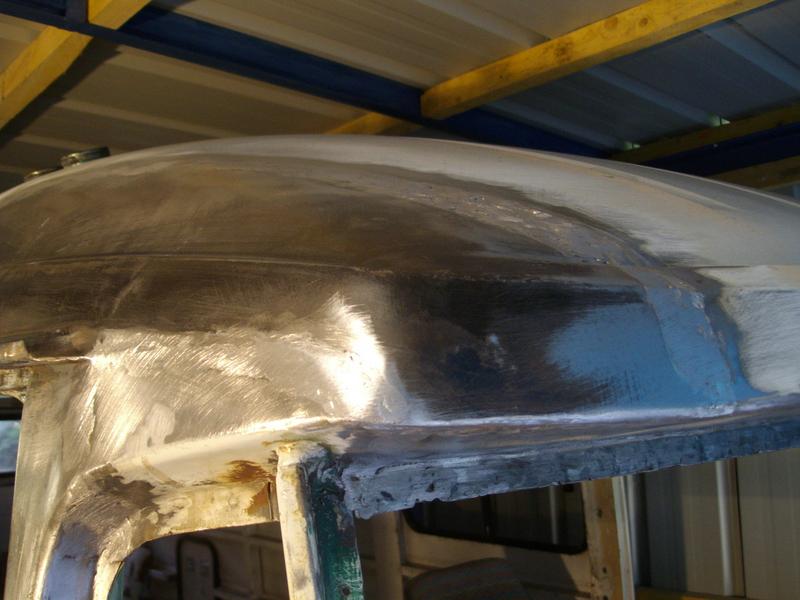
ça permet de conserver uniquement l'étain qui se trouve sous les points les plus haut de la tole.
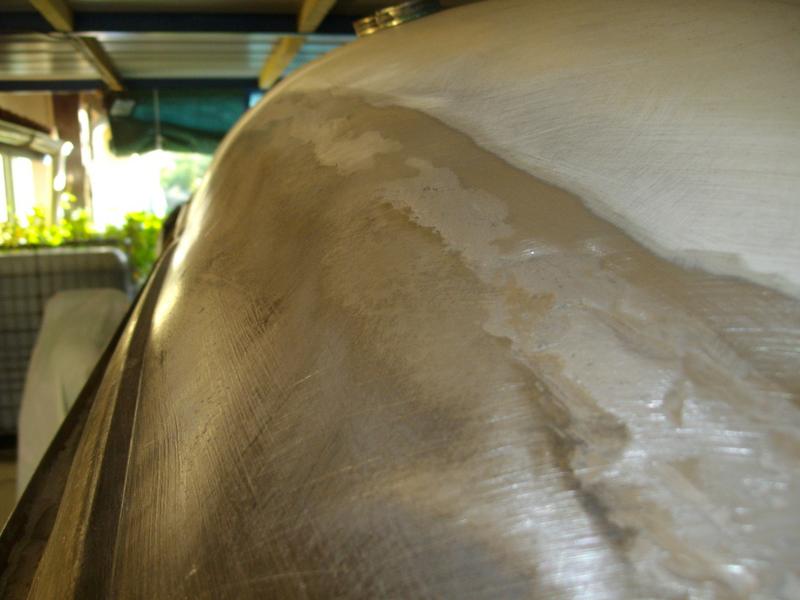
et forcément, si on insiste trop.. la tole se découvre. éviter que cela se produise entre les points de soudure.
voila, ça devient rébarbatif dans le principe. alors ya plus qu'a ce lancer dans la pratique et sauver durablement ces vieilles structures.
Dans l'exemple de ce fourgon, les gouttières doivent être perforées depuis un moment et les infiltrations d'eau l'ont oxydé en profondeur. Mais dans tous les cas, mettre de l'énergie à équiper un fourgon dont la carrosserie n'est pas saine, c'est ce condamner a rendre impossible ce genre de travail et la certitude que quelques années après, il faudra sortir le mastic fibré...
il faut bien avouer que pour une restauration complète, évaluer le temps de taf est compliqué et cela demande un minimum d'outils et une structure conséquente.
mais pour des réparations plus ponctuelle, comme un passage de roue ou une partie de gouttière, si le greffon est préparé a l'avance, en apprenant trankilement, deux jours suffisent.
juste un petit dernier, pour ceux qui ne serai pas convaincu de la nécessite de traiter correctement les corps creux.
celui du montant de portière c'est arrêté au niveau de la charnière supérieure... en dessous, vu de l'intérieur de la cabine, mis a part les trous fait à l'arrache, c'est pas trop moche.
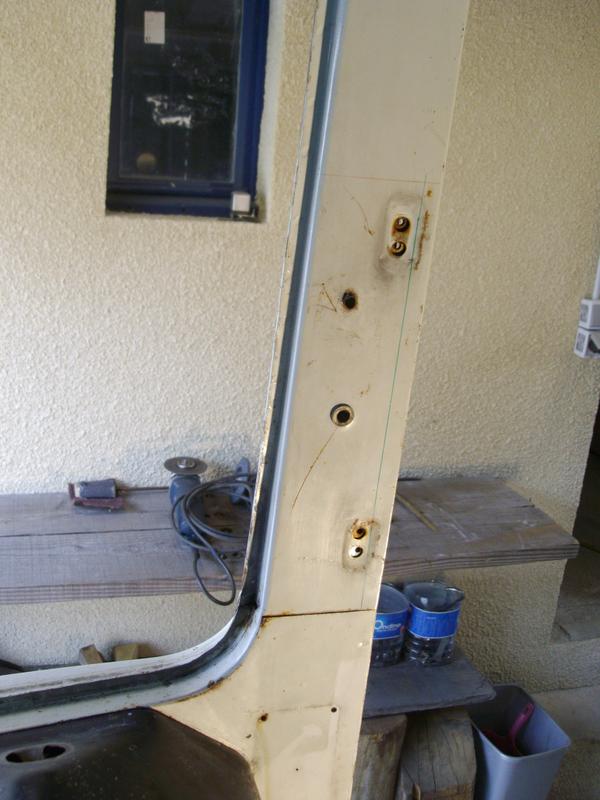
et pourtant, la disqueuse est quand même venue s'y frotter
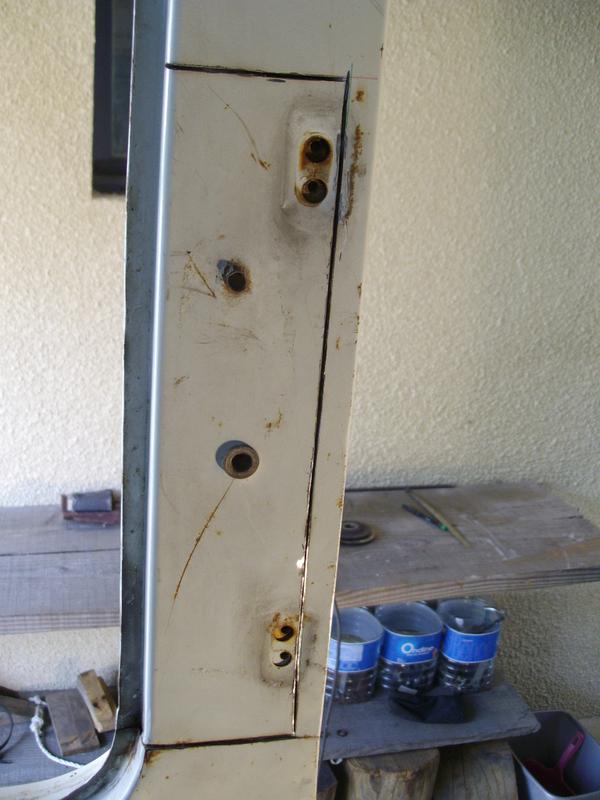
et pas pour rien !
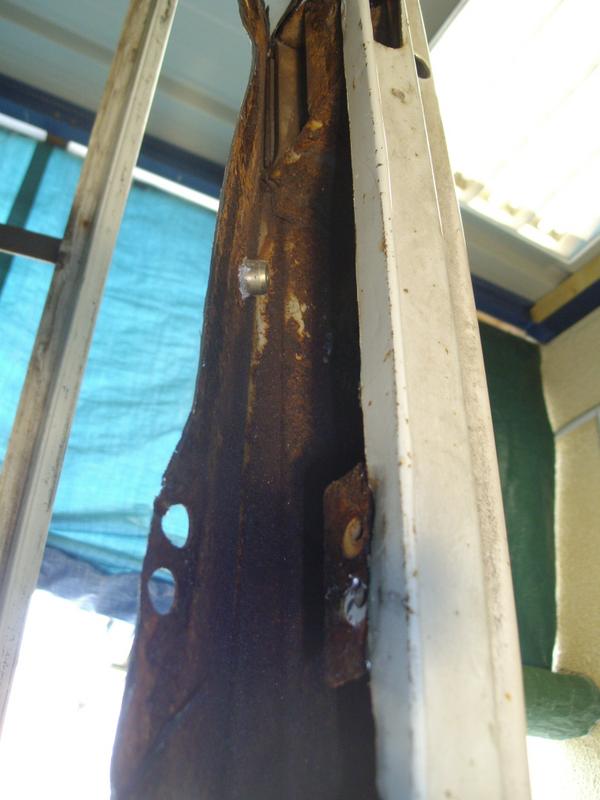
je précise quand même que traiter les corps creux ne veut pas dire systématiquement découper de la tole !, un trou suffit à passer le flexible de la bombe ( ou cartouche sur pistolet protection chassis ) et pulvériser la cire quand l'oxydation n'est que superficielle.
il faut avant aspirer (ou souffler) le maximum d’impuretés.
ici la découpe est évidente vu l'état général du fourgon...
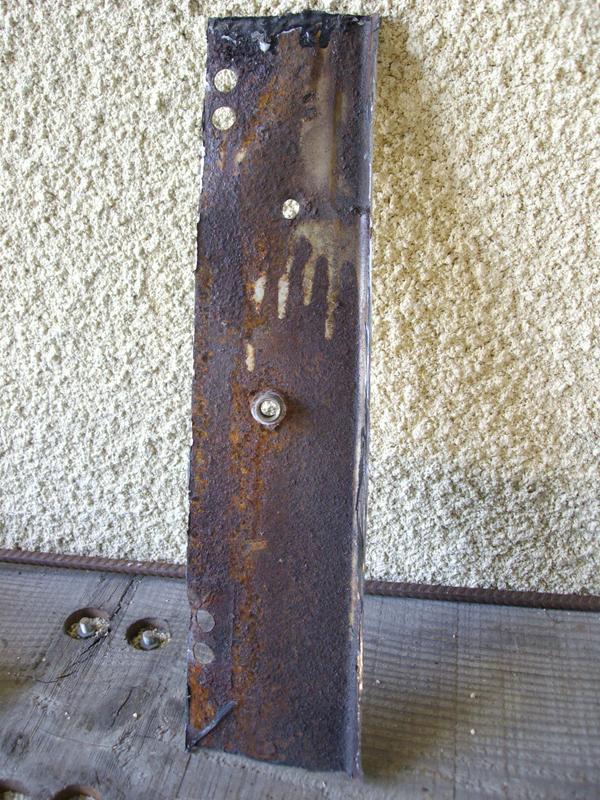
ça permet aussi d'avoir accès à la plaque flottante pour le serrage/réglage de la charnière de porte
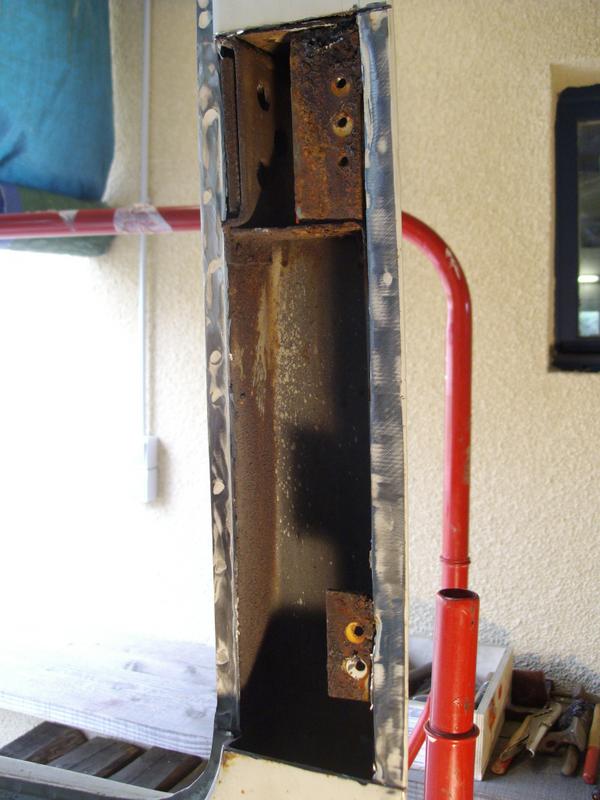
la disqueuse à lamelles passée sur les montants soudés pour faire apparaitre les points de soudures de la partie découpée.
sur la peinture, le résultat est facile !
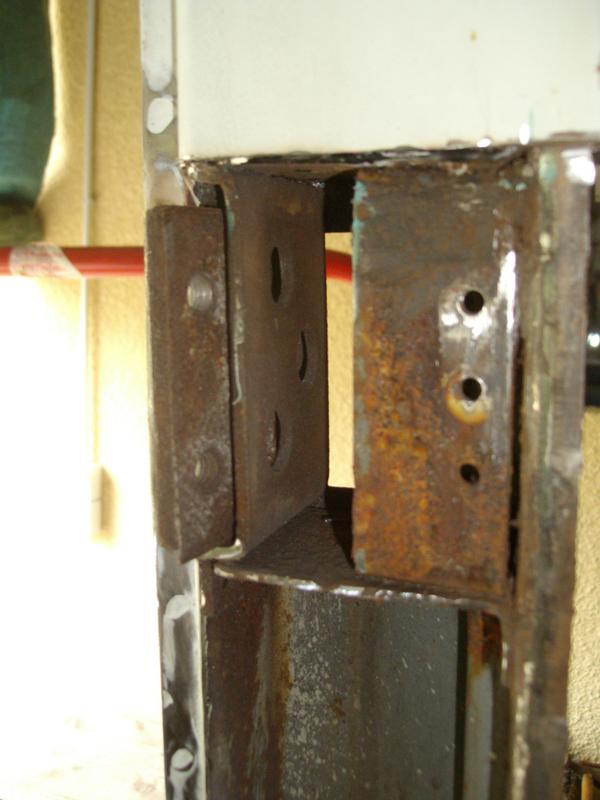
pour ceux qui qui veule faire connaissance avec la plaque flottante...
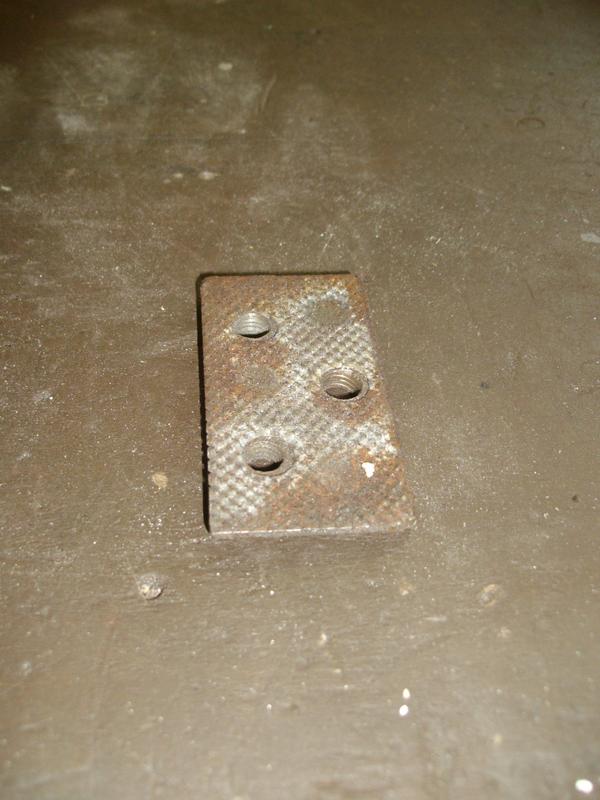
donc ya plus qu'a meuler sur et autour des taches blanches... une routine maintenant.
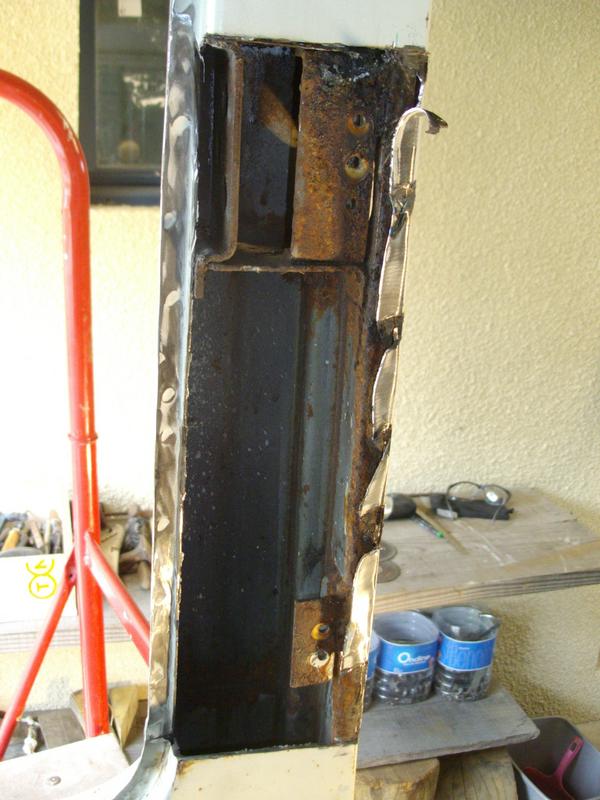
ici pas possible de soulever la taule au fur et à mesure que l'on fait sauter les points de soudure ( pour découvrir plus facilement les contours du prochain point a meuler) car la tole est repliée sur l’arrête du montant !
mais ça dégage pareil
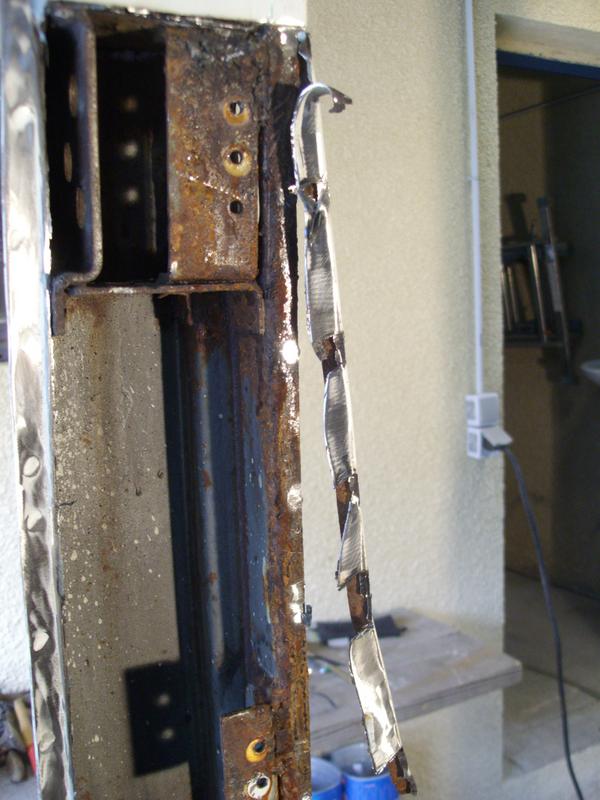
et le résultat est le même !
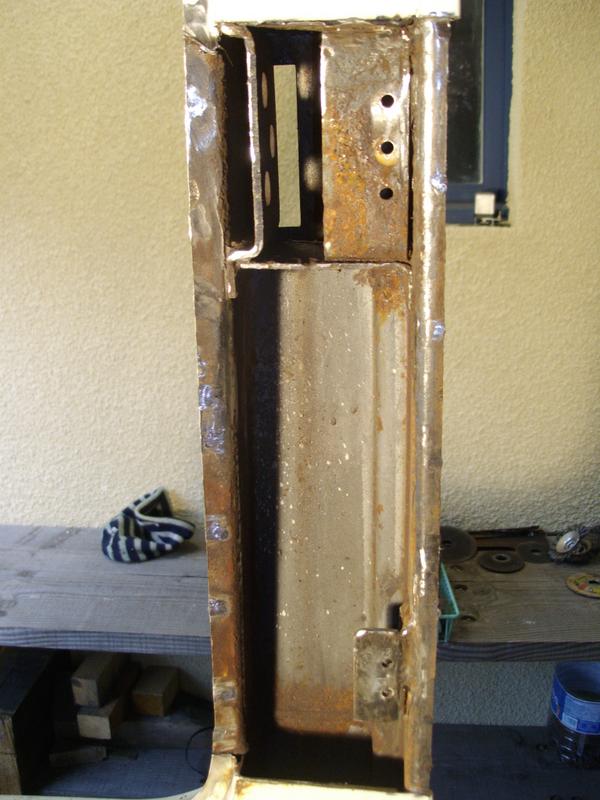
et plus on descend vers la charnière de porte inférieure, moins c'est oxydé. dans cet état, la cire peut être pulvérisée directement ( sans grattage ).
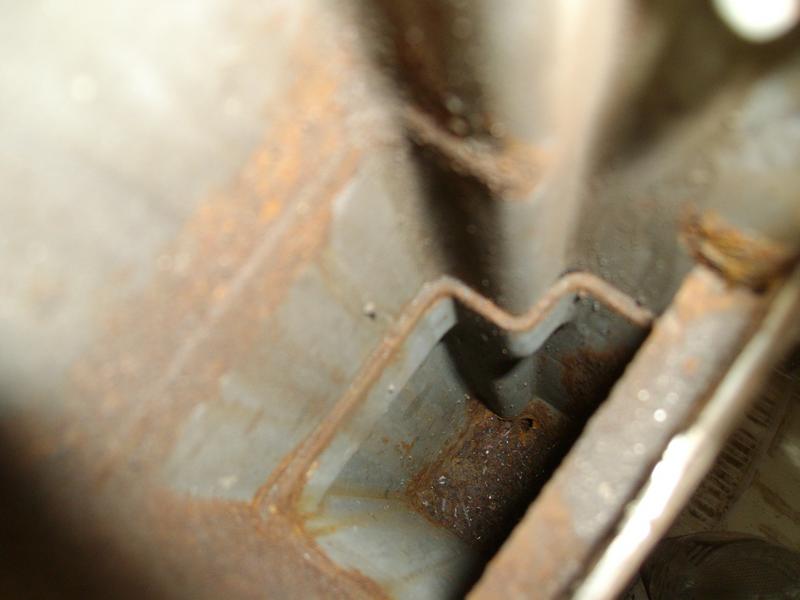
après juste un coup d'aspirateur, le fond c'est que du superficiel
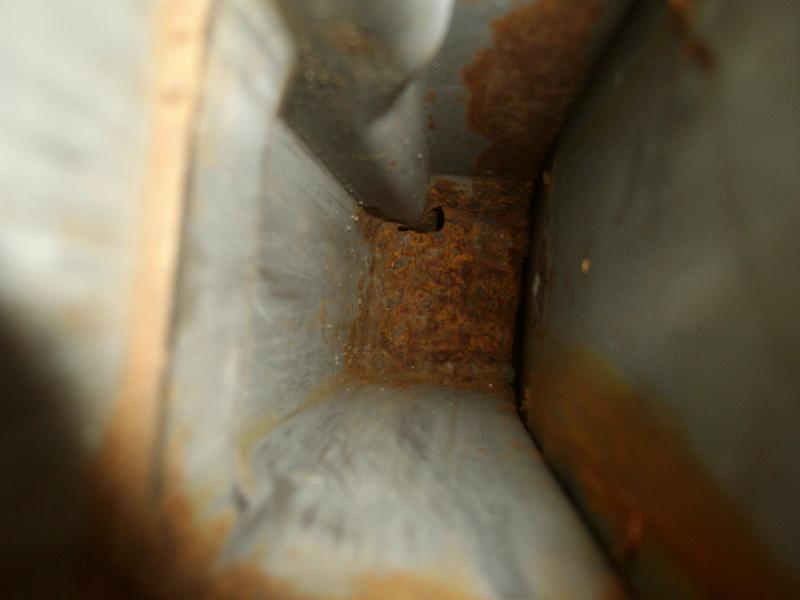
la découpe étant faite, la protection suit le même principe... donc ponçage grossier de l'intérieur du montant avec un outil éphémère.
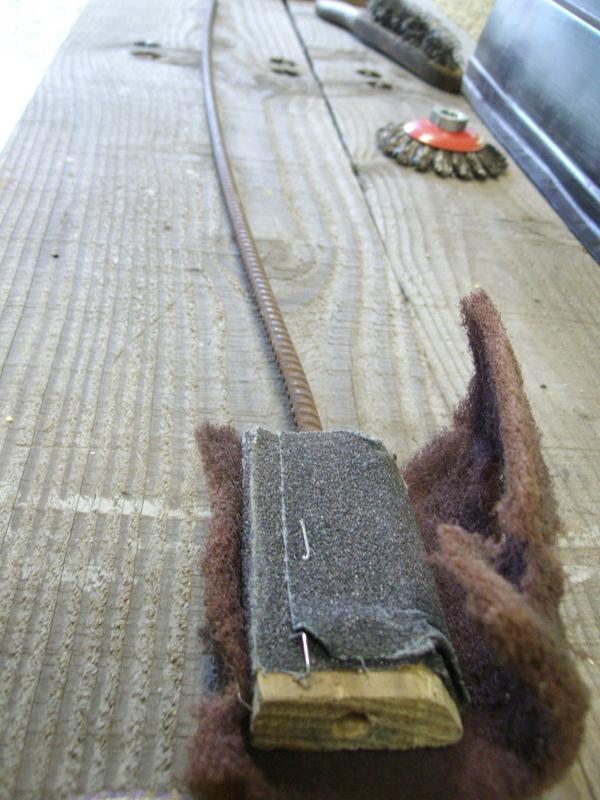
comme d'autres avant lui
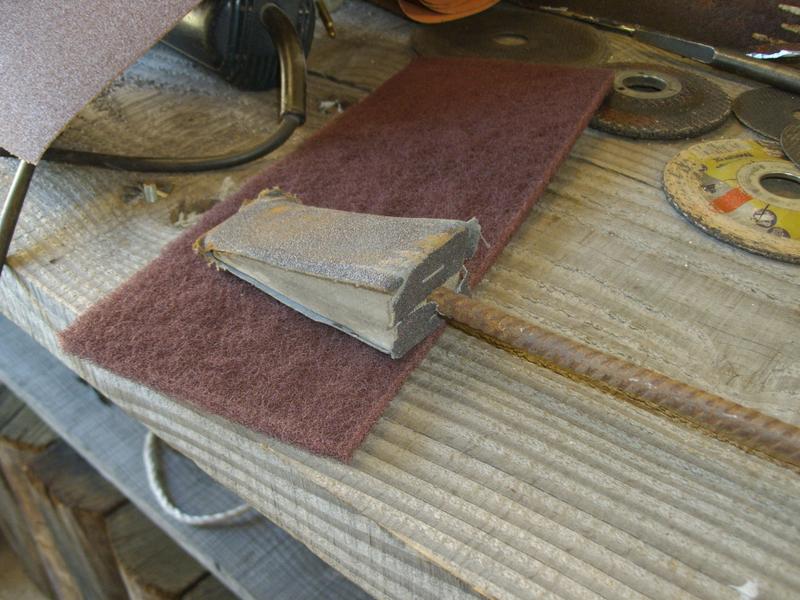
grattage, ponçage et autres... de la structure peu accessible de la charnière
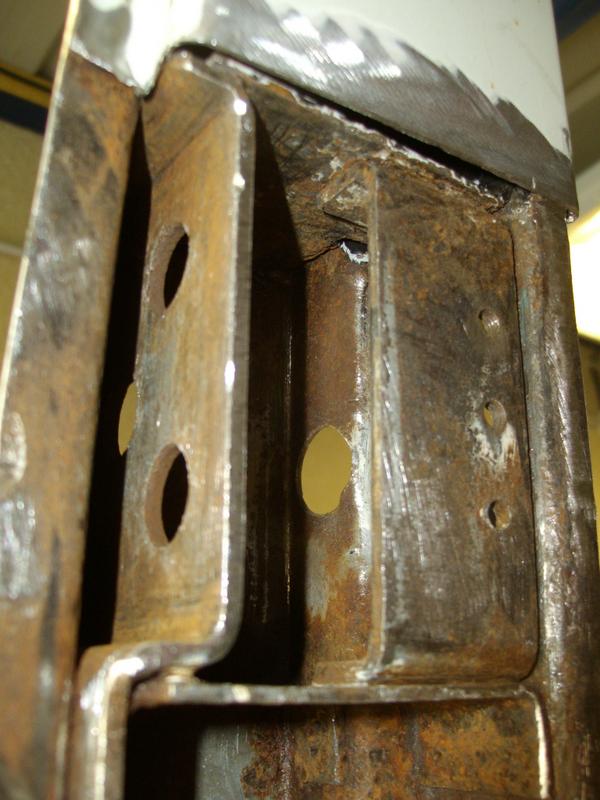
et pour le débat entre rustol et frameto, bin perso j'utilise les deux.
tout ce qui est superposition de tole, c'est pour le rustol qui pénètre bien la rouille par capillarité.
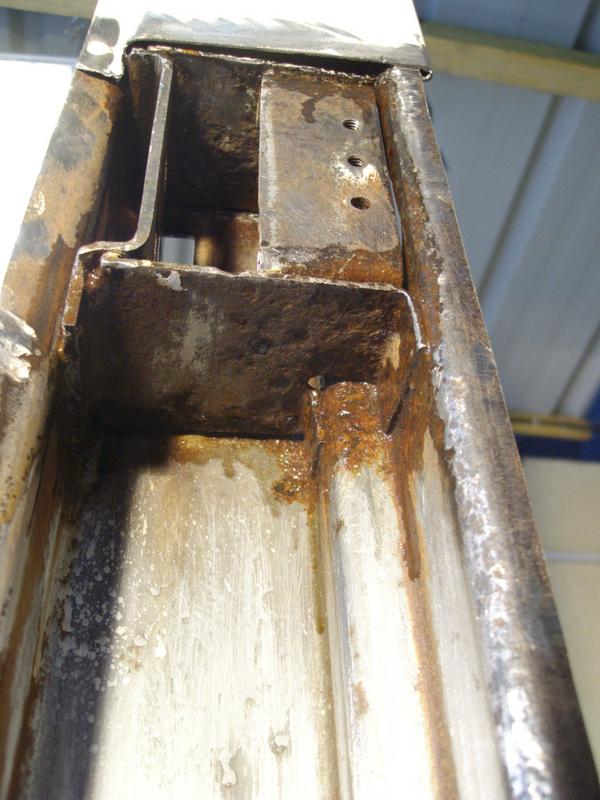
et pour les surfaces oxydées , c'est le frameto qu'il faut passer une fois le rustol sec.
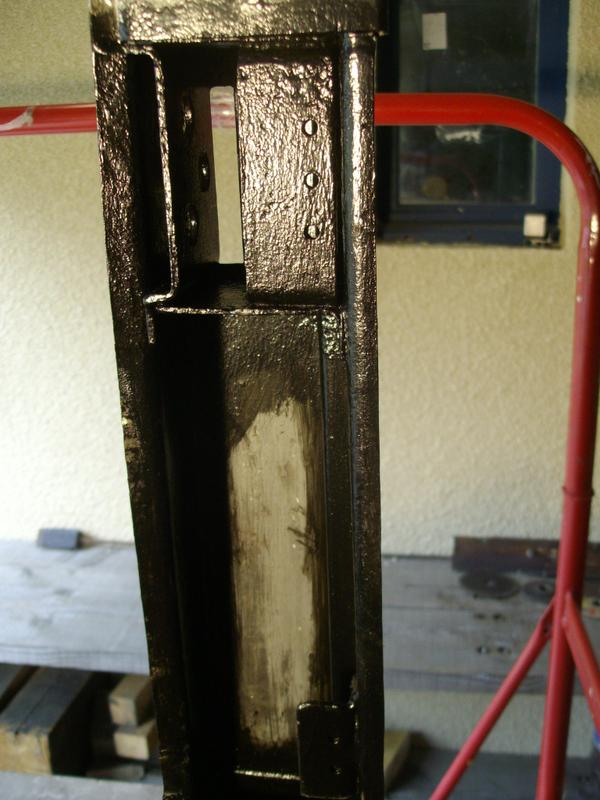
puis dépolissage de la surface avant de recouvrir de peinture glycéro au pinceau.
Pour l'impression phosphatant, le diluant fait réagir le frameto, il faut donc changer le frameto pour du rustol CIP que l'on peut passer au pinceau ou en pulvérisation sur les surfaces oxydées.
mais avant, petit retour sur les patrons en carton.
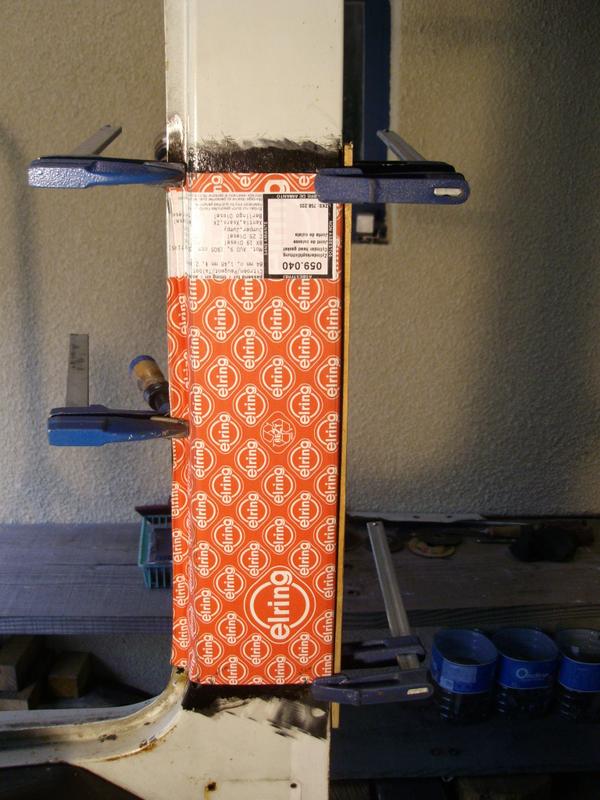
que l'on déplie sur une tole. (encore un plus pour les toles de bardage qui ont des pliures déjà faite !).
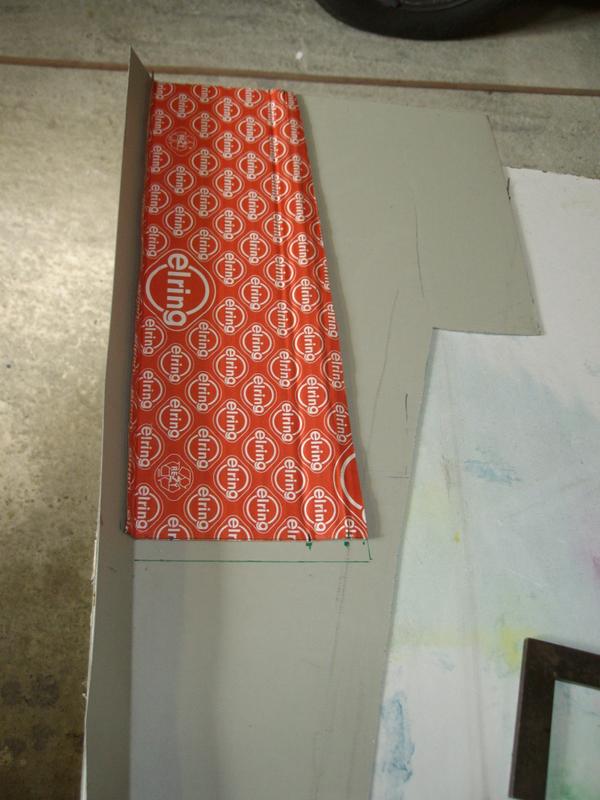
pour marquer le contour et repérer précisément les endroits à plier.
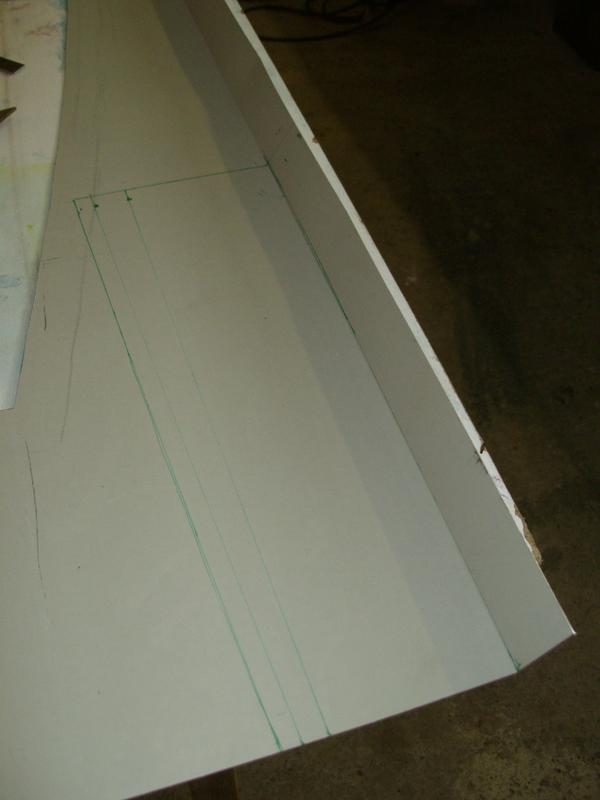
découpe des contours ( disqueuse ou scie sauteuse suivant la situation )
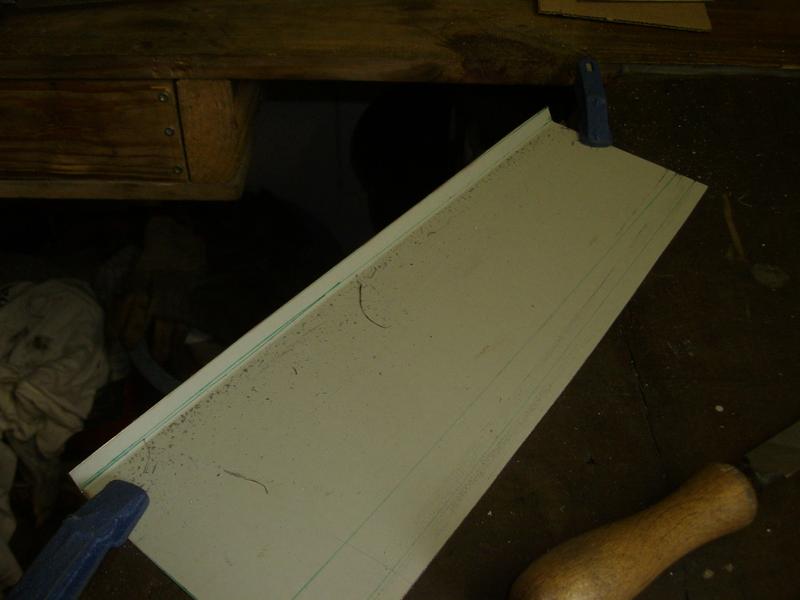
et le pliage de la partie recourbée sur l’arrête du montant peut commencer
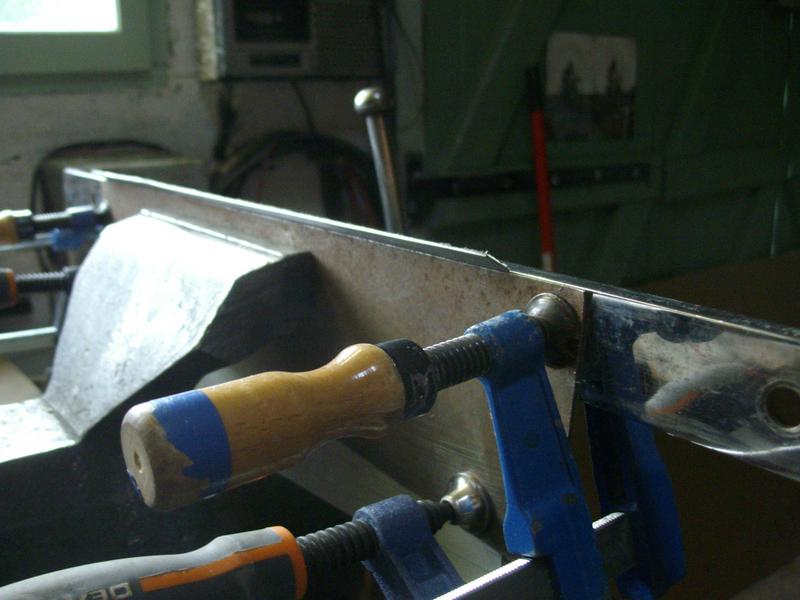
progressivement comme dab...
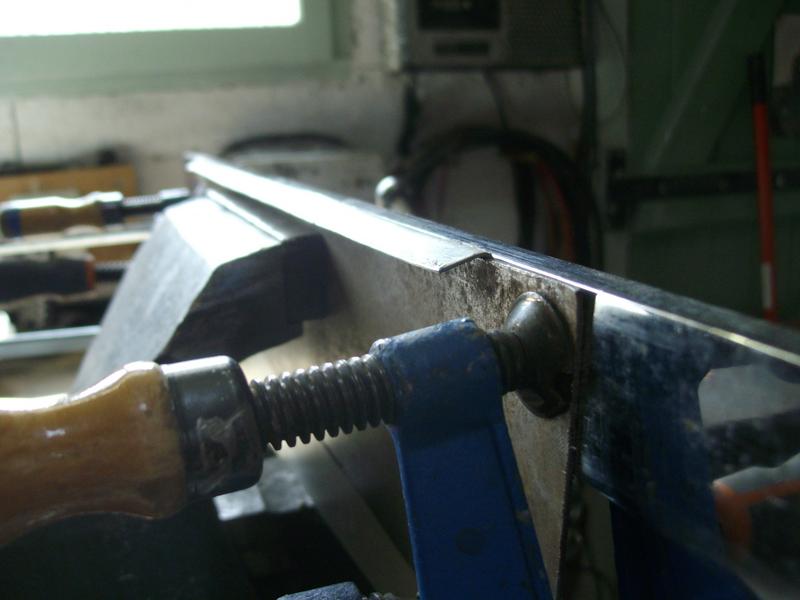
et au final, une jolie pliure
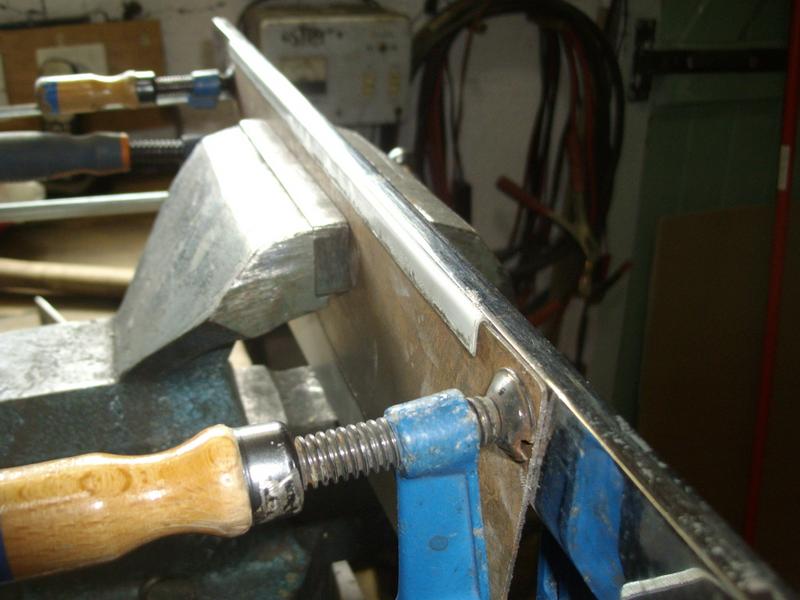
qui donne une bonne référence de positionnent pour la suite
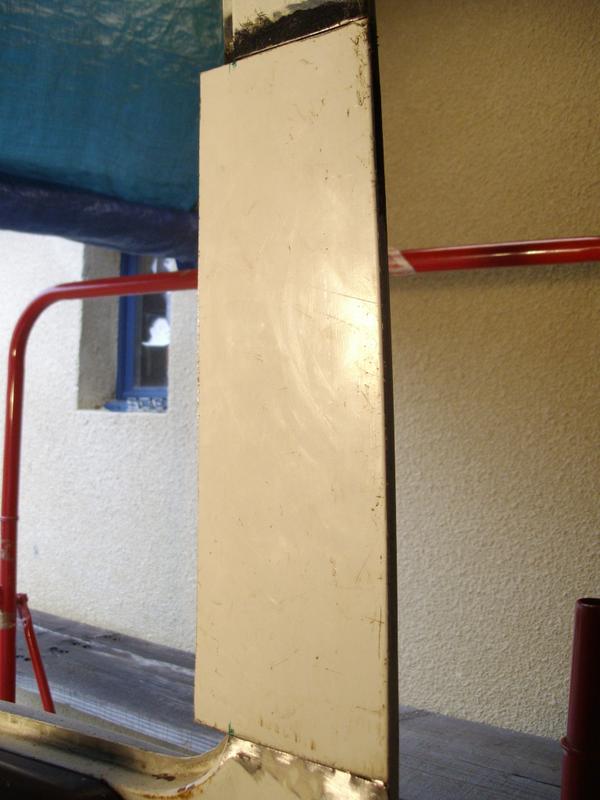
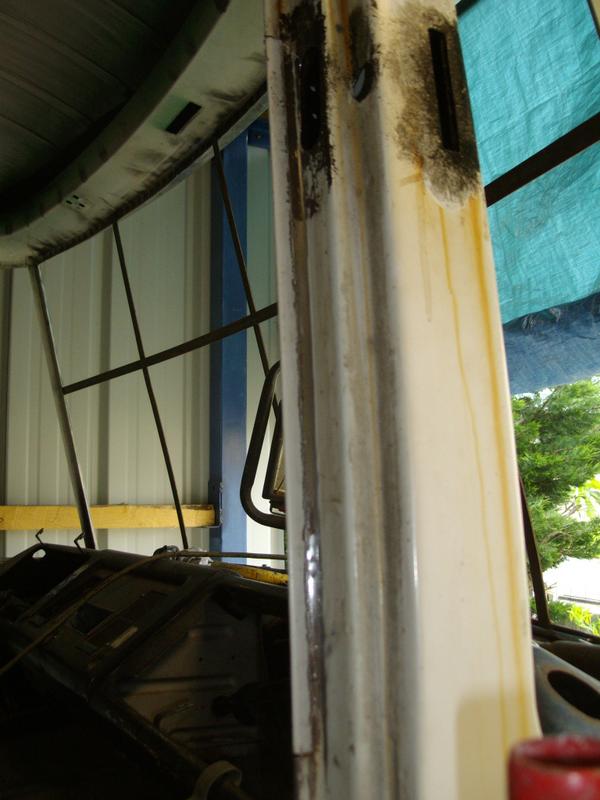
ponçage
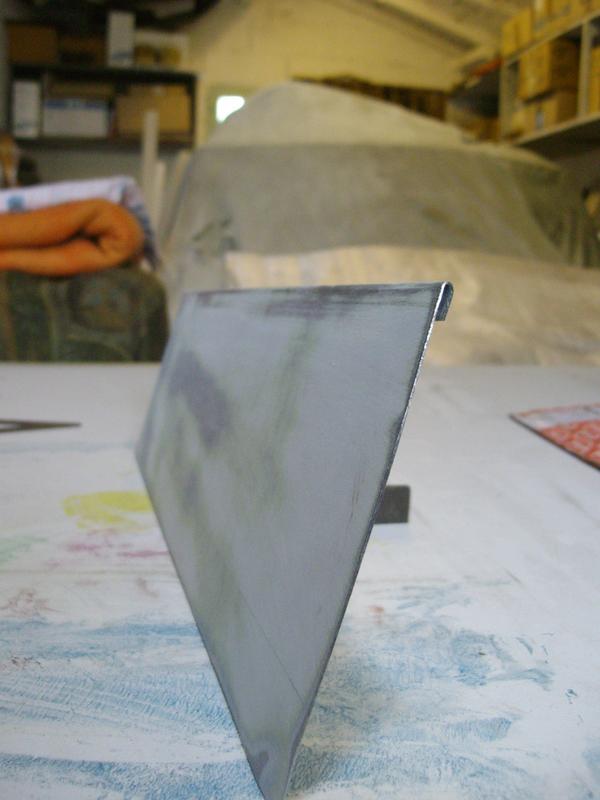
vérification que les repères pour le pliage sont corrects et marquer l'indexage de la pièce par rapport au montant
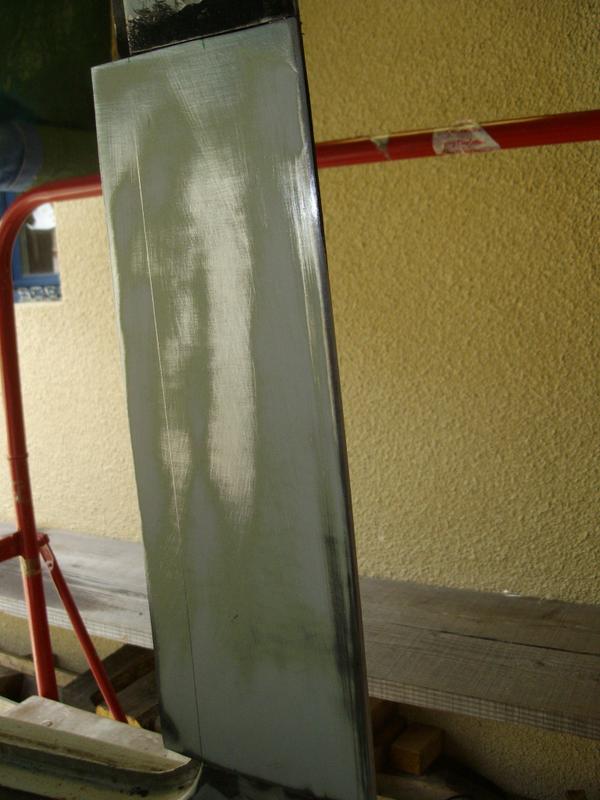
avant de la remettre dans l'étau pour une nouvelle séance de pliage. c'est tellement prenant que j'ai pas fait de photos !
juste le résultat
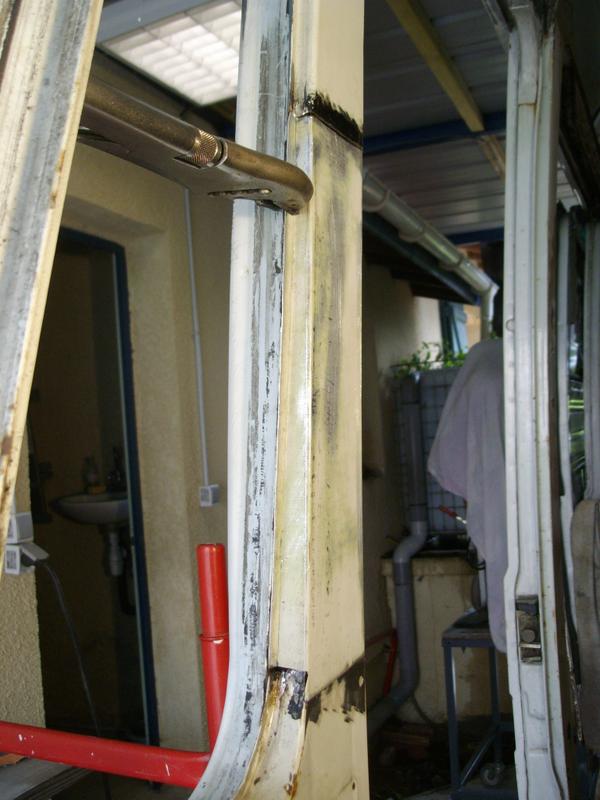
qui demande encore quelques ajustement. et oui, le carton est plus facilement comprimable que l'acier...
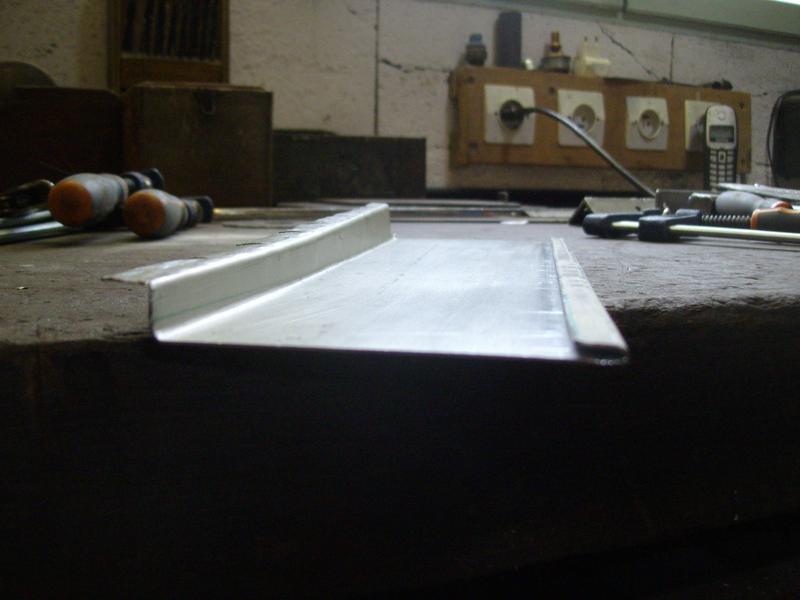
mais au final, la pièce est la
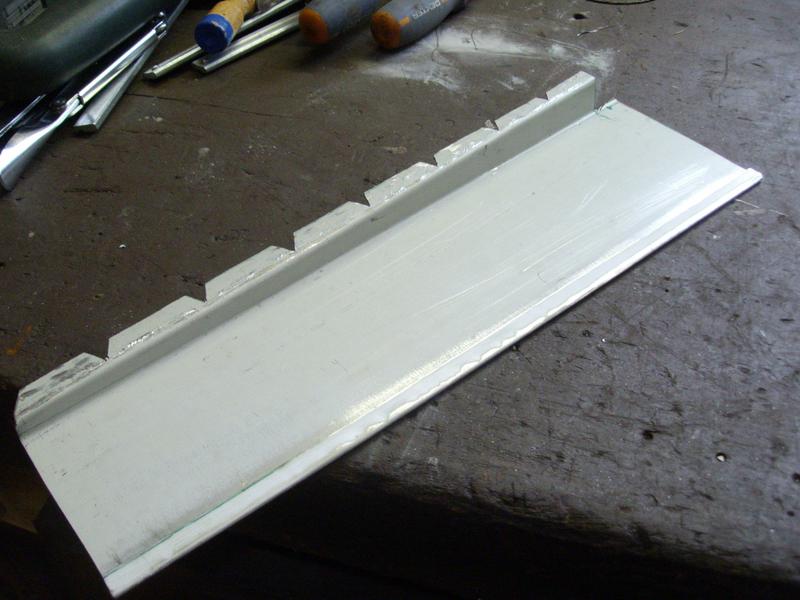
prête a être soudée
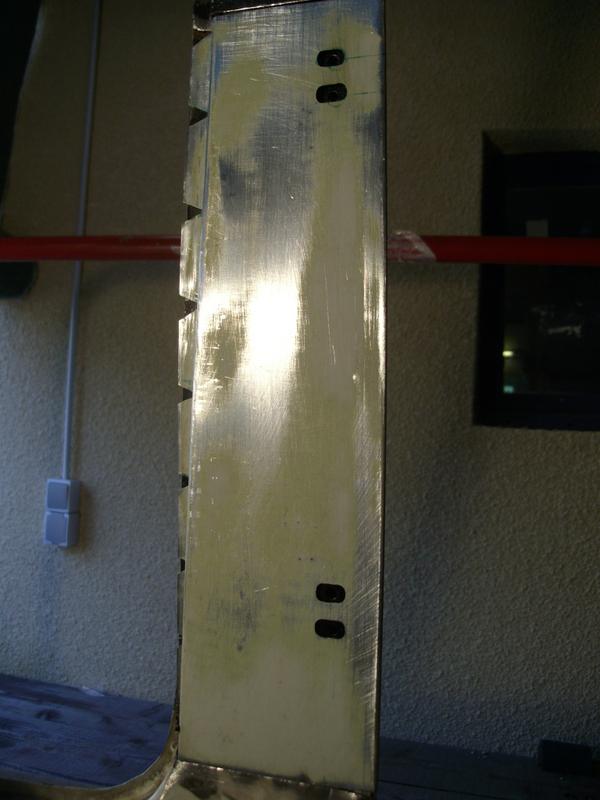
sauf que pendant le grattage du montant, j'ai repéré un petit passage ( bouché par un bout de mousse d'origine ) qui communique avec le corps creux de l'aile avant. ce passage vas permettre de pulvériser la cire après soudure... mais encore faut il y avoir acces par l'autre coté !
c'est bientot fait...
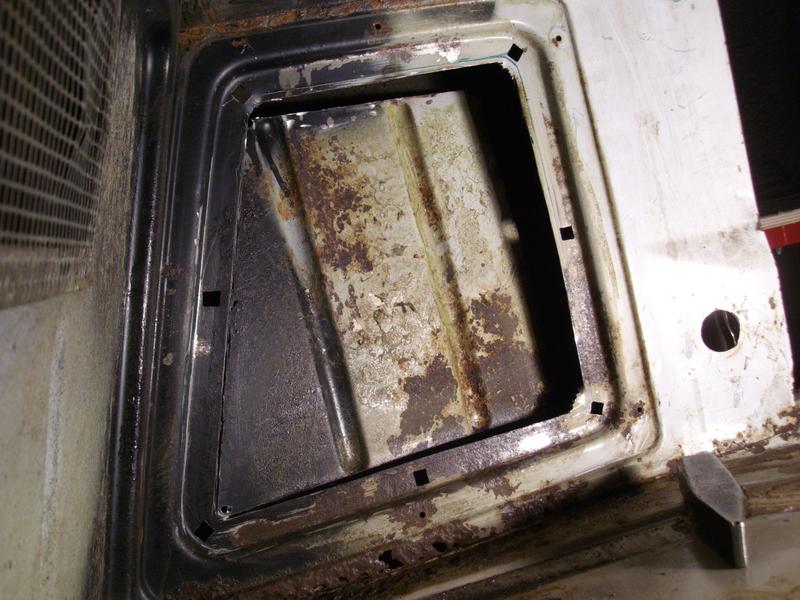
avant, le marquage de la découpe de la trappe est fait sur une feuille souple, tenue avec des aimants.
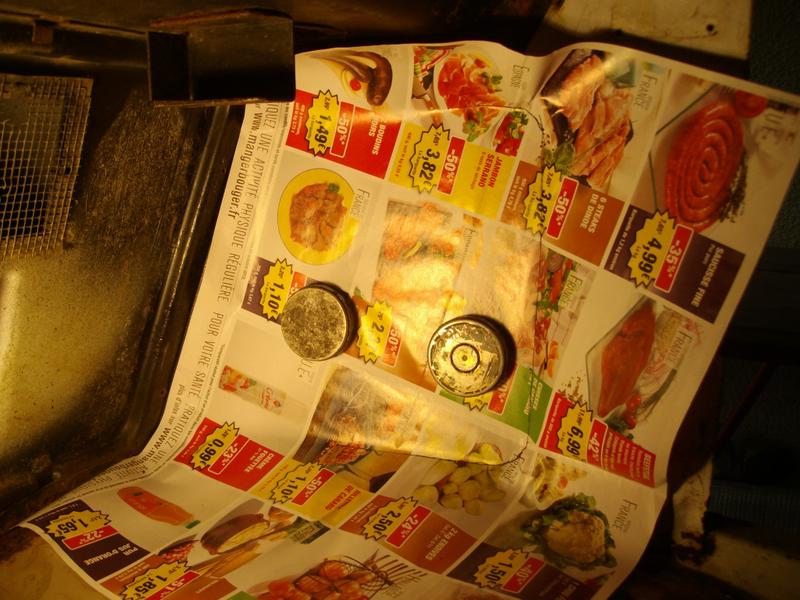
puis collé sur un carton pour vérifier les dimensions de la découpe,
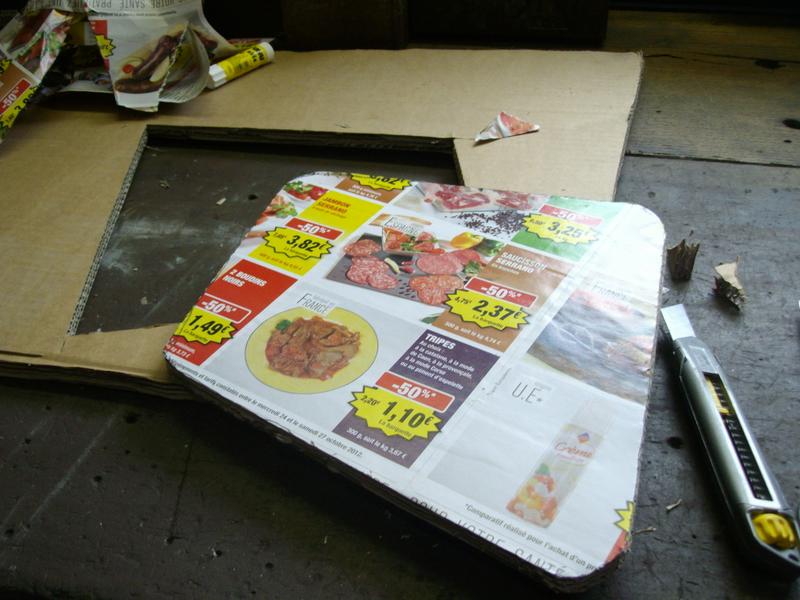
et faire un tracé précis sur la plaque à découper
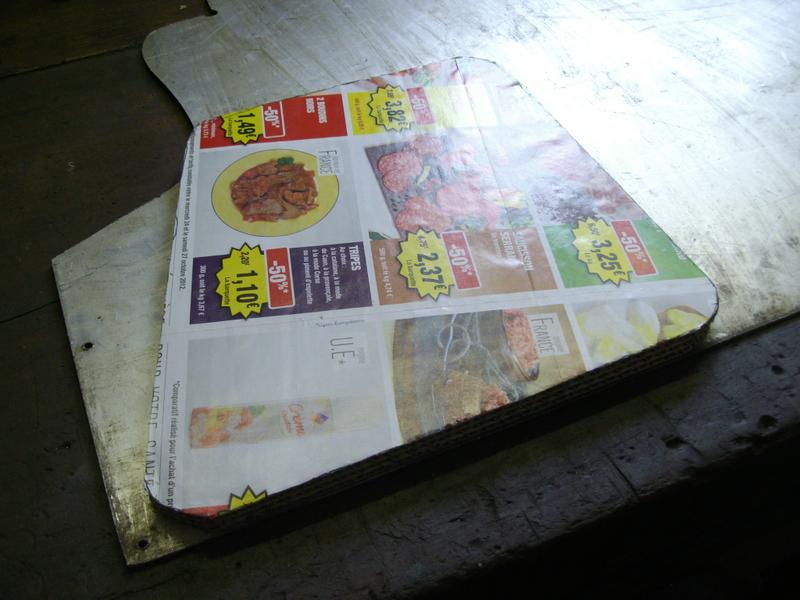
et derrière la découpe, avec un peu d'idées, ya un volume à exploiter !
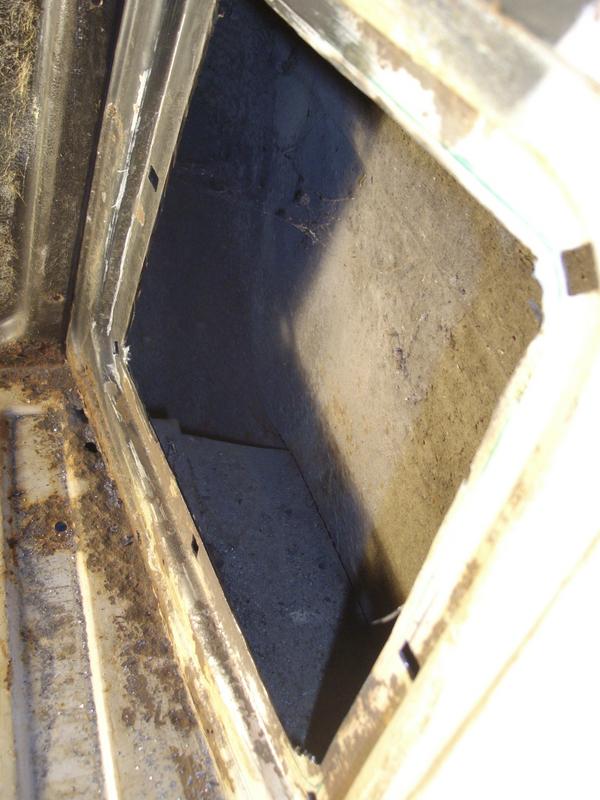
donc découpe des fenêtres pour les écrous prisonniers, avec au passage un trou pour faciliter la découpe finale des coins, qui se fera avec un petit burin bien aiguisé ou un ciseau à bois.
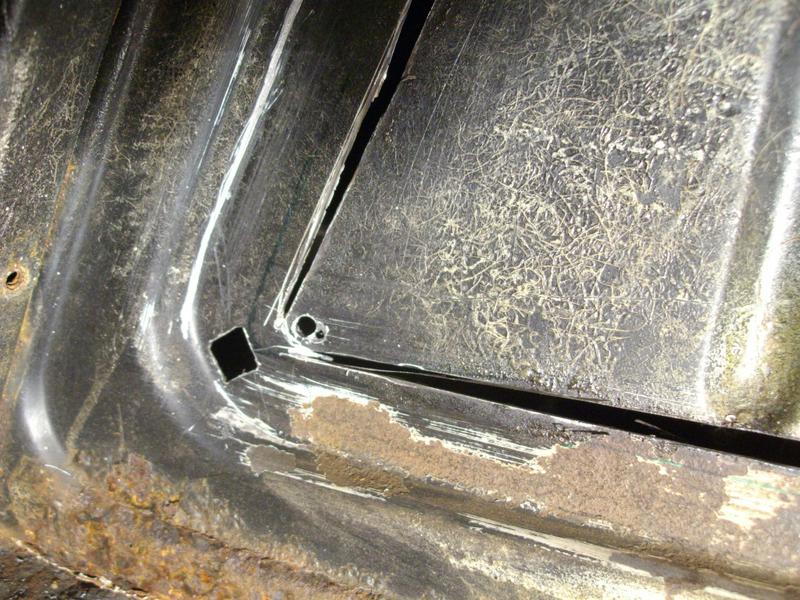
résultat de la manip
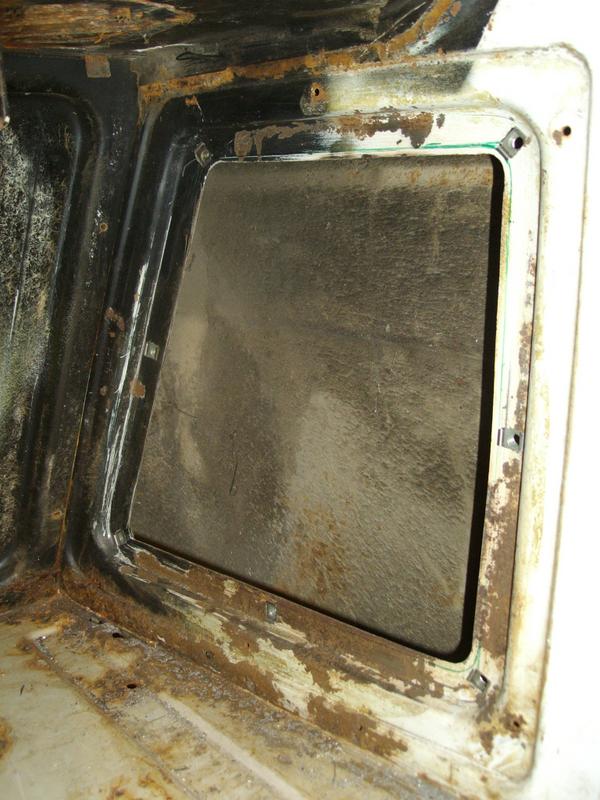
les écrous prisonniers
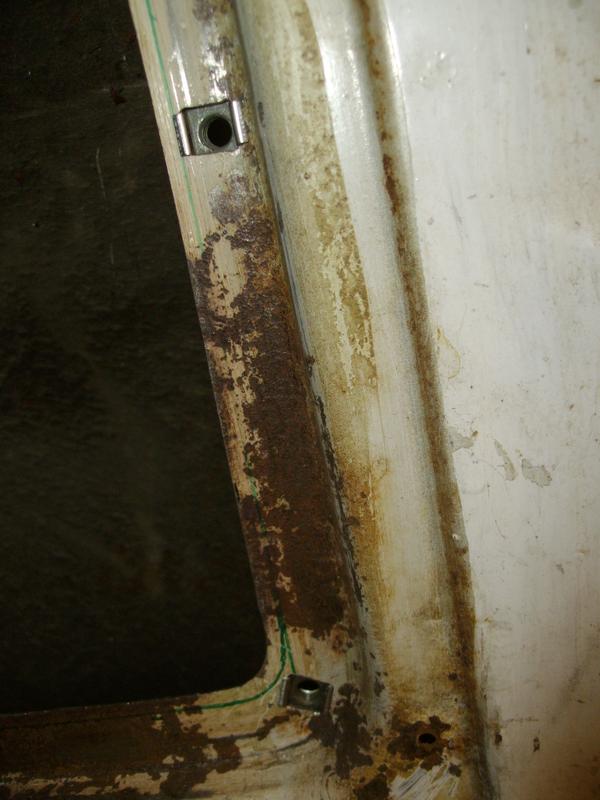
dont le but est, mis a part le volume, d'avoir accès... au dessus du bloc optique
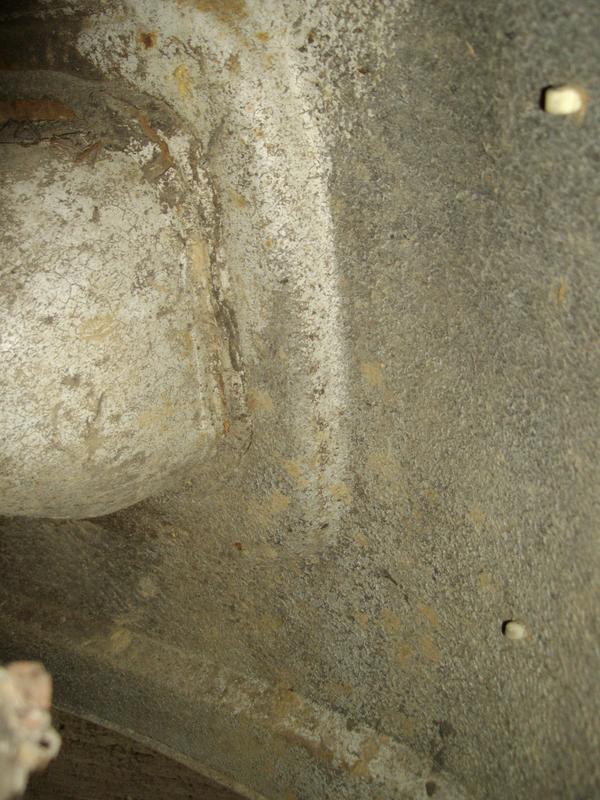
à la deuxième plaque flottante pour le serrage/réglage de la charnière inférieure
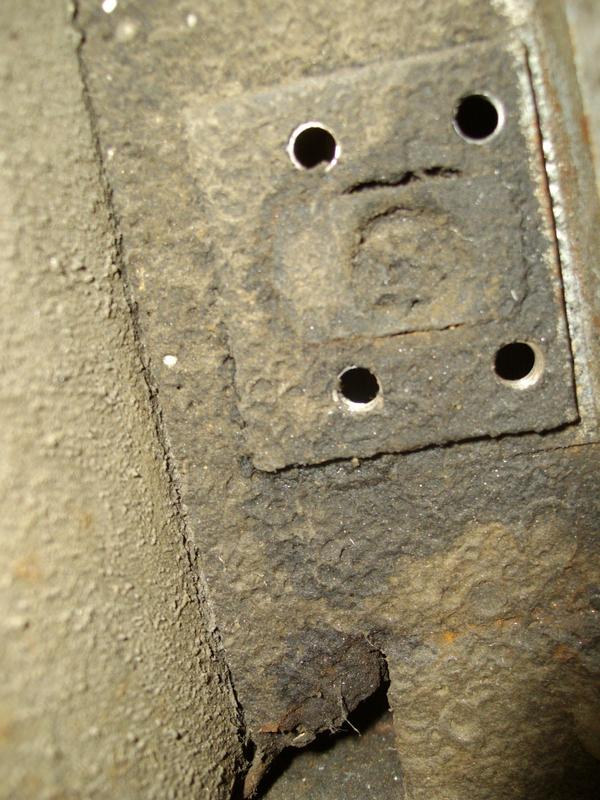
et au petit passage qui permettra de glisser le flexible de la cire corps creux, pour traiter, après soudure de la pièce, l'intérieur du montant .
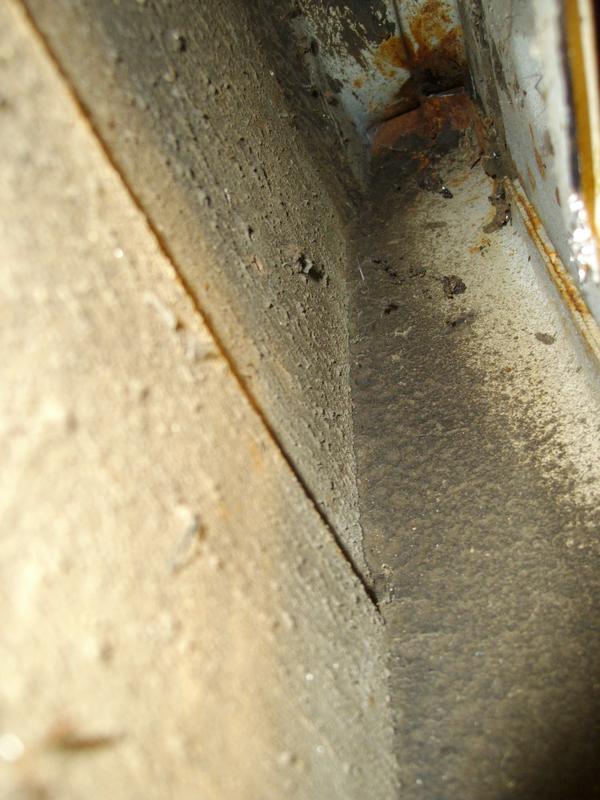
une fois fait, on refermera...
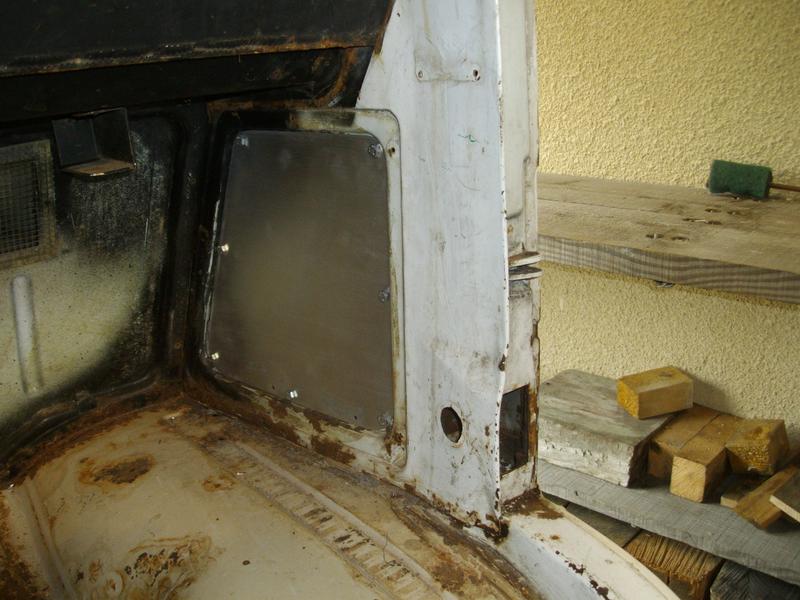
avec des vis têtes fraisées, ça devrai être mieux
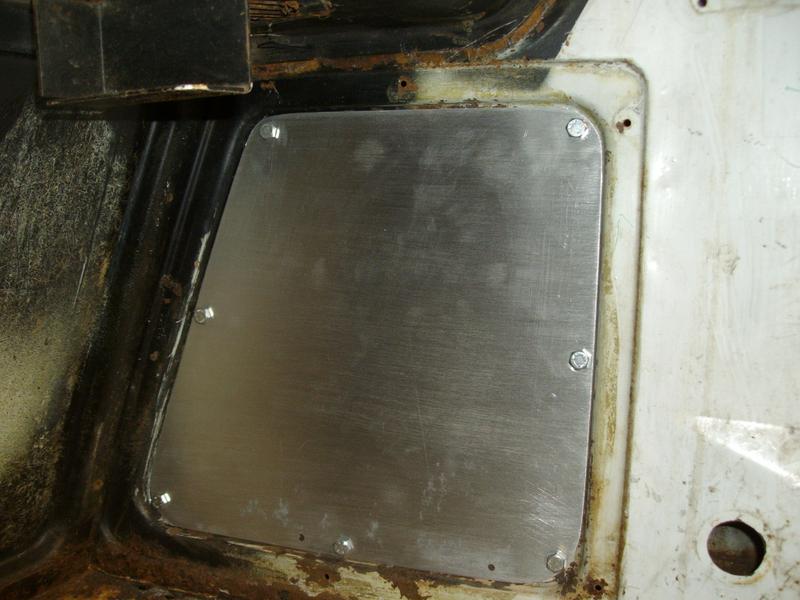
petit détail sans importance devant la suite... la même, mais à gauche !

ou

, chacun est libre de choisir !
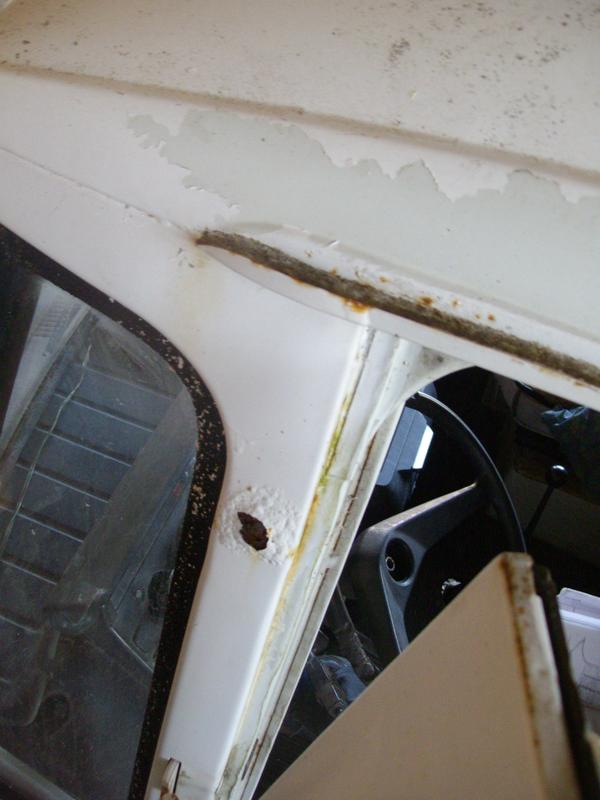
il faut de toute façon accepter que c'est très souvent symétrique ce genre de phénomène !
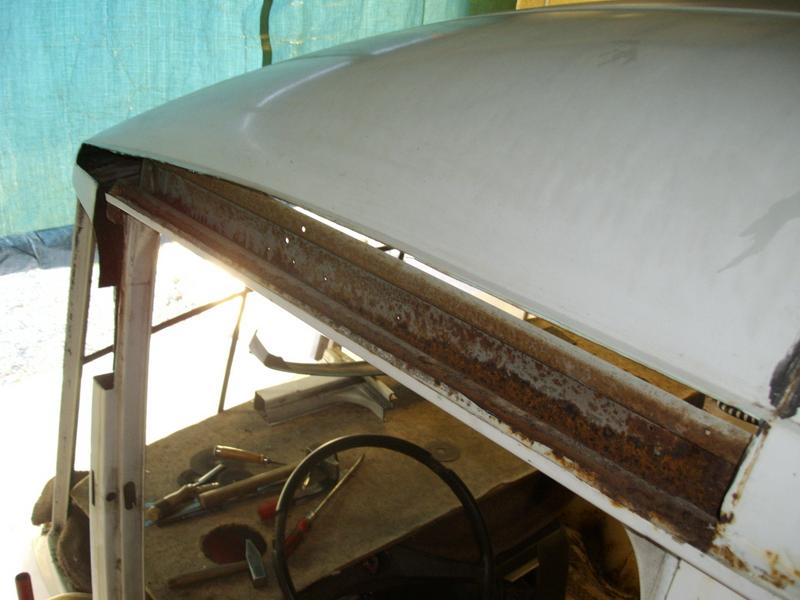
l’expérience du coté droit en plus, le petit bout courbé récupéré sur un caisse de 410 et ressoudé sur la pièce, bin je l'ai pas coupé !

mais je ne vais pas faire le tour du camion dans ce tuto... juste donner le principe d'une méthode que j'utilise pour me débarrasser de la rouille, sans avoir les compétences d'un carrossier.
une précision quand même sur le choix de cette méthode. Ce n'est pas l'achat du poste MIG qui est l’investissement le plus lourd, mais le gaz qu'il utilise ( Argon - Atal ).
avec l'achat du poste, il est proposé une recharge jetable... avec laquelle on ne fait strictement rien !
une bouteille rechargeable de 140L, on fini à peine un passage de roue, et c'est en moyenne 30 balles ( dans la grande distribution ) avec un détendeur simplifié mais pas trop chère !
le minimum à prendre, si on décide de ce lancer dans plusieurs points à traiter, c'est 1m cube ! et le maximum accessible pour nous, soudeur occasionnel, c' est en dessous de 2 mètres cubes !!
et oui, au dessus, on n'est plus propriétaire de la bouteille et les contrats de location proposé par les distributeurs de gaz, ne sont rentable que pour les pro.
un conseil donc, trouver le détendeur et la bouteille d'occasion avant l'achat d'un poste en grande distribution, ou bien un poste d'occasion.. avec la bouteille qui vas bien !
attention dans le choix du détendeur, le mano en sortie doit etre en "litre/minute" et non en "bars" !
pour le fil, même si les bobines ont un diamètre ridicule par rapport au poste professionnel, elles ont une durée d'utilisation correct et c'est entre 8 et 10 balles.
rien qu'une petite brise rend l'utilisation du poste difficile car le gaz protège moins la soudure... consommation du gaz encore augmenté en extérieur car il faudra augmenter le débit du détendeur.
aucune expérience avec les postes MIG à fil fourré... je laisse parler ceux qui savent.
plus le gaz protège efficacement la soudure, plus celle ci est pénétrante... et on a souvent besoin de poser la buse de la torche sur la pièce à souder, pour que la protection soit bonne mais aussi pour pointer plus facilement... méfiance, certains poste MIG sont vendu avec une buse non isolé.
tcho la tribe !